Passing Comments
Page 44
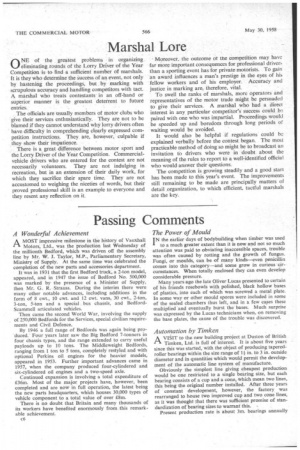
Page 45
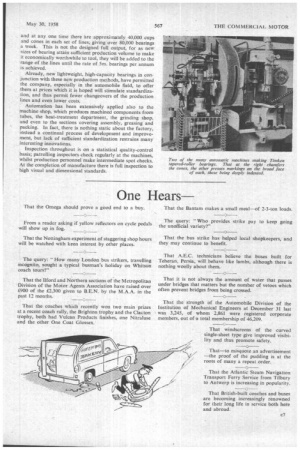
If you've noticed an error in this article please click here to report it so we can fix it.
A Wonderful Achievement
AMOST impressive milestone in the history of Vauxhall Motors, Ltd., was the production last Wednesday of the millionth Bedford, which was driven off the assembly line by Mr. W. I. Taylor, M.P., Parliamentary Secretary, Ministry of Supply. At the same time was celebrated the completion of the new parts and accessories department.
It was in 1931 that the first Bedford truck, a 2-ton model, appeared, and in 1947 the issue of Bedford No. 500,000 was marked by •the presence of a Minister of Supply, then Mr. G. R. Strauss. During the interim there were many other notable advances, including additions in the form of 8 cwt., 10 cwt. and 12 cwt. vans, 30 cwt., 2-ton, 3-ton, 5-ton and a special bus chassis, and BedfordScammell articulated vehicles.
Then came the second World War, involving the supply of 250,000 Bedfords for the Services, special civilian requirements and Civil Defence.
By 1946 a full range of Bedfords was again being produced.' Four years later saw the Big Bedford 7-tonners in four chassis types, and the range extended to carry useful payloads up to 10 tons. The Middleweight Bedfords, ranging from 1 ton to 5 tons, completely restyled and with optional Perkins oil engines for the heavier models, appeared in 1953. Further important advances came in 1957, when the company produced four-cylindered and six-cylindered oil engines and a two-speed axle.
Continued expansion is involving a total expenditure of .E36m. Most of the major projects have, however, been completed and are now in full operation, the latest being the new parts headquarters, which houses 30,000 types of vehicle component to a total value of over Om.
There is no doubt that Britain and many thousands of its workers have benefited enormously from this remarkable achievement.
c6
The Power of Mould
IN the earlier days of bodybuilding when timber was used A to a much greater extent than it is now and not so much attention was paid to obviating inaccessible spaces, trouble was often caused by rotting and the growth of fungus. Fungi, or moulds, can be of many kinds—even penicillin comes into this category—and some grow in curious circumstances. When totally enclosed they can even develop considerable pressure.
Many years ago the late Oliver Lucas presented to certain of his friends rosebowls with polished, black hollow bases of plastics, into each of which was screwed a metal plate. In some way or other mould spores were included in some of the sealed chambers thus left, and in a few cases these multiplied and eventually burst the bases. Much surprise was expressed by the Lucas technicians when, on removing the base plates, the cause of the trouble was discovered.
Automation by Timken
VISIT to the new building project at Duston of British Timken, Ltd. is full of interest. It is about five years since this was started, with the object of producing taperedroller bearings within the size range of 1-} in. to 3 in. outside diameter and in quantities which would permit the development of the automatic line system of manufacture.
Obviously the simplest line giving cheapest production would be one restricted to a single bearing size, but each bearing consists of a cup and a cone, which mean two lines, this being the original number installed. After three years of constant development, however, the factory was rearranged to house two improved cup and two cone lines, as it was thought that there was sufficient promise of standardization of bearing sizes to warrant this.
Present production rate is about 3m. bearings annually and at any one time there are approximately 40,000 cups and cones in each set of lines; giving over 80,000 bearings a week. This is not the designed full output, for as new sizes of bearing attain sufficient production volume to make it economically worthwhile to tool, they will be added to the range of the lines until the rate of 5m. bearings per annum is achieved.
Already, new lightweight, high-capacity bearings in conjunction with these new production methods, have permitted the company, especially in the automobile field, to offer them at prices which it is hoped will stimulate standardization, and thus permit fewer changeovers of the production lines and even lower costs.
Automation has been extensively applied also to the machine shop, which produces machined components from tubes, the heat-treatment department, the grinding shop, and even to the sections covering assembly, greasing and packing. In fact, there is nothing static about the factory, instead a continual process of development and improvement, but lack of sufficient standardization restrains many interesting innovations.
Inspection throughout is on a statistical quality-control basis; patrolling inspectors check regularly at the machines, whilst production personnel make intermediate spot checks. At the completion of manufacture there is full inspection to high visual and dimensional standards.