Tipping with confidence
Page 112
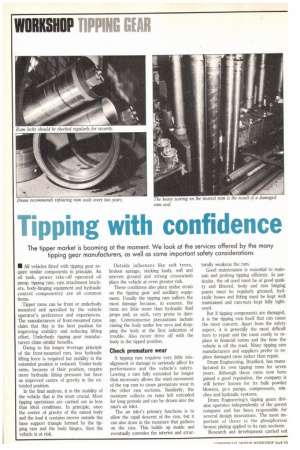
Page 113
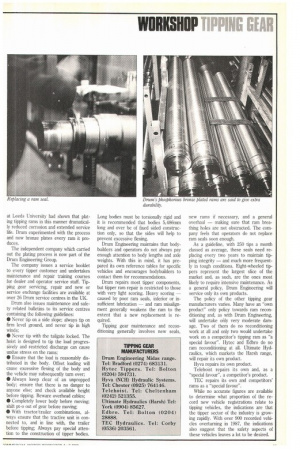
If you've noticed an error in this article please click here to report it so we can fix it.
The tipper market is booming at the moment. We look at the services offered by the many tipping gear manufacturers, as well as some important safety considerations
• All vehicles fitted with tipping gear require similar components in principle. An oil tank, power take-off operated oil pump, tipping ram, ram attachment brackets, body-hinging equipment and hydraulic control componentry are all common items.
,Tipper rams can be front or underbody mounted and specified by the vehicle operator's preference and experiences. The manufacturers of front-mounted rams claim that this is the best position for improving stability and reducing lifting effort. Underbody tipping gear manufacturers claim similar benefits.
Owing to the longer leverage principle of the front-mounted ram, less hydraulic lifting force is required but stability in the extended position is reduced. Under-body rams, because of their position, require more hydraulic lifting pressure but have an improved centre of gravity in the extended position.
In the final analysis, it is the stability of the vehicle that is the most crucial. Most tipping operations are carried out in less than ideal conditions. In principle, once the centre of gravity of the raised body and the load it contains moves outside the base support triangle formed by the tipping ram and the body hinges, then the vehicle is at risk. Outside influences like soft tyres, broken springs, sticking loads, soft and uneven ground and strong crosswinds place the vehicle at even greater risk.
These conditions also place undue strain on the tipping gear and ancillary equipment. Usually the tipping ram suffers the most damage because, in essence, the rams are little more than hydraulic fluid props and, as such, very prone to damage. Commonsense precautions include raising the body under low revs and dropping the body at the first indication of trouble. Also never drive off with the body in the tipped position.
Check premature wear
A tipping ram requires very little misalignment or damage to seriously affect its performance and the vehicle's safety. Leaving a ram fully extended for longer than necessary allows the wind movement of the top ram to cause premature wear in the other ram sections. Similarity, the moisture collects on rams left extended for long periods and can be drawn into the ram's air inlet.
The air inlet's primary functions is to allow the rapid descent of the ram, but it can also draw in the moisture that gathers on the ram. This builds up inside and eventually corrodes the interior and struc
turally weakens the ram.
Good maintenance is essential to maintain and prolong tipping efficieny. In particular, the oil used must be of good quality and filtered, body and ram hinging points must be regularly greased, hydraulic hoses and fitting must be kept well maintained and ram-nuts kept fully tightened.
But if tipping components are damaged, it is the tipping ram itself that can cause the most concern. Apart from the safety aspect, it is generally the most difficult item to repair and the most costly to replace in financial terms and the time the vehicle is off the road. Many tipping ram manufacturers and suppliers prefer to replace damaged rams rather than repair.
Drum Engineering, Bradford, has manufactured its own tipping rams for seven years. Although these rams now have gained a good reputation, the company is still better known for its bulk powder blowers, pt-o pumps, compressors, winches and hydraulic systems.
Drum Engineering's tipping gears division operates independently of the parent company and has been responsible for several design innovations. The most important of these is the phosphorous bronze plating applied to its ram sections.
Research and development carried out at Leeds University had shown that plating tipping rams in this manner dramatically reduced corrosion and extended service life. Drum experimented with the process and now bronze plates every ram it produces.
The independent company which carried out the plating process is now part of the Drum Engineering Group.
The company issues a service booklet to every tipper customer and undertakes maintenance and repair training courses for dealer and operator service staff. Tipping gear servicing, repair and new or service exchange facilities are available at over 26 Drum service centres in the UK.
Drum also issues maintenance and safety related bulletins to its service centres containing the following guidelines: • Never tip on a side slope; always tip on firm level ground, and never tip in high winds; • Never tip with the tailgate locked. The hoist is designed to tip the load progressively and restricted discharge can cause undue stress on the rams; • Ensure that the load is reasonably distributed in the body. Offset loading will cause excessive flexing of the body and the vehicle may subsequently turn over; • Always keep clear of an unpropped body; ensure that there is no danger to anyone else; and check available height before tipping. Beware overhead cables; • Completely lower body before moving; shift pt-o out of gear before moving; • With tractor/trailer combinations, always ensure that the tractive unit is connected to, and in line with, the trailer before tipping; Always pay special attention to the construction of tipper bodies. Long bodies must be torsionally rigid and it is recommended that bodies 6,486mm long and over be of fixed sided construction only, so that the sides will help to prevent excessive flexing.
Drum Engineering maintains that bodybuilders and operators do not always pay enough attention to body lengths and axle weights. With this in mind, it has prepared its own reference tables for specific vehicles and encourages bodybuilders to contact them for recommendations.
Drum repairs most tipper components, but tipper ram repair is restricted to those with very light scoring. Heavy scoring — caused by poor ram seals, inferior or insufficient lubrication — and ram misalignment generally weakens the ram to the extent that a new replacement is required.
Tipping gear maintenance and reconditioning generally involves new seals, new rams if necessary, and a general overhaul — making sure that ram breathing holes are not obstructed. The company feels that operators do not replace ram seals soon enough.
As a guideline, with 250 tips a month classed as average, these seals need replacing every two years to maintain tipping integrity — and much more frequently in tough conditions. Eight-wheeled tippers represent the largest slice of the market and, as such, are the ones most likely to require intensive maintenance. As a general policy, Drum Engineering will service only its own products.
The policy of the other tipping gear manufacturers varies. Many have an "own product" only policy towards ram reconditioning and, as _with Drum Engineering, will undertake only very moderate darnage. Two of them do no reconditioning work at all and only two would undertake work on a competitor's tipping ram as "a special favour". Hytec and Edbro do no ram reconditioning at all. Ultimate Hydraulics, which markets the Harsh range, will repair its own product.
Hyva repairs its own product.
Telehoist repairs its own and, as a "special favour", a competitor's product.
TEC repairs its own and competitors' rams as a "special favour".
While no accurate figures are available to determine what proportion of the record new vehicle registrations relate to tipping vehicles, the indications are that the tipper sector of the industry is growing rapidly. With over 900 recorded vehicles overturning in 1987, the indications also suggest that the safety aspects of these vehicles leaves a lot to be desired.