The scope for 'reefer' developments
Page 40
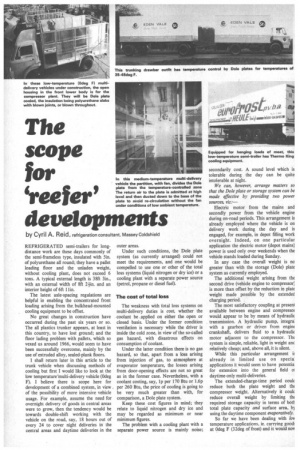
Page 41
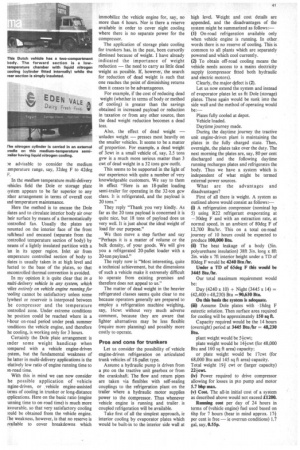
Page 42
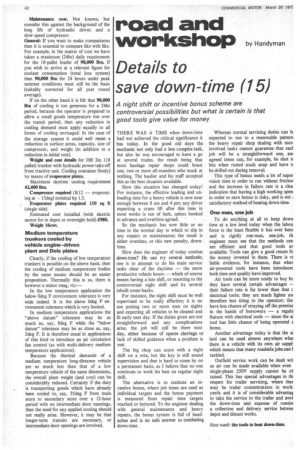
If you've noticed an error in this article please click here to report it so we can fix it.
by Cyril A. Reid, refrigeration consultant. Massey Coldshield
REFRIGERATED semi-trailers for longdistance work are these days commonly of the semi-frameless type, insulated with 5in. of polyurethane all round; they have a pallet loading floor and the unladen weight, without cooling plant, does not exceed 6 tons. A typical external length is 38ft 3in., with an external width of 8ft 24in. and an interior height of 6ft llin.
The latest axle-spacing regulations are helpful in enabling the concentrated front loading arising from the, bulkhead-mounted cooling equipment to be offset.
No great changes in construction have occurred during the past six years or so. The all plastics trunker appears, at least in this country, to have lost ground; and the floor lading problem with pallets, which so vexed us around 1966, would seem to have been successfully overcome, mainly by the use of extruded alloy, sealed-plank floors.
I shall return later in this article to the trunk vehicle when discussing methods of cooling but first I would like to look at the low temperaturemulti-delivery vehicle (Odeg F). I believe there is scope here for development of a combined system, in view , of the possibility of more intensive vehicle usage. For example, assume the need for overnight delivery of goods in central areas were to grow, then the tendency would be towards double-shift working with the vehicle on the road, say, 18 hours out of every 24 to cover night deliveries in the central areas and daytime deliveries in the outer areas.
Under such conditions, the Dole plate system (as currently arranged) could not meet the requirements, and one would be compelled to use one or other of the total loss systems (liquid nitrogen or dry ice) or a cooling plant with a separate power source (petrol, propane or diesel fuel).
The cost of total loss The weakness with total loss systems on multi-delivery duties is cost, whether the coolant be . applied on either the open or closed basis. Under the former condition ventilation is necessary while the driver is inside the cold zone, in view of the so-called gas hazard, with disastrous effects on consumption of coolant.
Under the latter condition there is no gas hazard, so that, apart from a loss arising from injection of gas, to atmosphere at evaporator temperature, the losses arising from door-opening effects are not so great as in the former case. Nevertheless, with a coolant costing, say, lp per 170 Btu or 1.6p per 260 Btu, the price of cooling is going to be very much greater than with, for comparison, a Dole plate system.
Keep these cost figures in mind; they relate to liquid nitrogen and dry ice and may be regarded as minimum or near minimum figures.
The problem with a cooling plant with a separate power source is mainly noise; secondarily cost. A sound level which is tolerable during the day can be quite intolerable at night.
We can, however, arrange matters so that the Dole plate or storage system can be made effective by providing two power sources, viz:—
Electric motor from the mains and secondly power from the vehicle engine during on-road periods. This arrangement is already employed where the vehicle is on delivery work during the day and is engaged, for example, in depot filling work overnight. Indeed, on one particular application the electric motor (depot mains) power is used only over weekends when the vehicle stands loaded during Sunday.
In any case the overall weight is no greater than with the storage (Dole) plate system as currently employed.
The additional weight arising from the second drive (vehicle engine to compressor) is more than offset by the reduction in plate weight made possible by the extended charging period.
The most satisfactory coupling at preseni available between engine and compressoi would appear to be by means of hydraulic transmission. A hydraulic pump, integral with a gearbox or driven from engine crankshaft, delivers fluid to a hydraulic motor adjacent to the compressor. The system is simple, reliable, light in weight and relatively cheap; and, above all, it is silent.
While this particular arrangement h already in limited use on specia applications it would seem to have potentia for extension into the general field col daytime-only multi-deliveries.
The extended-charge-time period couk reduce both the plate weight and the compressor weight. Alternatively it couk reduce overall weight by limiting the required storage capacity in terms of botl total plate capacity and surface area, 131 using the daytime component evaporatively.
So far we have been dealing with /oil temperature applications ie. carrying good! at Odeg F (32deg of frost) and it would no De advisable to consider the medium Temperature range, say, 32deg F to 42deg F.
In the medium temperature multi-delivery /chides field the Dole or storage plate ystern appears to be far superior to any )ther arrangement in terms of overall cost ind temperature maintenance.
Here the method is to encase the Dole )Iates and to circulate interior body air over heir surface by means of a thermostatically ;ontrolled fan. Usually the plates are nounted on the interior face of the front )ulkhead and encased (separate from the ;ontrolled temperature section of body) by neans of a lightly insulated partition with a in in its upper region. Inlet air from emperature controlled section of body to )Iates is usually taken in at high level and lucted to the base of the plates, so that incontrolled thermal convection is avoided.
In my opinion it is quite clear that in a flu/ti-delivery vehicle in any system, which .elies entirely on vehicle engine running for 7oofing cannot be satisfactory unless some lywheel or reservoir is interposed between he compressor and the temperature :ontrolled zone. Under extreme conditions he position could be reached where in a )-hour on-road period under peak summer :onditions the vehicle engine, and therefore he cooling, is working only for 3 hours.
Certainly the Dole plate arrangement is inder some weight handicap when ;ompared with a vehicle engine-driven iystem, but the fundamental weakness of he latter in multi-delivery applications is the .elatively low ratio of engine running time to m-road time.
With this in mind we can now consider he possible application of vehicle :ngine-driven, or vehicle engine-assisted 'orms of cooling in tnmker or long-distance ipplications. Here on the basic ratio (engine .unning time to on-road time) is much more avourable, so that very satisfactory cooling :ould be obtained from the vehicle engine. Ile weakness, however, is that no reserve is wailable to cover breakdowns which
immobilize the vehicle engine for, say, no more than 4 hours. Nor is there a reserve available in order to cover night cooling where there is no separate power for the compressor.
The application of storage plate cooling for trunkers has, in the past, been cursorily dimissed because of weight. I have already indicated the importance of weight reduction — the need to carry as little dead weight as possible. If, however, the search for reduction of dead weight is such that one reaches the point of diminishing returns then it ceases to be advantageous.
For example, if the cost of reducing dead weight (whether in terms of body or method of cooling) is greater than the savings obtained in increased payload or reduction in taxation or from any other source, then the dead weight reduction becomes a dead loss.
Also, the effect of dead weight — unladen weight — presses most heavily on the smaller vehicles. It seems to be a matter of proportion. For example, a dead weight of 3cwt in a small vehicle of, say, 2.5 tons gvw is a much more serious matter than 3 cwt of dead weight in a 32 tons gcw outfit.
This seems to be supported in the light of our experience with quite a number of very knowledgeable customers. We say to them in effect "Here is an 18-pallet loading semi-trailer for operating in the 32-ton gew class. It is refrigerated, and the payload is 20 tons."
They reply "Thank you very kindly. As far as the 20 tons payload is concerned it is quite nice, but 18 tons of payload does us very well. It is just about the ideal weight of load for our purpose."
We then move a step further and say "Perhaps it is a matter of volume or the bulk density, of your goods. We will give you a refrigerated 20-pallet loader with a 20-ton payload."
The reply now is "Most interesting, quite a technical achievement, but the dimensions of such a vehicle make it extremely difficult to operate from existing premises and therefore does not appeal to us."
The matter of dead weight in the heavier refrigerated classes seems quite clear to me because operators generally are prepared to employ a refrigeration machine weighing, say, 16cwt without very much adverse comment, because they are aware that lighter alternatives may be less flexible (require more planning) and possibly more costly to operate.
Pros and cons for trunkers Let us consider the possibility of vehicle engine-driven refrigeration on articulated trunk vehicles of I8-pallet type.
Assume a hydraulic pump is driven from a pto on the tractive unit gearbox or from the crankshaft: The flow and return pipes are taken via fleycibles with self-sealing couplings to the refrigeration plant on the trailer where a hydraulic motor supplies power to the compressor. Thus whenever vehicle engine is running and trailer, is coupled refrigeration will be available.
Take first of all the simplest approach, ie interior cooling by evaporator plates which would be built-in to the interior side wall at
high level. Weight and cost details are appended, and the disadvantages of the system might be summarized as follows:—
(1) On-road refrigeration available only when vehicle engine is running. In other words there is no reserve of cooling. This is common to all plants which are separately powered and which cool currently.
(2) To obtain off-road cooling means the vehicle needs access to a mains electricity supply (compressor fitted both hydraulic and electric motors).
Clearly, the major defect is (2). Let us now extend the system and instead of evaporator plates let us fit Dole (storage) plates. These again would be sunk into the side wall and the method of operating would be:—
Plates fully cooled at depot.
Vehicle loaded.
Daytime journey made.
During the daytime journey the tractive unit engine-driven plant is maintaining the plates in the fully charged state. Then, overnight, the plates take over the duty. The next morning the plates are, say, 80 per cent discharged and the following daytime running recharges plates and refrigerates the body. Thus we have a system which is independent of what might be termed external power sources.
What are the advantages and disadvantages?
First of all there is weight. A system as outlined above would consist as follows:— (I) A refrigeration compressor (nominal hp 5) using R22 refrigerant evaporating at —30deg F and with an extraction rate, at normal speed, in an ambient of 80deg F of 12,700 Btu/hr. This on a total on-road journey of 10 hours could be expected to produce 100,000 Btu.
(ii) The heat leakage of a body (5in. polyurethane insulation) 38ft 3in. long x 8ft 2in. wide x 7ft interior height under a TD of 80deg F would be 4240 Btu /hr.
Under a TD of 65deg F this would be 3445 Btu/hr.
Our total maximum requirement would be:
Day (4240 x 10) + Night (3445 x 14) = (42,400+48,230) Btu =90,630 Btu.
On this basis the system is adequate. ftift Assume Dole plates with -18deg F eutectic solution. Then surface area required for cooling will be approximately 150 sq ft.
Capacity required would be the 14 hours (overnight) period at 3445 Btu /hr = 48,230 Btu.
plant weight would be 51cwt; plate weight would be 14+cwt (for 48,000 Btu and 160 sq ft area) capacity;
or plate weight would be 17cw-t (for 68,000 Btu and 145 sq ft area) capacity. Total weight 19+ cwt or (larger capacity) 224-cwt.
(iv) Power required to drive compressor allowing for losses in pto pump and motor 5.7 blip max.
(v) Cost. The all-in initial cost of a system as described above would not exceed £1200.
Running cost per day of 24 hours in terms of (vehicle engine) fuel used based on 6hp for 7 hours (bear in mind approx. 17+ per cent is free — ie overrun conditions) 1.7 gal, say, 0.55p. Maintenance cost. Not known, but consider this against the background of the long life of hydraulic drives and a slow-speed compressor.
General: If you want to make comparisons then it is essential to compare like with like. For example, in the matter of cost we have taken a maximum (24hr) daily requirement for the 18-pallet loader of 90,000 Btu. If you wish to arrive at a relevant figure for coolant consumption (total loss system) then 90,000 Btu for 24 hours under peak summer conditions must still be the basis (suitably corrected for all year round average).
If on the other hand it is felt that 90,000 Btu of cooling is too generous for a 24hr period, because the operator is prepared to allow a small goods temperature rise over the transit period, then any reduction in cooling demand must apply equally to all forms of cooling envisaged. In the case of the storage system it could well mean a reduction in surface areas, capacity, size of compressor, and weight (in addition to a reduction in initial cost).
Weight and cost details for 38ft 2in. (18 pallet) trunker with hydraulic power-take-off from tractive unit. Cooling container (body) by means of evaporator plates.
Maximum daytime cooling requirement 42,400 Btu.
Compressor required (R12 — evaporating at — 15deg) nominal hp 1.5.
Evaporator plates required 150 sq ft (single side).
Estimated cost installed (with electric motor for in depot or overnight hold) f9/10. Weight 16ewt.
Medium temperature trunkers cooled by vehicle engine-driven plant and Dole plates
Clearly, if the cooling of low temperature trunkers is possible on the above basis, then the cooling of medium temperature bodies by the same means should be an easier proposition. Thermally this is so, there is however a minor snag, viz:—
In the low temperature application the below Odeg F environment tolerance is very wide indeed_ It is the above Odeg F environment tolerance which is very limited.
In medium temperature applications the "above datum" tolerance may be as much as, say, 8deg F while the "below datum" tolerance may be as close as, say, 3deg F. It is therefore usual in applications of this kind to introduce an air circulation fan control (as with multi-delivery medium temperature applications).
Because the thermal demands of a medium temperature long-distance vehicle are so much less than that of a low temperature vehicle of the same dimensions, the overall plant weight (and cost) can be considerably reduced. Certainly if the duty is transporting goods which have already been cooled to, say, 35deg F from main store to secondary store over a 12-hour period with no intermediate door openings, then the need for any applied cooling should not really arise. However, it may be that longer-term transits are necessary, or intermediate door openings are involved.