Materials for Producer-gas Apparatus
Page 34
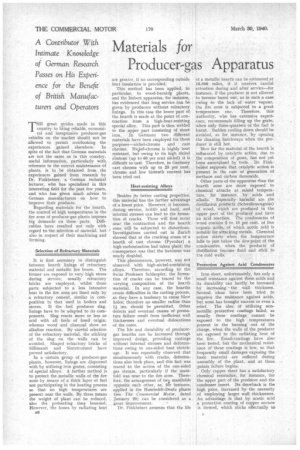
Page 35
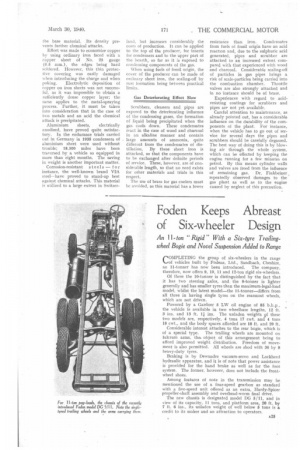
If you've noticed an error in this article please click here to report it so we can fix it.
A Contributor With Intimate Knowledge of German Research Passes on His Experience for the Benefit of British Manufacturers and Operators THEgreat strides made in this country to bring reliable, economical and inexpensive producer-gas vehicles on the market should not be allowed to permit overlooking the experiences gained elsewhere. In spite of the fact that German materials are not the same as in this country, useful information, particularly with reference to the correct maintenance of plants, is to be obtained from the experiences gained from research by Dr. Finkbeiner, a German technical lecturer, who has specialized in this interesting field for the past few years, and who has given much advice to German manufacturers on how to improve their products.
Regarding materials for the hearth, the control of high temperatures in the fire zone of producer-gas plants imposes big demands on these parts. Difficulties have resulted not only with regard to the selection of material, but also in respect of their machining and forming.
Selection of Refractory Materials It is first necessary to distinguish between hearth linings of refractory material. and metallic fire boxes. The former are exposed to very high stress during service; usually refractory bricks are employed, whilst those parts subjected to a less intensive heat in the fire zone are lined only by a refractory cement, similar in composition to that used in boilers and stoves. If the fuel produces slag, linings have to be adapted to its components. Slag reacts more or less as acid with all fuels of fossil origin, whereas wood and charcoal show an alkaline reaction. By careful selection of the refractory material, the sticking of the slag on the walls can be avoided. Shaped refractory bricks of Sillimanit and Sintercorund have proved satisfactory.
In a certain group of producer-gas plants, however, linings are dispensed with by utilizing iron grates, consisting of special alloys. A further method is to protect the metallic walls of tire fire zone by means of a thick layer of fuel not participating in the heating process so that no high temperatures are present near the walls. By these means the weight of plant can be reduced, also the preheating time lessened. However, the losses by radiating heat aS are greater, if no corresponding outside heat insulation is provided.
This method has been applied, in particular, to wood-bumint plants, and the Imbert apparatus, for instance, has evidenced that long service can be given by producers without refractory linings. In this case the lower part of the hearth is made at the point of contraction from a high-heat-resisting special alloy. This part is then welded to the upper part consisting of sheet iron. In Germany two different materials have been employed for these purposes—nickel-chrome and cast chrome. Nickel-chrome is highly heat resistant, but owing to its high nickel Content (up to 60 per cent nickel) it is difficult to cast. Therefore, in Germany cast chrome with up to 25 per cent. chrome and low bismuth content has been tried out.
Heat-resisting Alloys Besides its better casting properties, this material has the further advantage of a lower price. However, it becomes, during service, brittle and hard, and internal stresses can lead to the formation of cracks. These will first occur near the contraction and the hearth zone will be subjected to distortions. Investigations carried out in Zurich showed that at the cracking zones of a hearth of cast chrome (Pyrodur) a high carbonization had taken place; the consequence was that the hardness was nearly doubled.
This phenomenon, however, was not observed with high-nickel-containing alloys. Therefore, according to the Swiss Professor Schlaepfer, the formation of cracks can be traced to the varying composition of the hearth material. In any case, the hearths create difficulties in the casting process, as they have a tendency to cause blow holes; therefore no smaller radius than ins, should be permitted. Other defects and eventual causes of premature failure result from inefficient wall thicknesses and eventual dislocations of the cores.
The life and durability of producergas hearths can be increased through improved design, providing castings without internal stresses and deformations owing to one-sided heat shrinkage. It was repeatedly observed that simultaneously with cracks, deformations also took place, and this fact was traced to the action of the one-sided gas stream, particularly if the manifold was near to the fire zone. Therefore, the arrangement of twii) manifolds opposite each other, as, for instance, applied in the Humboldt-Deutz plants (see The Commercial Motor, dated January 20) can be considered as a great improvement.
Dr. Finkbeiner assumes that the life
of a metallic hearth can be estimated at 18.000 miles, if it receives careful attention during and after service—for instance, if the producer is not allowed to become burnt out, as in such a case owing to the lack of water vapour, the fire zone is subjected to a great temperature rise. Therefore, this authority, who has extensive experience, recommends filling up the grate, when only three-quarters of the fuel is burnt. Sudden cooling down should be avoided, as for instance, by opening the cleaning hatchways when the producer is still hot.
How far the material of the hearth is influenced by catalytic action, due to the composition of gases, has not yet been ascertained by tests. Dr. Finkbeiner supposes that catalytic action is present in the case of generation of methane and carbon rhonoxide.
Other parts of the apparatus than the hearth zone are more exposed to chemical attacks at raised temperature, for instance, by acids and alkalis. Especially harmful are the distillation products (Schwelerzeugniss) of wood, which are produced in the upper part of the producer and have an acid reaction. The condensates of Wood contain 2 to 10 per cent, of free organic acids, of which acetic acid is notable for attacking metals. Chemical action starts when the temperature falls to just below the dew point of the condensates, when the products of distillation become fluid and stick to the cold walls.
Protection Against Acid Condensates Iron sheet, unfortunately, has only a small resistance against these acids and its durability can hardly be increased by increasing the wall thickness. Several ideas have been tried to improve the resistance against acids, but none has brought success or even a relief. The idea of utilizing nonmetallic protective coatings failed, as usually these coatings cannot be exposed to the high temperatures present in the burning out of the charge, when the walls of the producer are exposed to the radiating heat of the fire. Email-coatings have also been tested, but the mechanical resistance of these coatings is low, so that frequently small damages exposing the basic material are suffered during assembly of the plant, and at these points failure begins.
Only copper sheet has a satisfactory chemical resistafice, for instance, for the upper part of the producer and the condenser insert. Its drawback is the high price, increased by the necessity of employing larger wall thicknesses. An advantage is that by acetic acid a protective coating of capper acetate is formed, which sticks effectually to the base material. Its density prevents further chemical attacks.
Effort was made to economize copper by using ordinary iron faced with a copper sheet of No. 25 gauge (0,5 ram.), the edges being hard soldered. However, this thin protective covering was easily damaged when introducing the charge and when poking. Electrolytic deposition of copper on iron sheets was not successful, as it was impossible to obtain a sufficiently dense copper layer; the same applies to the metal-spraying process. Further, it must be taken into consideration that in the case of two metals and an acid the chemical attack is precipitated.
Aluminium sheets, electrically anodized, have proved quite satisfactory. In the endurance trials carried out in Germany in 1935 condensers of aluminium sheet were used without trouble; 18,500 miles have been traversed by a vehicle so equipped in more than eight months. The saving in weight is another important matter.
Corrosion-resistant s te els — f o r instance, the well-known brand V2A steel—have proved to stand-up best against chemical attacks. This material is utilized to a large extent in Switzer
land, but increases considerably the costs of production. It can be applied to the top of the producer, for inserts for condensers and to the upper part of the hearth, so far as it is exposed to condensing components of the gas.
When using fuels of fossil origin, the cover of the producer can be made of ordinary sheet iron, the scaling-off by rust formation being between practical limits, Gas Deteriorating Effect Slow Scrubbers, cleaners and pipes are exposed to the deteriorating influence of the condensing gases, the formation of liquid being precipitated when the gas cools down. These condensates react in the case of wood and charcoal in an alkaline manner and contain large amounts of ammonia, quite different from the condensates of distillation. By these sheet iron is attacked, so that the components have to be exchanged after definite periods of service_ These, however, are of considerable length, so that no need exists for other materials and trials in this respect.
The use of brass for gas coolers must be avoided, as this material has a lower resistance than iron. Condensates from fuels of fossil origin have an acid reaction and, due to the sulphuric acid generated, pipes and scrubber are attacked to an increased extent compared with that experienced with wood and charcoal. Considerable scaling-off of particles in gas pipes brings a risk of scale-particles being carried into the combustion chamber. Throttle valves are also strongly attacked and in no instance should be of brass.
Experiences with regard to acidresisting coatings for scrubbers and pipes are not yet available.
Careful attention to maintenance, as already pointed out, has a considerable influence on the durability of the components of the plant. For instance, when the vehicle has to go out of service for several days the pipes and scrubbers should be carefully degassed. The best way of doing this is by blowing air through the whole system, which can he effected by keeping the engine running for a few minutes on petrol. By this means cylinder walls and valves are freed from the influence of remaining gas. Dr. Finkbeiner, repeatedly observed damages to the gas plant as well as to the engine caused by neglect of this precaution.