EN AMELLING -IASSIS FRAMES
Page 50
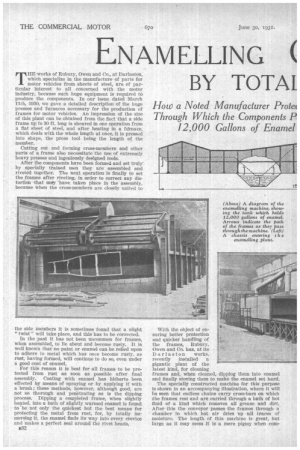
Page 51
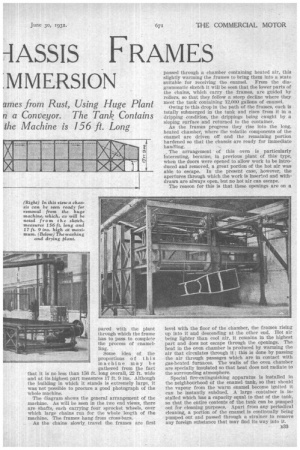
If you've noticed an error in this article please click here to report it so we can fix it.
BY TOTAI MMERSION
THE works of Rubury, Owen and Co., at Darlaston, which specialize hi the manufacture of parts for motor vehicles from sheets of steel, are of particular interest to all concerned with the motor industry, because such huge equipment is required to produce the components. In our issue dated March 11th, 1930, we gave a detailed description of the huge presses and furnaces necessary for the production of frames for motor vehicles. An impression of the size of this plant can be obtained from the fact that a side frame up to 30 ft. long is sheared in one operation from a fiat sheet of steel, and after heating in a fUrnace, which deals with the whole length at once, it is pressed into shape, the press tool being the length of the member.
Cutting out and forming cross-members and other parts of a frame also necessitate the use of extremely heavy presses and ingeniously designed tools.
After the components have been formed and set truly by specially trained men they are assembled and riveted together. The next operation is finally to set the frames after riveting, in order to correct any distortion that nury have taken place in the assembly, because when the cross-members are closely united to the side members it is sometimes found that a slight " twist " will take place, and this has to be corrected.
In the past it has not been uncommon for frames, when assembled, to lie about and become rusty. It is well known that no paint or enamel can be relied upon to adhere to metal which has once become rusty, as rust, having formed, will continue to do so, even under a good coat of enamel.
For this reason it is best for all frames to be protected from rust as soon as possible after final assembly. Coating with enamel has hitherto been effected by means of spraying or by applying if with a brush ; these methods, however, although good, are not so thorough and penetrating as is the dipping process. Dipping a completed frame, when slightly heated, into a bath of slightly warmed enamel is found to The not only the quickest but the best means for protecting the metal from rust, for, by totally immersing it, the enamel finds its way into every crevice and makes a perfect seal around the rivet heads, .632 With the object of ensuring better protection and quicker handling of the frames, Rubury, Owen and Co. has, at its Darlaston works, recently installed a gigantic plant of the latest kind, for cleaning frames and, when cleaned, dipping them into enamel and finally stoving them to make the enamel set hard.
The specially constructed machine for this purpose is shown in an accompanying illustration, where it will be seen that endless chains carry cross-bars on which the frames rest and are carried through a bath of hot fluid of a kind which removes all grease and dirt. After this the conveyor passes the frames through a chamber in which hot air dries up !all traces of moisture. The length of this machine is great, but large as it may seem It is a mere pigmy when corn
pared with the plant through which the frame has to pass to complete the process of enamelling.
Some idea of the proportions of this machine may be gathered from the fact that it is no less than 156 ft. long overall, 22 ft. wide and at its highest part measures 17 ft. 9 ins. Although the building in which it stands is extremely large, it was not possible to procure a good photograph of the whole machine.
The diagram shows the general arrangement of the machine. As will be seen in the two end views, there are shafts, each carrying four sprocket wheels, over which large chains run for the whole length of the machine. The frames hang from cross-bars.
As the chains slowly travel the frames are first passed through a chamber containing heated air, this slightly warming the frames to bring them into a state suitable for receiving the enamel. From the diagrammatic sketch it will be seen that the lower parts of the chains, which carry the frames, are guided by rollers, so that they follow a steep decline where they meet the tank containing 12,000 gallons of enamel.
Owing to this drop in the path of the frames, each is totally submerged in the tank and rises from it in a dripping condition, the drippings being caught by a sloping surface and returned to the container.
As the frames progress they rise into the long, heated chamber, where the volatile components of the enamel are driven off and the remaining portion hardened so that the chassis are ready for immediate handlin_z.
The arrangement of this oven is particularly Interesting, because, in previous plant of this type, when the doors were opened to allow work to be introduced and removed, a great portion of the hot air was able to escape. In the present case, however, the apertures through which the work is inserted and withdrawn are always open, but no hot air can escape.
The reason for this is that these openings are on a level with the floor of the chamber, the frames rising up into it and descending at the other end. Hot air being lighter than cool air, it remains in the highest part and does not escape through the openings. The heat in the oven chamber is produced by warming the air that circulates through it ; this is done by passing the air through passages which are in contact with gas-heated furnaces. The walls of the oven chamber are specially insulated so that heat does not radiate to the surrounding atmosphere.
Special fire-extinguishing apparatus is installed in the neighbourhood of the enamel tank, so that should the vapour from the warm enamel become ignited it can be instantly subdued. A large container is installed which has a capacity equal to that of the tank, so that the entire contents of the tank can be pumped out for cleaning purposes. Apart from any periodical cleaning, a portion of the enamel is continually 'being pumped out and passed through a strainer to remove any foreign substance that may find its way into it.