Pointers on
Page 50

Page 51
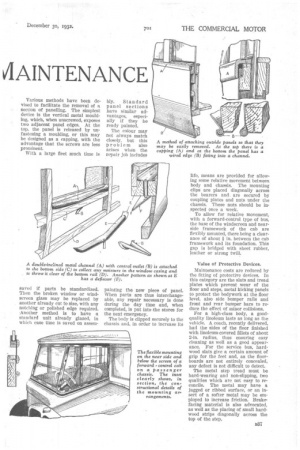
If you've noticed an error in this article please click here to report it so we can fix it.
BODY dAINTENANCE
IN every well-ordered garage, each vehicle, at the end of its day's work, is subjected to a routine inspection, attention being given first to any defect which has been reported by the driver. It may not be possible to examine the bus thoroughly each day, but, by allocating certain parts for attention at regular intervals, the whole vehicle is dealt with systematically, with the result that few defects arise from neglect.
If the body be well made, only minor adjustments should be necessary and, with good-quality material and equipment, it should be possible to defer repairs, necessary owing to wear, until the annual overhaul.
Minimizing Maintenance Costs.
Good construction, therefore, minimizes maintenance costs. The body must be strong and waterproof. Protection from the weather includes not only well-fitted panels and windows, but also the provision of safeguards to prevent moisture from injuring the interior surface of the panels, the underside of the floor and hidden parts of the framework.
With a drop window, moisture sometimes finds its way into the casing between the inner and outer panels. Moisture is also caused in this part of the body by condensation. Moreover, air is sucked up from underneath while the vehicle is moving.
It is usual to drill the bottom side, in order that any water present may escape. To ensure this, there is a lengthwise groove along the top of the bottom side, which collects the water and leads it to the holes provided. Such a groove may be metal lined and have a decided incline, so that once any moisture has collected it does not remain stationary.
This method is satisfactory when there is no side framework below the botfom side. Nowadays, there is usually another rail which carries the bottom edge of the panel. The water should not drip on to this, but B36 be deflected from it, unless there be a down pipe which conducts the water from the bottom side directly to the ground.
The underside of the floor is exposed to the weather. To make it waterproof, it should be well painted on the underside and edges, whilst similar treatment should be given to the supporting framework. Under any maintenance scheme, it is impossible to inspect hidden parts of the body framework and panelling.
The bodybuilder usually makes each joint waterproof by driving it with white lead, but similar means for protection are not always applied to the framework, either before or during assembly, by giving it one or two coats of lead colour.
Repairs and Replacements.
To ensure low maintenance costs, any part which is liable to accidental damage should be designed so that it may quickly be repaired or replaced. Both full-drop and halfdrop windows are designed with this object in view, the metal window frame, or channel, being accessible after a wooden fillet has been removed. The holes in these fillets are reinforced with metal cups, which allow the raised-head screws to be taken out and replaced without injury to the woodwork. Various methods have beeh devised to facilitate the removal of a section of panelling. The simplest device is the vertical metal moulding, which, when unscrewed, exposes two adjacent panel edges. At the top, the panel is released by unfastening a moulding, or this may be designed as a capping, with the advantage that the screws are less prominent.
With a large fleet much time is saved if parts be standardized. Then the broken window or windscreen glass may be replaced by another already cut to size, with any notching or polished edge required. Another method is to have a standard unit already glazed, in which case time is saved on assem painting the new piece of panel. When parts are thus interchangeable, any repair necessary is done during the day time and, when completed, is put into the stores for the next emergency.
The body is clipped securely to the chassis and, in order to increase its life, means are provided for allowing some relative movement between body and chassis. The mounting clips are placed diagonally across the bearers and. are secured by coupling plates and nuts under the chassis. These nuts should be inspected once a week.
To allow for relative movement, with a forward-control type of bus, the base of the windscreen and nearside framework of the cab are flexibly mounted, there being a clearance of about I in. between the cab framework and its foundation. This gap is 'bridged with sheet rubber, leather or strong twill.
Value of Protective Devices.
Maintenance costs are reduced by the fitting of protective devices. In this category are the slats and tread plates which prevent wear of the floor and steps, metal kicking panels to protect the bodywork at the floor level, also side bumper rails and front and rear bumper bars to reduce the effect of minor collisions.
For a high-class body, a goodquality linoleum lasts as long as the vehicle. A coach, recently delivered, had the sides of the floor finished with linoleum-covered fillets of about 2-in, radius, thus ensuring easy cleaning as well as a good appearance. For the service bus, hardwood slats give a certain amount of grip for the feet and, as the floorboards are not entirely concealed, any defect is not difficult to detect.
The metal step tread must be hard-wearing and non-slipping, two qualities which are not easy to reconcile. The metal may have a jagged or ribbed surface, or an insert of a softer metal may be employed to increase friction. Brakefacing material is also advocated, as well as the placing of small hardwood strips diagonally across the top of the step.