MOTORWAY ;AFETY ON 10 WHEELS
Page 54
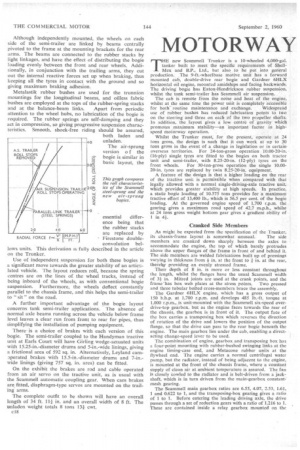
Page 55
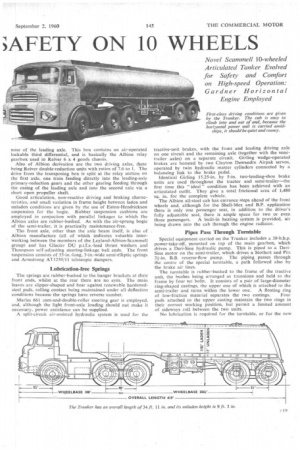
Page 56
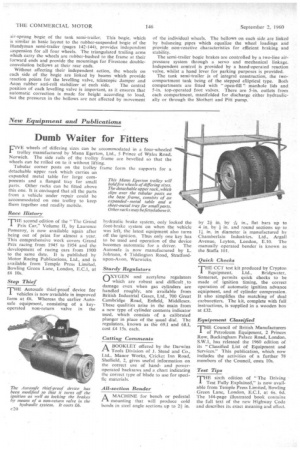
If you've noticed an error in this article please click here to report it so we can fix it.
THE new Scamrnell Trunker is a 10-wheeled 4,000-gal. tanker built to meet the specific requirements of ShellMex and B.P., Ltd., but also to be put into general production. The 9-ft.-wheelbase motive unit has a forward mounted cab, double-drive rear bogie and Gardner 60.LX horizontal oil engine, mounted amidships and facing backwards. The driving bogie has Eaton-Hendrickson rubber suspension, whilst the tank semi-trailer has Seammell air suspension..
The cab is remote from the noise and heat of the engine, whilst at the same time the power unit is completely accessible for bothroutine maintenance and exchange. Widespread use of rubber bushes has reduced lubrication points to two on the steering' and three on each of the two propeller shafts. In addition, the layout gives a low centre of gravity which promotes maximum stability—an 'important factor in high
speed motorway. operation. .
Whilst the Trunker must, for the present, operate at 24 tons gross, the design is such that it can work at up to 30 tons gross in the event of a change in legislation or in certain overseas territories. For 24-ton-gross operation 10.00-20-in. (16-ply) single tyres are fitted to the bogies on both tractor unit and semi-trailer, with 8.25-20-in. (12-ply) tyres on the
front wheels. For 30-ton-gross operation the single 10.0020-in. tyres are replaced by twin 8.25-20-in. equipment.
A feature of the design is that a higher loading on the rear of the tractive unit is permissible when compared with that legally allowed with a normal single-driving-axle tractive unit, which provides greater stability at high speeds. In practice, a static bogie loading of 10.575 tons provides for a maximum tractive effort of 13,400 lb., which is 56.5 per cent, of the bogie loading. At the governed engine speed of 1,700 r.p.m. the gearing gives a maximum road speed of 42.7 mp.h., whilstat 24 tons gross weight bottom gear gives a; gradient ability of I in 41.
Cranked Side Members As might be expected from the specification of the Trunker,
its chassis-frame layout is somewhat unusual. The side members are cranked down sharply, between the axles toaccommodate the engine, the top of which barely protrudes above the upper flanges of the frame in front of and behind it. The side members are welded fabrications built up of pressings varying in thickness from f in, at the front to f in. at the rear, thereby providing an evenly stressed frame.
Their depth of 8 in. is more or less constant throughout the length, whilst the flanges have the usual Scammell width of 3f in. Mitred joints are used at the crank points, and the frarne'has box web plates at the stress points. Two pressed and three tubular bolted cross-members brace the assembly.
The Gardner 6HLX engine, which has a gross output of 150 b.h.p. at 1,700 r.p.m. and develops 485 lb.-ft, torque at 1,000 r.p.m., is unit-mounted with the Scammell six-speed overdrive-top gearbox, but as the engine faces towards the rear of the chassis, the gearbox is in front of it. The output face of the box carries a transposing box which reverses the direction of rotation of the drive and lowers the position of the output flange, so that the drive can pass to the rear bogie beneath the engine. The main gearbox lies under the cab, enabling a directacting change-speed lever to be used.
The combination of engine, gearbox and transposing box has a four-point mounting with rubber-bushed swinging links at the engine timing-case end, and Metacone rubber units at the flywheel end. The engine carries a normal centrifugal water pump, but the radiator, instead of being adjacent to the engine, is mounted at the front of the chassis frame, where a constant supply of clean air at ambient temperature is assured. The fan is closely cowled to the radiator and is belt-driven from a jackshaft, which is in turn driven from the main-gearbox constant: mesh gearing.
The Scammell main gearbox ratios are 6.55, 4.07, 2.53, 1.61, 1 and 0.622 to 1, and the transposing-box gearing gives a ratio of 1 to I. Before entering the leading driving axle, the drive passes through a set of reduction gears with a ratio of 1.216 to 1. These are contained inside a relay gearbox mounted on the
nose of the leading axle. This box contains an air-operated lockable third differential, and is basically the Albion relay gearbox used in Reiver 6 x 4 goods chassis.
Also of Albion derivation are the two driving axles, these being Reiver double-reduction units with ratios of 7.6 to I. The drive from the transposing box is split at the relay section on the first axle, one train feeding directly into the leading-axle primary-reduction gears and the other gearing feeding through the casing of the leading axle and into the second axle via a short open propeller shaft.
Good articulation, non-reactive driving and braking characteristics, and small variation in frame height between laden and unladen conditions are given by the use of Eaton-Hendrickson suspension for the bogie. Rubber suspension cushions are employed in conjuction with parallel linkages to which the Albion axles are rubber-bushed. As with the air-sprung bogie of the semi-trailer, it is practically maintenance-free.
The front axle, other than the axle beam itself, is also of Albion manufacture (all of which indicates valuable interworking between the members of the Leyland-Albion-Scammell group) and has Glacier DU p.t.f.e.-lead thrust washers and Thompson self-adjusting steering-linkage ball ends. The front suspension consists of 55-in.-long, 3-in.-wide semi-elliptic springs and Armstrong AT1250/11 telescopic dampers.
Lubrication-free Springs
The springs are rubber-bushed to the hanger brackets at their front ends, whilst at the rear there are no eyes. The main leaves are slipper-shaped and bear against renewable hardenedsteel pads, rolling contact being maintained under all deflection conditions because the springs have reverse camber.
Mules 661 cam-and-double-roller steering gear is employed. and, although the light front-axle loading should not make it necessary, power assistance can be supplied.
A split-circuit air-assisted hydraulic system is used for the tractive-unit brakes, with the front and leading driving axle on one circuit and the remaining axle (together with the semitrailer axles) on a separate circuit. Girling wedge-operated brakes are boosted by two Clayton Dewandre Airpak servos, operated by twin hydraulic master cylinders connected by a balancing link to the brake pedal. Identical Girling 15.25-in. by 5-in, two-leading-shoe brake units are used throughout the tractor and semi-trailer—the first time this " ideal " condition has been achieved with an articulated outfit. They give a total frictional area of 1,480 sq. in. for the complete vehicle. The Albion all-steel cab has entrance steps ahead of the front wheels and, although for the Shell-Mex and BY. application there is only one passenger seat, in addition to the driver's fully adjustable seat, there is ample space for two or even three passengers. A built-in heating system is provided, air being drawn into the cab through the engine radiator.
Pipes Pass Through Turntable
Special equipment carried on the Trunker includes a 30-13.h.p. power-take-off, mounted on top of the main gearbox, which drives a Den-Sine hydraulic pump. This is piped to a DenSine motor on the semi-trailer, which drives a Stothert and Pitt 34-in. B.B. reverse-flow pump. The piping passes through the centre of the special turntable, a path followed also by the brake air lines.
The turntable is rubber-bushed to the frame of the tractive unit, the bushes being arranged as trunnions and held to the frame by four set bolts. It consists of a pair of large-diameter ring-shaped castings, the upper one of which is attached to the semi-trailer and turns within the lower one. A floating ring of low-friction material separates the two castings. Four pads attached to the upper casting maintain the two rings in their correct working position, but permit a limited amount of sideways roll between the two units.
No lubrication is required for the turntable, or for the new air-sprung bogie of the tank semi-trailer. This bogie, which is similar in basic layout to the rubber-suspended bogie of the Handyman semi-trailer (pages 142-144), provides independent 3uspension for all four wheels. The triangulated trailing arms which carry the wheels are rubber-bushed to the frame at their forward ends and provide the mountings for Firestone doubleconvolution bellows at their rear ends.
Without affecting their independent action, the wheels on each side of the bogie are linked by beams which provide reaction points for the levelling valve, telescopic damper and Aeon rubber anti-roll stabilizer at each side. The central position of each levelling valve is important, as it ensures that automatic correction is made for height according to load, but the pressures in the bellows are not affected by movement of the individual wheels. The bellows on each side are linked by balancing pipes which equalize the wheel loadings and provide non-reactive characteristics for efficient braking and stability. The semi-trailer bogie brakes are controlled by a two-line aii-pressure system through a servo and mechanical linkage. Independent control is provided by a hand-operated reaction valve, whilst a hand lever for parking purposes is provided.
The tank semi-trailer is of integral construction, the twocompartment tank being of the stepped elliptical type. Both compartments are fitted with " open-fill " manhole lids and 5-in, top-operated foot valves. There are 5-in, outlets from each compartment, manifolded for discharge either hydraulically or through the Stothert and Pitt pump.