GOING WITH THE FLOW
Page 52
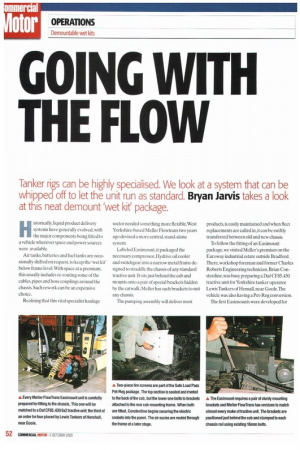
Page 53
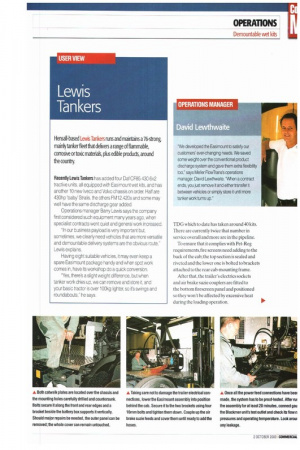
Page 54
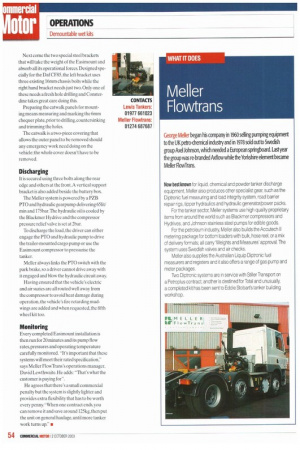
If you've noticed an error in this article please click here to report it so we can fix it.
Tanker rigs can be highly specialised. We look at a system that can be whipped off to let the unit run as standard. Bryan Jarvis takes a look at this neat demount 'wet kit' package.
Historically, liquid product delivery systems have generally evolved, with the major components being fitted to a vehicle wherever space and power sources were available.
Air tanks, batteries and fuel tanks are occasionally shifted on request. to keep the 'wet kit' below frame le vel. With space at a premium, this usually includes re-routing some of the cables, pipes and hose couplings around the chassis. Such rework can be an expensive choice.
Realising that this vital specialist haulage sector needed somethingmore llexible,West Yorkshire-based Metier Flowtrans two years ago devised a more central,stand-alone system.
Labeled Easimount, it packaged the necessary compressor. Hydrive oil cooler and sr,vitchgear into a narrow metal frame designed to straddle the chassis of any standard tractive unit. It sits just behind the cab and mounts onto a pair of special brackets hidden by the catwalk: Meller has such brackets to suit any chassis.
The pumping assembly will deliver most products, is easily maintained and when fleet replacements are called in, it can be swiftly transferred between old and new chassis.
To follow the fitting of an Easimount package, we visited Meller's premises on the Euroway industrial estate outside Bradford. There, workshop foreman and former Charles Roberts Engineering technician,Brian Consterdine, was busy preparing a Daf CF85A30 tractive unit for Yorkshire tanker operator Lewis Tankers of Hensall, near Goole.The vehicle was also having a Pet-Reg conversion.
The first Easirnounts were developed for TDG which to date has taken around 40 kits. There are currently twice that number in service overall and more are in the pipeline.
To ensure that it complies with Pet-Reg requirements, fire screens need adding to the back of the cab; the top section is sealed and riveted and the lower one is bolted to brackets attached to the rear cab-mounting frame.
After that, the trailer's electrics sockets and air brake suzie couplers are fitted to the bottom firescreen panel and positioned so they won't be affected by excessive heat during the loading operation. Next come the two special steel brackets that will take the weight of the Easimount and absorb all its operational forces. Designed specially for the Daf CF85, the left bracket uses three existing 16mm chassis bolts while the right hand bracket needs just two. Only one of these needs a fresh hole drilling and Consterdine takes great care doing this.
Preparing the catwalk panels for mounting means measuring and marking the 6mm chequer plate, prior to drilling, countersinking and trimming the holes.
The catwalk is a two-piece covering that allows the outer panel to be removed should any emergency work need doing on the vehicle:the whole cover doesn't have to be removed.
Discharging
It is secured using three bolts along the rear edge and others at the front.A vertical support bracket is also added beside the battery box.
The Meller system is powered by a PZB 1FT0 and hydraulic gearpump delivering 65Iit/ min and 175bar.The hydraulic oil is cooled by the Blackmer Hydrive and the compressor pressure relief valve is set at 2bar.
To discharge the load, the driver can either engage the PTO and hydraulic pump to drive the trailer-mounted cargo pump or use the Easimount compressor to pressurise the tanker.
Meller always links the PTO switch with the park brake, so a driver cannot drive away with it engaged and blow the hydraulic circuit away.
Having ensured that the vehicle's electric and air suzies are all routed well away from the compressor to avoid heat damage during operation, the vehicle's fire retarding mudwings are added and when requested, the fifth wheel kit too.
Monitoring
Every completed Easimount installation is then run for 20 minutes and its pump flow rates, pressures and operating temperature carefully monitored. "It's important that these systems will meet their rated specification." says Meller FlowTrans's operations manager. David Lewthwaite.He adds: "That's what the customer is paying for".
He agrees that there's a small commercial penalty but the system is slightly lighter and provides extra flexibility that has to be worth every penny. "When one contract ends, you can remove it and save around 1254. then put the unit on general haulage. until more tanker work turns up."