Spraying Molten Metal to Build Up Parts
Page 35
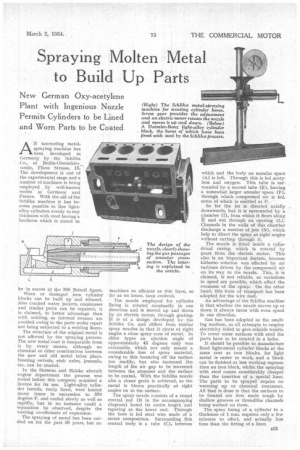
If you've noticed an error in this article please click here to report it so we can fix it.
New German Oxy-acetylene Plant with Ingenious Nozzle Permits Cylinders to be Lined and Worn Parts to be Coated
AN interesting metalspraying machine has been developed in Germany by the Schliha Co., of Berlin-Oberschanweide, Fliess Strasse, 15. The development is out of the experimental stage and a number of machines is being employed by well-known works in Germany and France. With the aid of the Schliha machine it has become possible to line lightalloy cylinders evenly to any thickness with steel having a hat dness which is stated to
be in excess of the 300 Brinell figure.
Worn or damaged iron cylinder blocks can be built up. and rebored. Also cracked water jackets, crankcases and similar parts can be repaired, it is claimed, to better advantage than with welding, as internal stresses are avoided owing to the parts under repair not being subjected to a welding flame.
The structure of the original metal is not affected by the spraying process. The new metal coat is inseparable from it by every means, although no chemical or other combination between the new and old metal takes place. Steering swivels, stub axles, journals, etc. can be treated.
In the Siemens and Halske aircraft engine department the process was tested before this company acquired a licence for its use. Light-alloy cylinder barrels, ready lined, were heated many times in succession to 570 degrees F. and cooled slowly as well as rapidly, but in no instance could a separation be observed, despite the varying co-efficients of expansion.
The spraying of metal has been carried on for the past 80 years, but no machines so efficient as this have, so far as we know, been evolved.
The nozzle employed for cylinder lining is rotated constantly in one direction and is moved up and down by an electric motor, through gearing. It is of a design developed by the Schliha Co. and differs from 'similar spray nozzles in that it ejects at right angles a close spray cone of metal. In older types an ejection angle of approximately 45 degrees only was attainable, which not only meant a considerable loss of spray material, owing to this bouncing off the surface too readily, but also increased the length of the air gap to be traversed between the atomiser and the surface to be coated. With the Schliha nozzle also a closer grain is achieved, as the metal is blown practically at right angles on to the surface.
The spray nozzle consists of a round central rod (B in the accompanying diagram) bored its entire length and tapering at the lower end. Through the bore is fed steel wire made of *a secret composition. Surrounding this central body is a tube (C), between which and the body an annular space (A) is left. Through this is fed acetylene and oxygen. This tube is surrounded by a second tube (E), leaving a somewhat larger annular space (F),, through which compressed air is fed, some of which is emitted at P.
So far the jet is directed axially downwards, but it is surrounded by a chamber (I), from which it flows along K and out through an opening (L). Channels in the walls of this chamber discharge a number of jets (N), which help to direct the spray at right angles without cutting through it.
The nozzle is fitted inside a cylindrical casing, which is rotated by gears from the electric motor. This also is an important feature, because hitherto, rotation was effected by air turbines driven by the compressed air on its way to the nozzle. This, it is claimed, is not reliable, as variations in speed are possible, which affect the evenness of the spray. On the other hand, this form of transport has been adopted for the wire feed.
An advantage of the Schliha machine is that whether the nozzle moves up or down it always turns with even speed in one direction.
Gas has been adopted as the smelting medium, as all attempts to employ electricity failed to give reliable results. To cover outer surfaces with steel the parts have to be rotated in a lathe.
It should be possible to manufacture lined light-metal cylinder blocks at the same cost as iron blocks, for light metal is easier to work, and a block can be finished at less working expense than an iron block, whilst the spraying with steel comes considerably cheaper than the insertion of a special liner. The parts to be sprayed require no warming up or chemical treatment. All that is done is that the surfaces to be treated are first made rough by shallow grooves or threadlike channels being worked on them.
The spray lining of a cylinder to a thickness of 1 mm. requires only a few minutes to effect, and actually less time than the fitting of a liner.