F ,., ram the Eh - skiing Boer
Page 44
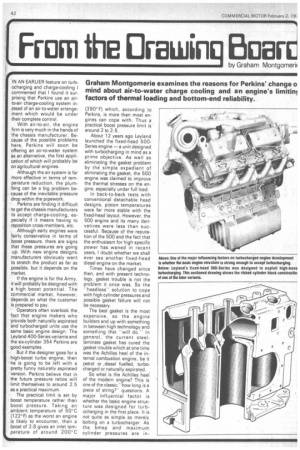
Page 45
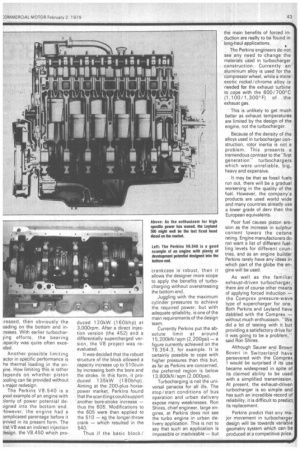
If you've noticed an error in this article please click here to report it so we can fix it.
by Graham Montgomeri( by Graham Montgomeri(
IN AN EARLIER feature on turbocharging and charge-cooling I commented that I found it surprising that Perkins use an airto-air charge-cooling system instead of an air-to-water arrangement which would be under their complete control.
With air-to-air, the engine firm is very much in the hands of the chassis manufacturer. Because of the possible problems here, Perkins will soon be offering an air-to-water system as an alternative, the first application of which will probably be on agricultural engines.
Although the air system is far more effective in terms of temperature reduction, the plumbing can be a big problem because of the inevitable pressure drop within the pipework.
Perkins are finding it difficult to get the chassis manufacturers to accept charge-cooling, especially if it means having to reposition cross-members, etc.
Although early engines were fairly conservative in terms of boost pressure, there are signs that these pressures are going up. With new engine designs, manufacturers obviously want to stretch the product as far as possible, but it depends on the market.
If the engine is for the Army. it will probably be designed with a high boost potential. The commercial market, however, depends on what the customer is prepared to pay.
Operators often overlook the fact that engine makers who provide both naturally aspirated and turbocharged units use the same basic engine design. The Leyland 400-Series variants and the six-cylinder 354 Perkins are good examples.
But if the designer goes for a high-boost turbo engine, then he is going to be left with a pretty funny naturally aspirated version. Perkins believe that in the future pressure ratios will limit themselves to around 2.5 as a practical maximum.
The practical limit is set by boost temperature rather than boost pressure. Taking an ambient temperature of 50cC (122°F) as the worst an engine is likely to encounter, then a boost of 2.8 gives an inlet temperature of around 200°C (390° F) which, according to Perkins, is more than most engines can cope with. Thus a practical boost pressure limit is around 2 to 2.5.
About 12 years ago Leyland launched the fixed-head 500Series engine — a unit designed with turbocharging in mind as a prime objective. As well as eliminating the gasket problem by the simple expedient of eliminating the gasket, the 500 engine was claimed to improve the thermal stresses on the engine, especially under full load.
In back-to-back tests with conventional detachable head designs, piston temperatures were far more stable with the fixed-head layout. However, the 500 engine and its many derivatives were less than successful. Because of the reputation of the 500 and the fact that the enthusiasm for high specific power has waned in recent years, I doubt whether we shall ever see another fixed-head diesel engine on the market.
Times have changed since then, and with present technology, gasket trouble is not the problem it once was. So the "'headless" solution to cope with high cylinder pressures and possible gasket failure will not be necessary.
The best gasket is the most expensive, so the engine builders end up with something in between high technology and something that "'will do." In general, the current steellaminate gasket has cured the gasket trouble which at one time was the Achilles heel of the internal combustion engine, be it petrol or ,diesel fuelled, turbocharged or naturally aspirated.
So what is the Achilles heel of the modern engine? This is one of the classic "how long is a piece of string?questions. A major influential factor is whether the basic engine structure was designed for turbocharging in the first place. It is not quite as simple as merely bolting on a turbocharger. As the bmep and maximum cylinder pressures are in
:reased, then obviously the oading on the bottom end in:reases. With earlier turbochar3ing efforts, the bearing :apacity was quite often exceaided.
Another possible limiting 'actor in specific performance is he thermal loading ,in the en)ine. How limiting this is rather depends on whether piston ooling can be provided without
3 major redesign.
The Perkins V8.540 is a jood example of an engine with D lenty of power potential deiigned into the bottom end. -lowever, the engine had a :iomplicated parentage before it arrived in its present form. The irst V8 was an indirect injection design, the V8.450 which pro
duced 120kW (160bhp) at 3,000rpm. After a direct injection version (the 452) and a differentially supercharged version, the V8 project was reevaluated.
It was decided that the robust structure of the block allowed a capacity increase up to 510cuin by increasing both the bore and the stroke. In this form, it produced 135kW (180bhp). Aiming at the 200-plus horsepower market, Perkins found that the scantlings could support another bore-stroke increase — thus the 605. Modifications to the 606 were then applied to the 510— eg the longer-throw crank — which resulted in the 540.
Thus if the basic block / crankcase is robust, then it allows the designer more scope to apply the benefits of turbocharging without overstressing the bottom end.
Juggling with the maximum cylinder 'pressures to achieve the required power, but with adequate reliability, is one of the main requirements of the design team.
Currently Perkins put the absolute limit at around 15,200kN /sqm (2,200psi) — a figure currently achieved on the T6.354.3, for example. It is certainly possible to cope with higher pressures than this but, as far as Perkins are concerned, the preferred region is below 13,800kN /sqm (2,000psi).
Turbocharging is not the universal panacea for all ills. The stop /start conditions of bus operation and urban delivery expose many weaknesses. Ron Shires, chief engineer, large engines, at Perkins does not see the turbo engine in urban delivery application. This is not to say that such an application is impossible or inadvisable — but the main benefits of forced in. duction are really to be found in long-haul applications.
The Perkins engineers do not see any need to change the materials used in turbocharger construction. Currently an aluminium alloy is used for the compressor wheel, while a more exotic nickel/chrome alloy is needed for the exhaust turbine to cope with the 600/700°C (1,100/1,300°F) of the exhaust gas.
This is unlikely to get much better as exhaust temperatures are limited by the design of the engine, not the turbocharger.
Because of the density of the alloys used in turbocharger construction, rotor inertia is not a problem. This presents a tremendous contrast to the 'first generation" turbochargers which were unreliable, big, heavy and expensive.
It may be that as fossil fuels run out, there will be a gradual worsening in the quality of the fuel. However, the company's products are used world wide and many countries already use a lower grade of dery than the European equivalents.
Poor fuel causes piston erosion as the increase in sulphur content lowers the cetane rating. Engine manufacturers do not want a list of different fuelling levels for different countries, and as an engine builder Perkins rarely have any ideas in which part of the globe the engine wilt be used.
As well as the familiar exhaust-driven turbocharger, there are of course other means of applying forced induction — the Comprex pressure-wave type of supercharger for one. Both Perkins and Leyland have dabbled with the Cornprex — without much enthusiasm. "We did a lot of testing with it but providing a satisfactory drive for it was going to be a problem," said Ron Shires.
Although Saurer and Brown Boveri in Switzerland have persevered with the Comprex. I would be surprised if its use became widespread in spite of its claimed ability to be used with a simplified transmission. At present, the exhaust-driven turbocharger is so simple and has such an incredible record of reliability, it is difficult to predict; its replacement.
Perkins predict that any major movement in turbocharger, design will be towards variable geometry system which can be produced at a competitive price.