A 35-ton Semi-trailer with Rubber Suspension Units
Page 49
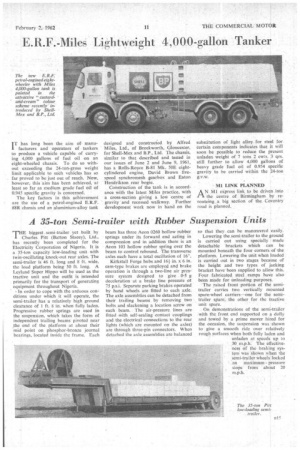
If you've noticed an error in this article please click here to report it so we can fix it.
THE biggest semi-trailer yet built by Charles Pitt (Barton Stacey), Ltd., has recently, been completed for the Electricity Corporation of Nigeria. It is a 35-ton capacity low-loading unit with twin-oscillating knock-out rear axles. The semi-trailer is 46 ft. long and 8 ft. wide, the load platform being 30 ft. long. A Leyland Super Hippo will be used as the tractive unit and the outfit is intended primarily for the transport of generating equipment throughout Nigeria.
In order to cope with the arduous conditions under which it will operate, the semi-trailer has a relatively high ground clearance of 1 ft. 8 in. when fully laden. Progressive rubber springs are used in the suspension, which takes the form of independent trailing beams pivoted near ,the end of the platform at about their mid point on phosphor-bronze journal bearings, located inside the frame. Each
beam has three Aeon 0260 hollow rubber springs under its forward end acting in compression and in addition there is an Aeon 103 hollow rubber spring over the beam to control rebound. The transverse axles each have a total oscillation of 16°.
Kirkstall Forge hubs and 161 in. x 6.in. cam-type brakes are employed and brake operation is through a two-line air pressure system designed to giye 0.5 g deceleration at a brake line pressure of 75 p.s.i. Separate parking brakes operated by hand wheels are fitted to each axle. The axle assemblies can be detached from their trailing beams by removing two bolts and slackening a location screw on each beam. The air-pressure lines are fitted with self-sealing contact couplings and, the electrical connections to the rear lights (which are mounted on the axles) are through three-pin connectors. When detached the axle assemblies are balanced so that they can be manceuvrcd easily.
Lowering the semi-trailer to the ground is carried out using specially made detachable brackets which can be mounted beneath the four corners of the platform. Lowering the unit when loaded is carried out in two stages because of the height and two types of jacking bracket have been supplied to allow this. Four fabricated steel ramps have also been made for unloading purposes.
The raised front portion of the semitrailer carries two vertically mounted spare-wheel carriers—one for the semitrailer spare, the other for the tractive unit spare.
On demonstrations of the semi-trailer with the front end supported on a dolly and towed by a prime mover hired for the occasion, the suspension was shown to give a smooth ride over relatively rough surfaces when both fully laden and unladen at speeds up to 30 m.p.h. The effectiveness of the braking system was shown when the semi-trailer wheels locked on maximum pressure stops from about 20 m.p.h.