%RTICULATION
Page 87
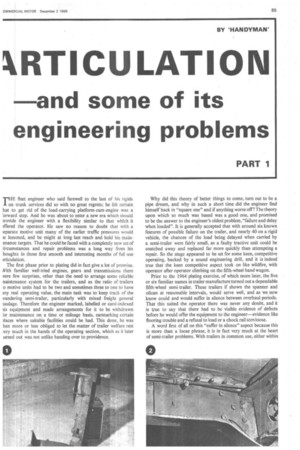
Page 88
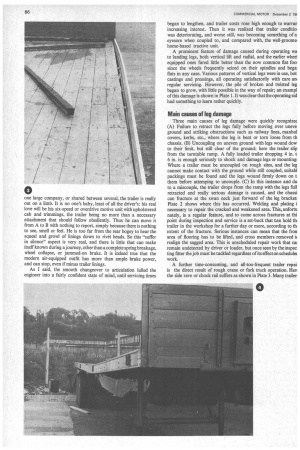
Page 89
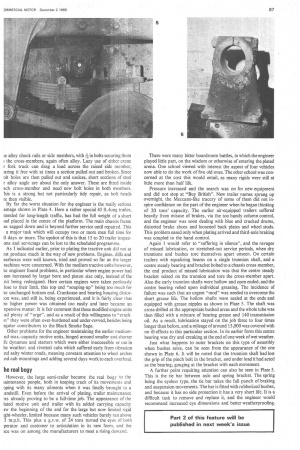
If you've noticed an error in this article please click here to report it so we can fix it.
and some of its engineering problems
PART 1
rHE fleet engineer who said farewell to the last of his rigids on trunk services did so with no great regrets; he felt certain hat to get rid of the load-carrying platform-cum-engine was a brward step. And he was about to enter a new era which should uovide the engineer with a flexibility similar to that which it )ffered the operator. He saw no reason to doubt that with a eparate motive unit many of the earlier traffic pressures would x lessened, and he might at long last reach and hold his mainenance targets. That he could be faced with a completely new set of ;ircumstances and repair problems was a long way from his houghts in those first smooth and interesting months of full use trticulation.
The first phase prior to plating did in fact give a lot of promise. With familiar well-tried engines, gears and transmissions there vere few surprises, other than the need to arrange some reliable naintenance system for the trailers, and as the ratio of trailers o motive units had to be two and sometimes three to one to have my real operating value, the main task was to keep track of the vandering semi-trailer, particularly with mixed freight general mulage. Therefore the engineer marked, labelled or card-indexed Us equipment and made arrangements for it to be withdrawn or maintenance on a time or mileage basis, earmarking certain )laces where suitable facilities could be had. This done, he was hen more or less obliged to let the matter of trailer welfare rest rery much in the hands of the operating section, which as it later urned out was not unlike handing over to providence.
Why did this theory of better things to come, turn out to be a pipe dream, and why in such a short time did the engineer find himself back in "square one" and if anything worse off? The theory upon which so much was based was a good one, and promised to be the answer to the engineer's oldest problem, "failure and delay when loaded". It is generally accepted that with around six known features of possible failure on the trailer, and nearly 40 on a rigid vehicle, the chances of the load being delayed when carried by a semi-trailer were fairly small, as a faulty tractive .unit could be snatched away and replaced far more quickly than attempting a repair. So the stage appeared to be set for some keen, competitive operating, backed by a sound engineering drill, and it is indeed true that the keen competitive aspect took on like wildfire, with operator after operator climbing on the fifth-wheel band wagon.
Prior to the 1964 plating exercise, of which more later, the five or six familiar names in trailer manufacture turned out a dependable fifth-wheel semi-trailer. These trailers if shown the spanner and oilcan at reasonable intervals, would serve well, and as we now know could and would suffer in silence between overhaul periods. That this suited the operator there was never any doubt, and it is true to say that there had to be visible evidence of defects before he would offer the equipment to the engineer—evidence like flooring trouble and a refusal to load or a chock rail torn loose.
A word first of all on this "suffer in silence" aspect because this is more than a loose phrase, it is in fact very much at the heart of semi-trailer problems. With trailers in common use, either within one large company, or shared between several, the trailer is really out on a limb. It is no one's baby, least of all the driver's: his real love will be his six-speed or overdrive motive unit with upholstered cab and trimmings, the trailer being no more than a necessary attachment that should follow obediently. Thus he can move it from A to B with nothing to report, simply because there is nothing to see, smell or feel. He is too far from the rear bogey to hear the squeal and growl of linings down to rivet heads. So this "suffer in silence" aspect is very real, and there is little that can make itself known during a journey, other than a complete spring breakage, wheel collapse, or jammed-on brake. It is indeed true that the modern air-equipped outfit has more than ample brake power, and can stop, even if minus trailer linings.
As I said, the smooth changeover to articulation lulled the engineer into a fairly confident state of mind, until servicing times began to lengthen, and trailer costs rose high enough to warran increasing interest. Then it was realized that trailer conditio was deteriorating, and worse still; was becoming something of a eyesore when coupled to, and compared with, the well-groome home-based tractive unit.
A prominent feature of damage caused during operating wa to landing legs, both vertical lift and radial, and the earlier wheel equipped ones fared little better than the now common flat fool since the wheels frequently seized on their spindles and begai flats in any case. Various patterns of vertical legs were in use, bot castings and pressings, all operating satisfactorily with care as regular servicing. However, the pile of broken and twisted leg began to grow, with little possible in the way of repair; an exampl of this damage is shown in Plate 1. It was clear that the operating sid had something to learn rather quickly.
Main causes of leg damage Three main causes of leg damage were quickly recognize( (Al) Failure to retract the legs fully before moving over uneve ground and striking obstructions such as railway lines, manhol covers, kerbs, etc., where the leg is bent or torn loose from th chassis. (B) Uncoupling on uneven ground with legs wound dow to their limit, but still clear of the ground; here the trailer slip from the turntable ramp. A fully loaded trailer dropping 4 in. t 6 in. is enough seriously to shock and damage legs or mounting: Where a trailer must be uncoupled on rough sites, and the leg cannot make contact with the ground while still coupled, suitabl packings must be found and the legs wound firmly down on t them before attemping to uncouple. (C) In this instance and du to a miscouple, the trailer drops from the ramp with the legs full retracted and really serious damage is caused, and the chassi can fracture at the swan neck just forward of the leg bracken Plate 2 shows where this has occurred. Welding and plating i necessary to repair the cracked and weakened area. This, unfortu nately, is a regular feature, and to come across fractures at thi point during inspection and service is a set-back that tan hold till trailer in the workshop for a further day or more, according to th extent of the fracture. Serious instances can mean that the fron area of flooring has to be lifted, and cross members removed n realign the sagged area. This is unscheduled repair work that cal remain undetected by driver or loader, but once seen by the inspec ting fitter the job must be tackled regardless of its effect on schedule( work.
A further time-consuming, and all-too-frequent trailer mind] is the direct result of rough crane or fork truck operation. Hen the side rave or chock rail suffers as shown in Plate 3. Many trailer! se alloy chock rails or side members, with in bolts securing them ) the cross-members, again often alloy. Lazy use of either crane r fork truck can drag a load across the raised side member, ming it free with at times a section pulled out and broken. Since nit holes are then pulled out and useless, short sections of steel r alloy angle are about the only answer. These are fitted inside ach cross-member and need new bolt holes in both members. 'his is a strong but not particularly tidy repair, as bolt heads re then visible.
By far the worst situation for the engineer is the really serious amage shown in Plate 4. Here a rather special 45 ft.-long trailer, itended for long-length traffic, has had the full weight of a short ad placed in the centre of the platform. The main chassis frame as sagged down and is beyond further service until repaired. This a major task which will occupy two or more men full time for 0 days or more. The upshot of this is that 15 to 20 trailer inspecons and servicings can be lost to the scheduled programme.
As I indicated earlier, prior to plating the tractive unit did not at rst produce much in the way of new problems. Engines, diffs and earboxes were well known, tried and proved so far as the larger iachines were concerned. With the medium tractive units however, he engineer found problems, in particular where engine power had leen increased by larger bore and piston size only, instead of the nit being redesigned. Here certain engines were taken perilously lose to their limit, this top end "souping-up" being too much for he unchanged bottom end. Crankcase and bearing housing distorion was, and still is, being experienced, and it is fairly clear that he higher power was obtained too easily and later became an xpensive matter. It is fair comment that these modified engine units ad plenty of "urge", and as a result of this willingness to " crackin" they were often over-burdened and under-revved, besides being egular contributors to the Black Smoke Saga.
Other problems for the engineer maintaining the earlier mediumrid max.-capacity motive units, hinged around smaller and shorter fe dynamos and starters which were either inaccessible or out in he weather; and rivetted cabs which suffered early from vibration rid salty winter roads, meaning constant attention to wheel arches aid cab mountings and adding several days work to each overhaul.
he real bogy However, the large semi-trailer became the real bogy to the laintenance people, both in keeping track of its movements and oping with its many ailments when it was finally brought to a :andstill. Even before the arrival of plating, trailer maintenance us already proving to be a full-time job. The appearance of the lated motive unit and trailer with its added carrying capacity aw the beginning of the end for the large but now limited rigid ight-wheeler, limited because many such vehicles barely ran above 3 m.p.h. This plus a g.v.w. of 24 tons turned the eyes of both perator and customer to articulation in its new form, and the see was on among the manufacturers to meet a rising demand. There were many bitter boardroom battles, in which the engineer played little part, on the wisdom or otherwise of entering the plated arena. One school viewed with interest the aspect of four vehicles now able to do the work of five old ones. The other school was concerned at the cost this would entail, as many rigids were still at little more than half life.
Pressure increased and the search was on for new equipment and did not stop at "Buy British". New trailer names sprang up overnight, the Meccano-like tracery of some of them did not inspire confidence on the part of the engineer when he began thinking of 20 tons' capacity. The earlier air-equipped trailers suffered heavily from misuse of brakes, via the too handy column control, and the engineer was soon dealing with blue and cracked drums, distorted brake shoes and loosened back plates and wheel studs. This problem eased only when plating arrived and third-axle braking was coupled to the hand control.
Again I would refer to "suffering in silence", and the ravages of missed lubrication, or stretched-out service periods, when dry trunnions and bushes tore themselves apart unseen. On certain trailers with equali7ing beams on a single trunnion shaft, and a centre steady bearing and bracket bolted to a chassis cross-member, the end product of missed lubrication was that the centre steady bracket seized on the trunnion and tore the cross-member apart. Also the early trunnion shafts were hollow and open ended, and the centre bearing relied upon individual greasing. The incidence of failure was such that an urgent "mod" was needed to overcome the short grease life. The hollow shafts were sealed at the ends and equipped with grease nipples as shown in Plate 5. The shaft was cross-drilled at the appropriate bushed areas and the whole tube was then filled with a mixture of bearing grease and 140 transmission oil. As a result, lubrication stayed on the job three to four times longer than before, and a mileage of around 15,000 was covered with no ill-effects to this particular section. In its earlier form this centre bearing was dry and creaking at the end of one week of wet weather.
Just what happens to outer brackets on this type of assembly when bushes seize, can be seen from the appearance of the one shown in Plate 6. It will be noted that the trunnion shaft had lost the grip of the pinch bolt in the bracket, and under load it had acted as the bearing, gouging at the bracket with each movement.
A further point requiring attention can also be seen in Plate 5. This is the tie bar between axle and spring bracket. The spring being the eyeless type, the tie bar takes the full punch of braking and suspension movements. The bar is fitted with rubberized bushes, and because it has no side protection it has a very short life. It is a difficult task to remove and replace it, and the engineer would recommend increased eye dimensions and better weatherproofing.