Demountable Bodies Are The Best Solution
Page 66
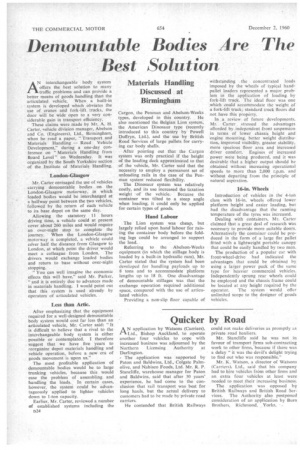
If you've noticed an error in this article please click here to report it so we can fix it.
AN interchangeable body system offers the best solution to many traffic problems and can provide a better means of goods handling than the articulated vehicle. When a built-in system is developed which obviates the use of cranes and fork-lift trucks, the door will be wide open to a very considerable gain in transport efficiency.
These claims were made by Mr. A. 1-1. Carter, vehicle division manager, Abelson and Co. (Engineers), Ltd., Birmingham, when he read a paper, "Transport and Materials Handling — Road Vehicle Development," during a one-day conference on "Materials Handling from Board Level '• on Wednesday. It was organized by the South Yorkshire section of the Institute of Materials Handling.
London-Glasgow
Mr. Carter envisaged the use of vehicles carrying demountable bodies on the London-Glasgow motorway, in which loaded bodies would be interchanged at a halfway point between the two vehicles, followed by the return of each vehicle to its base depot on the same day.
Allowing the statutory 11 hours driving time, a vehicle could at present cover about 260 miles and would require an over-night stop to complete the journey. When the London-Glasgow motorway is completed, a vehicle could cdver half the distance from Glasgow to London, at which point the driver would meet a colleague from London. The drivers would exchange loaded bodies and return to base without over-night stopping.
"You can well imagine the economic effects this will have," said Mr. Parker, "and it is entirely due to advances made in materials handling. I would point out that this system is used already by operators of articulated vehicles.
Less than Artie.
After emphasizing that the equipment required for a well-designed demountable body system would cost far less than an articulated vehicle, Mr. Carter said: "It is difficult to believe that a rival to the interchangeable body system is either possible or contemplated. I therefore suggest that we have five years to reorganize depot materials handling and vehicle operation, before a new era of goods movement is upon us."
The most profitable application of demountable bodies would be to large trunking vehicles, because this would case the problem of assembling and handling the loads.. In certain cases, however, the system could be advantageously applied to lighter vehicles down to 1-ton capacity.
Earlier, Mr. Carter, reviewed a number of established systems including the D24 Cargon, the Penman and Abelson-Weeks types, developed in this country. He also mentioned the -Belgian Lion system, the American Dinosaur type (recently introduced to this country by Powell Duffryn, Ltd.), and the use by British Road Services of large pallets for carrying car body shells.
• After pointing out that the Cargon system was only practical if the height of the loading deck approximated to that of the vehicle, Mr. Carter said that the necessity to employ a permanent set of unloading rails in the case of the Penman systenri reduced flexibility.
The Dinosaur system was relatively costly, and its use increased the taxation
weight -of the vehicle. Because the container was tilted to a steep angle when loading, it could only be applied for certain types of goods.
Hand Labour
The Lion system was cheap, but largely relied upon hand labour for raising the container body before the folding legs could be arranged to support the load.
Referring to the Abelson-Weeks equipment (in which the stillage body is loaded by a built-in hydraulic ram), Mr. Carter stated that the system had been developed for handling payloads up to 8 tons and to accommodate platform lengths up to 18 ft. One disadvantage of demountable stillages was that the exchange operation required additional space, compared with the use of articulated vehicles.
Providing a non-slip floor capable of withstanding the concentrated loads imposed by the wheels of typical handpallet loaders represented a major problem in the application of loading by fork-lift truck. The ideal floor was one which could accommodate the weight of a fork-lift truck; standard truck floors did not have this property.
In a review of future developments, Mr. Carter. stressed the advantages afforded by independent front suspension in terms of lower chassis height and engine mounting, better weight distribution, improved visibility, greater stability, more spacious floor area and increased driver comfort. Engines of increased power were being produced, and it was desirable that a higher output should be obtained without increasing operational speeds to more than 2,000 r.p.m. and without departing from the principle of natural aspiration.
16-in. Wheels
Introduction of vehicles in the 4-ton class with 16-in. wheels offered lower platform height and easier loading, but had the disadvantage that the running temperature of the tyres was increased.
Dealing with containers, Mr. Carter claimed that a great deal of research was necessary to provide more suitable doors. Alternatively the container could be produced in the form of a large flat pallet fitted with a lightweight portable canopy that could be easily handled by two men.
The production of a popular car with front-wheel-drive had indicated the advantages that could be obtained by using a larger power pack of the same type for heavier commercial vehicles. Independently sprung rear wheels could be employed and the chassis frame could be located at any height required by the operator. The system would offer unlimited scope to the designer of goods vehicles.