FACING THE iNctuorn ON
Page 19
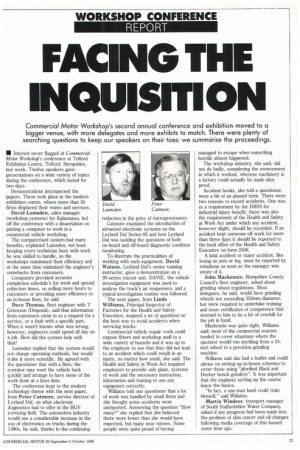
If you've noticed an error in this article please click here to report it so we can fix it.
Commercial Motor Workshop's second annual conference and exhibition moved to a bigger venue, with more delegates and more exhibits to match. There were plenty of searching questions to keep our speakers on their toes: we summarise the proceedings.
• Interest never flagged at Commercial Motor Workshop's conference at Telford Exhibition Centre, Telford, Shropshire, last week. Twelve speakers gave presentations on a wide variety of topics during the conference, which lasted for two days.
Demonstrations interspersed the papers. These took place in the modern exhibition centre, where more than 50 firms displayed their wares and services.
David Lumsden, sales manager (workshop systems) for Kalamazoo, led off the conference with a dissertation on putting a computer to work in a commercial vehicle workshop.
The computerised system had many benefits, explained Lumsden, not least keeping every technician busy with work he was skilled to handle, so the workshops maximised their efficiency and at the same time minimised the engineer's comebacks from customers.
Computers provided accurate completion schedule's for work and spread collection times, so selling more hours to customers or providing more efficiency to an in-house fleet, he said.
Dave Thomas, fleet engineer with T Graveson (Disposal), said that information from customers came in as a request for a service, or a fault with a specific part. When it wasn't known what was wrong, however, engineers could spend all day on a job. How did the system help with that?
Lumsden replied that the system would ort. change operating methods, but would rrake it more scientific. He agreed with the questioner that with a fleet, the ry)erator may want the vehicle back qiickly and arrange to have some of the v•ork done at a later date.
The conference kept to the modern technology theme with the next paper, from Peter Cutmore, service director of Leyland Daf, on what electronic d agnostics had to offer in the HGV sm-vicing field. The automotive industry would see a considerable increase in the use of electronics on trucks during the 1390s, he said, thanks to the continuing
reduction in the price of microprocessors.
Cutmore examined the introduction of advanced electronic systems on the Leyland Daf Series-95 and how Leyland Daf was tackling the questions of both on-board and off-board diagnostic condition monitoring.
To illustrate the practicalities of working with such equipment, David Watson, Leyland Dafs senior training instructor, gave a demonstration on a 95-series tractor unit. DAVIE, the vehicle investigation equipment was used to analyse the truck's air suspension, and a typical investigation routine was followed.
The next paper, from Linda Williams, Principal Inspector of Factories for the Health and Safety Executive, inspired a lot of questions on the best way to avoid accidents when servicing trucks.
Commercial vehicle repair work could expose fitters and workshop staff to a wide variety of hazards and it was up to the employer to see that they did not lead to an accident which could result in an injury, no matter how small, she said. The Health and Safety at Work Act required employers to provide safe plant, systems of work and the necessary instruction, information and training to use any equipment correctly.
Williams told one questioner that a lot of work was handled by small firms and she thought some accidents went unreported. Answering the question "How many?" she replied that she believed there were fewer than she would have expected, but many near misses. Some people were quite proud of having managed to escape when something horrific almost happened.
The workshop industry, she said, did not do badly, considering the environment in which it worked, whereas machinery in a factory could actually be made idiot proof.
Accident books, she told a questioner, were a bit of an abused term. There were two reasons to record accidents. One was as a requirement by the DHSS for industrial injury benefit; there was also the requirement of the Health and Safety at Work Act under which any accident, however slight, should be recorded. If an accident kept someone off work for more than three days it should be reported to the local office of the Health and Safety Executive on form 2508.
A fatal accident or major accident, like losing an arm or leg, must be reported by telephone as soon as the manager was aware of it.
John Mackenzie, Hampshire County Council's fleet engineer, asked about grinding wheel regulations. Most delegates, he said, would have grinding wheels not exceeding 250nun diameter, but were required to undertake training and issue certificates of competence that seemed to him to be a bit of overkill for the job in hand.
Mackenzie was quite right, Williams said; most of the commercial courses tended to cover situations where the operator would run anything from a 24inch wheel to a precision grinding
machine.
Williams said she had a leaflet and could advise on setting up in-house schemes to cover those using "glorified Black and Decker bench grinders". It was important that the engineer setting up the course knew the basics.
"In fact, a one-man band could train himself," said Willaims.
Martin Windsor, transport manager of South Staffordshire Water Company, asked if any progress had been made into the problem of skin cancer and oil changes following media coverage of this hazard some time ago.