Emn Drivers &Mechanics
Page 21
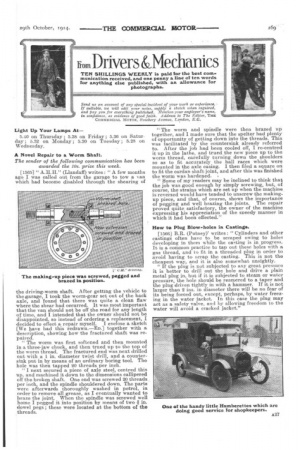
If you've noticed an error in this article please click here to report it so we can fix it.
Light Up Your Lamps At
5.40 on Thursday ; 5.38 on Friday ; 3.36 on Saturday; 5.32 on Monday; 5.30 on Tuesday ; 5.28 on Wednesday.
A Novel Repair to a Worm Shaft.
The sender of the following communication has been awarded the 103. prize this week.
[1565] " A.H.H." (Llandaff) writes : "A few months ago I was called out from the garage to tow a van which had become disabled through the shearing of
the driving-worm shaft. After getting the vehicle to the garage, I took the worm-gear set out of the back axle, and found that there was quite a clean flaw where the shear had occurred. It was most important that the van should not be off the road for any length of time, and I intended that the owner should not be disappointed, so instead of ordering a replacement, I decided to effect a repair myself. I enclose a sketch [We have had this redrawn.—En] together with a description, showing how the fractured shaft was repaired.
" The worm was first softened and then mounted in a three-jaw chuck, and then trued up to the top of the worm thread. The fractured end was next drilled out with a 1 in. diameter twist drill, and a countersink put in by means of an ordinary boring tool. The hole was then tapped 20 threads per inch.
" I next secured a piece of axle steel, centred this up, and machined it down to the dimensions callipered off the broken shaft. One end was screwed 20 threads per inch, and the spindle shouldered down. The parts were afterwards thoroughly washed in petrol, in order to remove all grease, as I eventually wanted to braze the joint. When the spindle was screwed well home I pegged it into position by means of two in. dowel pegs ; these were located at the bottom of the threads. "The worm and spindle were then brazed up together, and I made sure that the spelter had plenty of opportunity of getting down into the threads. This was facilitated by the countersink already referred to. After the job had been cooled off, I re-centred it up in the lathe, and trued the new piece up to the worm thread, carefully turning down the shoulders so as to fit accurately the ball races which were mounted in the axle casing. I then filed a square on to fit the cardan shaft joint, and after this was finished the worm was hardened.
" Some of my readers may be inclined to think that the job was good enough by simply screwing, but, of course, the strains which are set up when the machine is reversed would have tended to unscrew the makingup piece, and that, of course, shows the importance of pegging and well brazing the joints. The repair proved quite satisfactory, the owner of the machine expressing his appreciation of the speedy manner in which it had been effected."
How to Plug Blow-holes in Castings.
[1566] B. R. (Putney)' writes : "Cylinders and other castings often have to be scraped owing to holes developing in them while the casting is in progress. It is a common practice to tap out these holes with a gas thread, and to fit in a threaded plug in order to avoid having to scrap the casting. This is not the cheapest way, and it is also somewhat unsightly.
" If the plug is not subjected to any great pressure it is better to drill out the hole and drive a plain metal plug in, but if it is subjected to steam or water pressure, the hole should be reamered to a taper and the plug driven tightly in with a hammer. If it is not larger than 2 ins, in diameter there will be no fear of its being forced out, except, perhaps, by water freezing in the water jacket. In this case the plug may act as a safety valve, and by allowing freedom to the water will avoid a cracked jacket."