WHERE A LIGHT ALLOY BODY IS BEING PRODUCED.
Page 94
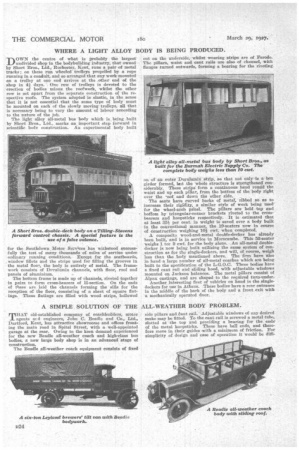
If you've noticed an error in this article please click here to report it so we can fix it.
TIA OWN the centre of what is probably the largest 1.1 undivided shop in the bodybuilding industry, that owned by Short Bros., Ltd., Rochester, Kent, runs a pair of metal tracks; on these run wheeled trolleys propelled by a rope running in a conduit, and so arranged that any work mounted on a trolley at one end arrives at the other end of the shop in 44 days. One row of trolleys is devoted to the erection of bodies minus the rootwork, whilst the other row is set apart from the separate construction of the respective roofs. The system adopted is elastic, in the sense that it is not essential that the same type of body must be mounted on each of the slowly moving trolleys, all that is necessary being to vary the amount of labour according to the nature of the job.
The light alloy all-metal bus body which is being built by Short Bros., Ltd., marks an important step forward in scientific body construction. An experimental body built for the Southdown Motor Services has withstood successfully the test of many thousands of miles of service under ordinary running conditions. Except for the seatboards, window fillets and the strips used for filling the grooves in the metal floor, the body is entirely of metal. The framework consists of Deralumin channels, with floor, roof and panels of aluminium. The bottem frame is made up of channels, riveted together in pairs to form cross-hearers of 1E-section. On the ends of these are laid the channels forming the sills for the reception of the floor, consisting of a sheet of square flutings. These flutings are filled with wood strips, hollowed Out on the underside, whilst wearing strips are of Ferodo. The pillars, waist and cant rails are also of channel, with flanges turned outwards, forming a bearing for the riveting on of an outer Duralumin strip, so that not only is a box girder formed, tut the whole structure Is strengthened considerably. These strips form a continuous baud roniid the waist and up each pillar, from the bottom of the body right over the -oaf and down the other side. _
The seats have curved backs of metal, ribbed sso as to increase their rigidity, a similar style of work being used' for the wheel-arch paliel. The pillars are held •top and bottom by triangular-corner brackets riveted to the erdssbearers and hoopsticks respectively. It is estimated that at least 334 per cent. in weight is saved over a body built ha the conventional manner, the 19-seaters now in course of construction weighing 1Q cwt. when completed. A composite wood-and-metal double-decker has already been built, and is in service in Morecambe. This 53-seater " weighs 1 tor 0 cwt. for the body alone. An all-metal doubledecker is now being built utilizing the same system of construction as for the single-deckers, and -svill, of course, weigh less than the body mentioned above. The firm have also in hand a large number of all-metal coaches which are being built to the specification of the L.G.O.C. These bodies have a fixed cant rail and sliding hood, with adjustable windows mounted on Jackson balances. The metal pillars consist of Alpax castings, and are shaped to the required turn-under.
Another interesting fleet of vehicles on hand is the singledeckers for use in Athens. These bodies have a rear entrance in the middle of the back of the body and a front exit with a mechanically operated door.