CHAR
Page 42
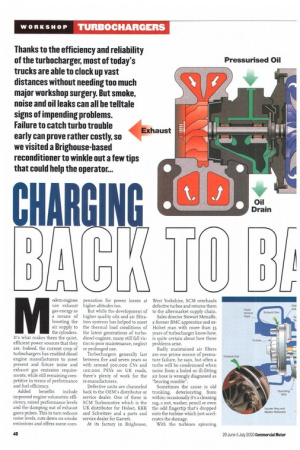
Page 43
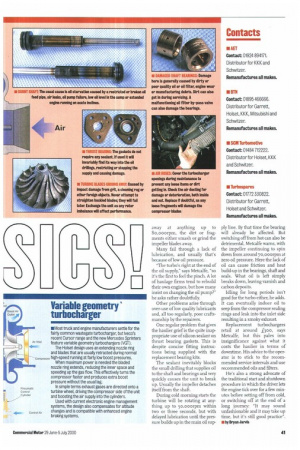
If you've noticed an error in this article please click here to report it so we can fix it.
IIIodem engines use exhaust gas energy as a means of boosting the air supply to the cylinders. It's what makes them the quiet, efficient power sources that they are. Indeed, the current crop of turbochargers has enabled diesel engine manufacturers to meet present and future noise and exhaust gas emission requirements, while still remaining competitive in terms of performance and fuel efficiency Added benefits include improved engine volumetric efficiency, raised performance levels and the damping out of exhaust gases pulses. This in turn reduces noise levels, cuts down on smoke emissions and offers some corn
pensation for power losses at higher altitudes too.
But while the development of higher quality oils and air filtration systems has helped to meet the thermal load conditions of the latest generations of turbodiesel engines, many still fall victim to poor maintenance, neglect or prolonged use.
Turbochargers generally last between five and seven years so with around 500,000 CVs and roo,000 PSVs on UK roads, there's plenty of work for the re-manufacturers.
Defective units are channeled back to the OEM's distributor or service dealer. One of these is SCM Turbomotive which is the UK distributor for Holset, KKK and Schwitzer and a parts and service dealer for Garrett.
At its factory in Brighouse, West Yorkshire, SCM overhauls defective turbos and returns them to the aftermarket supply chain.
Sales director Stewart Metcalfe, a former BMC apprentice and exHolset man with more than 35 years of turbocharger know-how, is quite certain about how these problems arise.
Badly maintained air filters are one prime source of premature failure, he says, but often a turbo will be condemned when noise from a holed or ill-fitting air hose is wrongly diagnosed as "bearing rumble".
Sometimes the cause is old trunking, deteriorating from within; occasionally it's a deaning rag, a nut, washer, pencil or even the odd fingertip that's dropped onto the turbine which just accelerates the damage.
With the turbines spinning away at anything up to 80,000rpm, the dirt or fragments either smash or grind the impeller blades away.
Many fail through a lack of lubrication, and usually that's because of low oil pressure.
"The turbo's right at the end of the oil supply," says Metcalfe, "so it's the first to feel the pinch. A lot of haulage firms tend to rebuild their own engines, but how many insist on changing the oil pump?" he asks rather doubtfully.
Other problems arise through over-use of low quality lubricants and, all too regularly, poor craftsmanship by the repairers.
One regular problem that gives the haulier grief is the quite inappropriate use of silicon sealant on thrust bearing gaskets. This is despite concise fitting instructions being supplied with the replacement bearing kits.
The sealant inevitably blocks the small drilling that supplies oil to the shaft and bearings and very quickly causes the unit to break up. Usually the impeller detaches itself from the shaft.
During cold morning starts the turbine will be rotating at anything up to so, 000rpm within two or three seconds, but with delayed lubrication until the pressure builds up in the main oil sup. ply line. By that time the bearing will already be affected. But switching off from hot can also be detrimental, Metcalfe warns, with the impeller continuing to spin down from around 70,000rpm at zero oil pressure. Here the lack of oil can cause friction and heat build-up in the bearings, shaft and seals. What oil is left simply breaks down, leaving varnish and carbon deposits.
Idling for long periods isn't good for the turbo either, he adds. It can eventually induce oil to seep from the compressor sealing rings and leak into the inlet side resulting in a smoky exhaust.
Replacement turbochargers retail at around £300, says Metcalfe, but this pales into insignificance against what it costs the haulier in terms of downtime. His advice to the operator is to stick to the recommended service intervals and use recommended oils and filters.
He's also a strong advocate of the traditional start and shutdown procedure in which the driver lets the engine tick over for a few minutes before setting off from cold, or switching off at the end of a long journey: "It may sound unfashionable and it may take up time, but it's still good practice".
• by Bryan Jarvis