OFF THE RAILS
Page 39
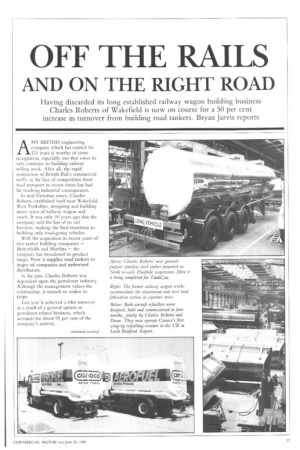
Page 40
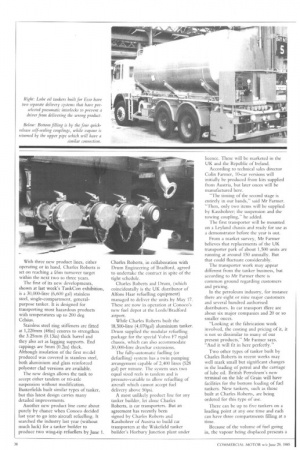
Page 41
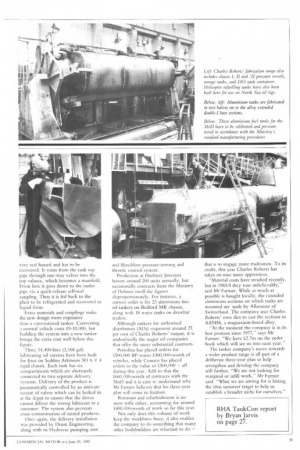
If you've noticed an error in this article please click here to report it so we can fix it.
AND ON THE RIGHT ROAD
Having discarded its long established railway wagon building business Charles Roberts of Wakefield is now on course for a 50 per cent increase in turnover from building road tankers. Bryan Jarvis reports
ANY BRITISH engineering company which has existed for 125 years is worthy of some recognition, especially one that owes its very existence to building railway rolling stock. After all, the rapid contraction of British Rail's commercial traffic in the face of competition from road transport in recent times has had far reaching industrial consequences.
In mid-Victorian times, Charles Roberts established itself near Wakefield, West Yorkshire, designing and building many types of railway wagon and coach. It was only 10 years ago that the company sold the last of its rail business, making the final transition to building only road-going vehicles.
With the acquisition in recent years of two tanker building companies — Butterfields and Murfitts — the company has broadened its product range. Now it supplies road tankers to major oil companies and authorised distributors.
In the past, Charles Roberts was dependent upon the petroleum industry. Although the management values the relationship, it intends to widen its scope. _ Last year it achieved a 8:4m turnover as a result of a general upturn in petroleum related business, which accounts for about 95 per cent of the company's activity. With three new product lines, either operating or in hand, Charles Roberts is set on reaching a £6m turnover target within the next two to three years.
The first of its new developments, shown at last week's TankCon exhibition, is a 30,000-litre (6,600 gal) stainless steel, single-compartment, generalpurpose tanker. It is designed for transporting most hazardous products with temperatures up to 200 deg Celsius.
Stainless steel ring stiffeners are fitted at 1,220mm (48in) centres to strengthen the 3.25mm (0.13in) thick barrel and they also act as lagging supports. End cappings are 5mrn (0,2in) thick.
Although insulation of the first an:del produced was covered in stainless steel, both aluminium and glass reinforced polyester clad versions are available.
The new design allows the tank to accept either tandem or tri-axle suspension without modification. Butterfields built similar types of tanker, but this latest design carries many detailed improvements.
Another new product line came about purely by chance when Conoco decided last year to go into aircraft refuelling. It searched the industry last year (without much luck) for a tanker builder to produce two wing-tip refuellers by June 1. Charles Roberts, in collaboration with Drum Engineering of Bradford, agreed to undertake the contract in spite of the tight schedule.
Charles Roberts and Drum, (which coincidentally is the UK distributor of Alfons Haar refuelling equipment) managed to deliver the units by May 17. These are now in operation at Conoco's new fuel depot at the Leeds/Bradford airport.
While Charles Roberts built the 18,500-litre (4,070gal) aluminium tanker. Drum supplied the modular refuelling package for the special Volvo F7 rigid chassis, which can also accommodate 30,000-litre drawbar extensions.
The fully-automatic fuelling (or defuelling) system has a twin pumping arrangement capable of 2,400 litres (528 gal) per minute. The system uses two equal sized reels in tandem and is pressure-variable to allow refuelling of aircraft which cannot accept fuel delivery above 50psi.
A most unlikely product line for any tanker builder, let alone Charles Roberts, is car transporters. But an agreement has recently been signed by Charles Roberts and Kassbohrer of Austria to build car transporters at the Wakefield tanker builder's Horbury Junction plant under licence. These will be marketed in the UK and the Republic of Ireland.
According to technical sales director Cohn Farmer, 10-car versions will initially be produced from kits supplied from Austria, but later onces will be manufactured here.
"The timing of the second stage is entirely in our hands," said Mr Farmer. "Then, only two items will be supplied by Kassbohrer; the suspension and the towing coupling," he added.
The first transporter will be mounted on a Leyland chassis and ready for use as a demonstrator before the year is out.
From a market survey, Mr Farmer believes that replacements of the UK transporter park of about 1,500 units are running at around 150 annually. But that could fluctuate considerably.
The transporter work may appear different from the tanker business, but according to Mr Farmer there is common ground regarding customers and pricing.
In the petroleum industry, for instance there are eight or nine major customers and several hundred authorised distributors. in car transport tbere are about six major companies and 20 or so smaller onces, "Looking at the fabrication work involved, the costing and pricing of it, it is not so dissimilar to many of our present products," Mr Farmer says. "And it will fit in here perfectly."
Two other types of tanker built by Charles Roberts in recent weeks may well mark small but significant changes in the loading of petrol and the carriage of lube oil. British Petroleum's new terminal on the Isle of Grain will have facilities for the bottom loading of fuel tankers. New tankers, such as those built at Charles Roberts, are being ordered for this type of use.
There can be up to five tankers on a loading point at any one time and each can have three compartments filling at a time.
Because of the volume of fuel going in, the vapour being displaced presents a very real hazard and has to he recovered. It vents from the tank top pipe through one-way valves into the top valance, which becomes a manifold. From here it goes down to the outlet pipe via a quick-release self-seal coupling. Then it is fed back to the plant to be refrigerated and recovered in liquid form.
Extra materials and couplings make the new design more expensive than a conventional tanker. Converting a normal vehicle costs £9-10,000, but building the system into a new tanker brings the extra cost well below this figure.
Three 14,400-litre (3,168 gal) lubricating oil carriers have been built for Esso on Seddon Atkinson 301 6 x 4 rigid chassis. Each tank has six compartments which are alternately connected to two separate delivery systems. Delivery of the product is pneumatically controlled by an intricate system of valves which can be locked in at the depot to ensure that the driver cannot deliver the wrong lubricant to a customer. The system also prevents cross contamination of mixed products.
Once again, the delivery installation was provided by Drum Engineering, along with its Hydravac pumping unit and Maxiblow pressure-sensing and throttle control system.
Production at Horbury junction hovers around 200 units annually, but occasionally contracts from the Ministry of Defence swell the figures disproportionately. For instance, a current order is for 23 aluminium fuei oil tankers on Bedford MK chassis, along with 18 water tanks on drawbar trailers.
Although tankers for authorised distributors (ADs) respresent around 23 per cent of Charles Roberts' output, it is undoubtedly the major oil companies that offer the more substantial contracts.
Petrofina has placed orders for £50X.0,000 BP wants £400,000-worth of vehicles, while Conoco has placed orders to the value of .£500,000 — all during this year. Add to that the £660,000-worch of contracts with the MoD and it is easy tc understand why Mr Farmer believes that his three-year plan will come to fruition.
Remount and refurbishment is no mere trifle either, accounting for around £400,000-worth of work so far this year.
Not only does this volume of work keep the workforce busy, it also enables the company to do something that many other bodybuilders are reluctant to do — that is to engage more tradesmen. To its credit, this year Charles Roberts has taken on nine more apprentices.
"Material costs have steadied recently, but in 1983/4 they rose unbelievably," said Mr Farmer. While as much as possible is bought locaily, the extended aluminium sections on which tanks are mounted are :nacle by Allusuissc of Switzerland. The company uses Charles Roberts' own dies to cast the sections in AA5454, a magnesium-based alloy.
"At the moment the company is in its best position since 1977," says Mr Farmer. "We have £2.7m on the order book which will see us into next year."
The tanker company's move towards a wider product range is all part of a deliberate three-year plan to help strengthen and develop the company still further. "We are not looking for marginal or infill work," Mr Farmer said. "What we are aiming for is hitting thei6in turnover target to help us establish a broader niche for ourselves."