Britain's First All-aluminium Semi-trailer Van?
Page 50
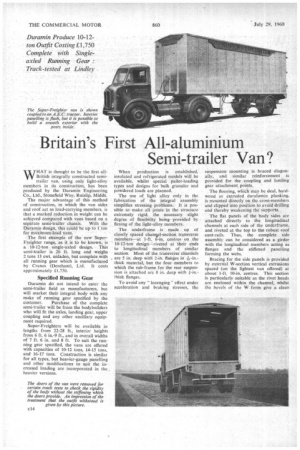
Page 51
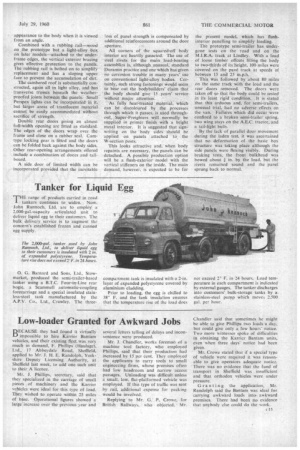
If you've noticed an error in this article please click here to report it so we can fix it.
WHAT is thought to be the first allBritish integrally constructed semitrailer van, using only light-alloy members in its construction, has been produced by the Duramin Engineering Co., Ltd., Stonefield Way, Ruislip, Middx.
The major advantage of this method of construction, in which the van sides and roof act as load-carrying members, is that a marked reduction in weight can be achieved compared with vans based on a separate semi-trailer chassis. With the Duramin design, this could be up to 1 ton for maximum-load vans.
The first example of the new SuperFreighter range, as it is to be known, is a 10-12-ton single-axled design. . This semi-trailer is 26 ft. long and weighs 2 tons 13 cwt. unladen, but complete with all running gear which is manufactured by Cranes (Dereharn), Ltd. It costs approximately £1,750.
Specified Running Gear
.Duramin do not intend to enter the semi-trailer field as manufacturers, but will market their integral body with any make of running gear specified by the customer. Purchase of the complete semi-trailer will be from the bodybuilders who will fit the axles, landing gear, upper coupling and any other ancillary equipment required.
Super-Freighters will be available in lengths from 22-28 ft., interior heights from 6 ft. 6 in.-9 ft., and in overall widths of 7 ft. 6 in. and 8 fr. To suit the running gear specified, the vans are offered with capacities of 10-12 tons, 14-15 tons, and 16-17 tons. Construction is similar for all types, but heavier-gauge panelling and other modifications to spit the increased loading are incorporated in the heavier versions.
When production is established, insulated and refrigerated models will be available, whilst special pallet-loading types and designs for bulk granular and powdered loads are planned.
The use of light alloy only in the fabrication of the integral assembly simplifies stressing problems. It is possible to make all joints in the structure extremely rigid, the necessary slight degree of flexibility being -provided by flexing of the light-alloy members.
• The underframe is made, up of closely spaced chain-lel-section transverse members—at 1-ft: 6-in. centres on the 10-12-ton design—riveted at 'their ends to longitudinal members of similar section. Most of the transverse channels are 5 in. deep with 2-in. flanges in thick material, but the four meinbers to which the sub-frame fu'r the tear suspension is attached are 8 in. deep with-in.
thick thick flanges. .
To avoid any " lozenging" effect under acceleration and braking stresses, the suspension mounting is braced diagonally, and similar reinforcement is provided for the coupling and landing gear attachment points. • The flooring, which may be deal, hardwood or extruded duralumin planking, is mounted directly on the cro*.members and clipped into position to avoid drilling and thereby weakening the suppcirts.
The flat panels of the body sides are attached directly to the longitudinal channels at each side of the underframe, and riveted at the top to the robust roof cant-rails. Thus, the complete side assembly can be considered as a girder with the longitudinal members acting as flanges and the stiffened panelling forming the webs.
Bracing for the side paneIs is provided by external W-section vertical extrusions spaced (on the lightest van offered) at about 1-ft. 10-in. centres. This section is particularly suitable as the rivet heads are enclosed within the channel, whilst the bevels of the W form give a clean appearance to the body when it is viewed from an angle.
Combined with a rubbing rail—wood on the prototype but a light-alloy box on later models—attached to the underframe edges, the vertical exterior bracing gives effective protection to the panels. The rubbing rail is bolted on to simplify replacement and has a sloping upper face to prevent the accumulation of dirt.
The cambered roof is substantially constructed, again all in light alloy, and has transverse trusses beneath the weatherproofed joints between the panels. Small Perspex lights can be incorporated in it, but larger areas of translucent material cannot be easily accommodated without sacrifice of strength.
Double rear doors giving an almost full-width opening arc fitted as standard. The edges of the doors wrap over the frame and close on a rubber seal. Camtype locking gear is fitted and the doors can he folded back against the body sides. Other rear-opening arrangements offered include a combination of doors and tailboard.
A side door of limited width can be incorporated provided that the inevitable loss of panel strength is compensated by additional reinforcements around the door aperture.
All corners of the squared-off body interior arc heavily gusseted. The use of steel rivets for the main load-bearing assemblies is, although unusual, standard Duramin practice and one which has-given no corrosion trouble in many years' use on conventional light-alloy bodies. Certainly, such strong fastenings would seem to bear out the bodybuilders' claim that the body should give 15 years' service without major attention.
As fully heat-treated material, which can be discoloured by the processes through which it passes, is used throughout, Super-Freighters will normally be supplied in primer finish with a bright metal interior. It is suggested that signwriting on the body sides should be applied on panels attached to_ the W-section posts.
This looks attractive and. when body repaints are necessary, the panels can be detached. A possible production option will be a flush-exterior model with the vertical stiffeners on the inside. The main demand, however, is expected to be for the present model, which has flushinterior panelling to simplify loading.
The prototype semi-trailer has undergone tests on the road and on the M.I.R.A. track at Lindley. With a load of loose timber offcuts filling the body to two-thirds of its height, 100 miles were covered on the pave track at speeds of between 15 and 25 m.p.h.
This was followed by about 80 miles On the same track with the load and the rear doors removed. The doors were taken off so that the body could be tested in its least rigid condition. It is stated that this arduous and, for semi-trailers, unusual trial, had no adverse effects on the van. Failures which did occur were confined to a broken semi-trailer spring, two wing stays on the A.E.C. tractor, and a tail-light bulb.
By the lack of parallel door movement during the laden test, it was ascertained that no deformation of the basic box structure was taking place although the side panels were flexing visibly. During braking tests, the front bulkhead was bowed about in. by the load, but the rivets remained sound and the panel sprung back to normal.