BODYBUILDING p
Page 42
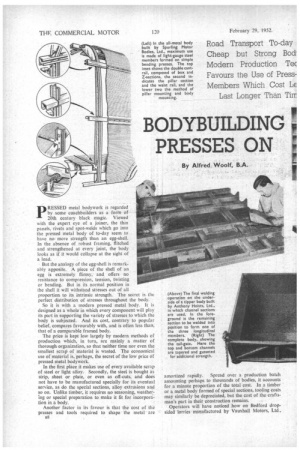
Page 43
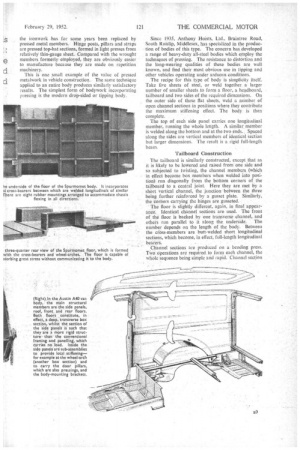
Page 44
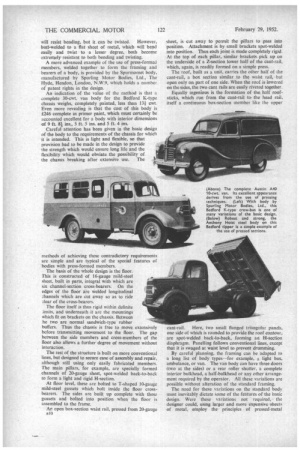
Page 45
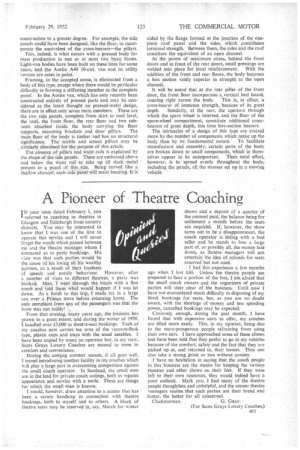
If you've noticed an error in this article please click here to report it so we can fix it.
PRESSES ON
By Alfred Woolf, B.A.
pRESSED metal bodywork is regarded by some coachbuilders as a form of 20th century black magic. Viewed with the expert eye of a joiner, the thin panels, rivets and spot-welds which go into the pressed metal body of to-day seem to have no more strength than an egg-shell. In the absence of robust framing, flitched and strengthened at every joint, the body looks as if it would collapse at the sight of a load.
But the analogy of the egg-shell is remarkably apposite. A piece of the shell of an egg is extremely flimsy, and offers no resistance to compression, tension, twisting or bending. But in its normal position in the shell it will withstand stresses out of all . proportion to its intrinsic strength. The secret is the perfect distribution of stresses throughout the body: So it is with a modern pressed metal body. It is designed as a whole in which every component will play its part in supporting the variety of stresses to which the body is subjected. And its cost, contrary to popular belief, compares favourably with, and is often less than, that of a comparable framed body.
The price is kept low largely by modern methods of production which, in turn, are mainly a matter of thorough organization, so that neither time nor even the smallest scrap of material is wasted. The economical use of material is, perhaps, the secret of the low price of pressed metal bodywork. .
In the first place it makes use of every available scrap of steel or light alloy. Secondly, the steel is bought as strip, sheet or plate, or even as off-cuts, and does not have to be manufactured specially for its eventual service, as do the special sections, alloy extrusions and so on. Unlike timber, it requires no seasoning, weathering or special preparation to make it fit for incorporation in a body. .
Another factor in its favour is that the cost of the presses and tools required to shape• the metal. are B8
amortized rapidly. Spread over a production batch amounting perhaps to thousands of bodies, it accounts for a minute proportion of the total cost. In a timber or a metal body formed of special sections, tooling costs may similarly be depreciated, but the cost of the craftsman's part in their construction remains. Operators will have noticed .how on Bedford dropsided lorries manufactured by Vauxhall Motors, Ltd.,
the .ironwork has for some years been replaced by pressed metal members. Hinge posts, pillars and straps are pressed top-hat sections, formed in light presses from relatively thin-gauge sheet. Compared with the wrought members formerly eMployed, they are obviously easier to manufacture because they are made on repetition machinery.
This is one small example of the value of pressed metalwork in vehicle construction.. The same technique applied to an entire body produces similarly satisfactory • results. The simplest form of bodywork incorporating pressing is the modern drop-sided or tipping body.
Since 1935, Anthony Hoists, Ltd., Braintree Road, South Ruislip, Middlesex,. has specialized in the production of bodies of this type. • The concern has .developed a range of heavy-duty all-steel bodies which employ the techniques of pressing. The resistance to distortion And the long-wearing qualities of these bodies are well known, and find their most obvious use in tipping and .other vehicles operating under arduous conditions.
The recipe for this. type of body is simplicity itself. Take five sheets of steel, or weld together a larger number of smaller sheets .to form a floor, a headboard, tailboard and two sides of the required dimensions. On the outer side of these flat sheets, weld a number of open channel sections in positions where they contribute the maximum, stiffening effect. The body is then complete.
The top of each side panel carries one longitudinal member, running the whole length. A similarmember is welded along the bottom and at the two ends.; Spaced along the sides are vertical members of identical Section but larger dimensions. The result is a rigid full-length beam.
Tailboard Construction The tailboard is similarly constructed, except that as it is likely to be lowered and raised from one side and so subjected to twisting, the channel members (which in effect become box members when welded into position) run diagonally from the bottom corners of the tailboard to a central joint. Here they are met by .a short vertical channel, the junction between the three being further reinforced by a gusset plate. Similarly, the corners carrying the hinges are gusseted.
The floor is slightly different, again, in final appearance. Identical channel sections are used The front of the floor is backed by one transverse channel, and others run parallel to it along the underside. The number depends on the length of the body. Between the cross members are butt welded short longitudinal sections, which become, in effect, full-length longitudinal bearers.
channel sections are produced on a bending press. Twia Operations are required to form each channel, the whole sequence being simple and rapid. Channel section will resist bending, but it. can be twisted. However,
butt-welded to a flat sheet of metal, which will bend easily and twist to a lesser degree, both become extremely-resistant to both bending and twisting.
A more advanced example of the use of press-formed members, welded together to form the framing and bearers of a body, is provided by the Spurrnomet body, manufactured by Spurting Motor Bodies, Ltd., The Hyde, Hendon, London, N.W.9, which holds a number of patent rights in the design.
An indication of the value of the method is that a complete 30-cwt. van body for the Bedford K-type chassis weighs, completely painted, less than 13-i. cwt. Even more revealing is that the cost of this body is £246 complete tn primer paint, which must certainly be accounted excellent for a body with interior dimensions of 9 ft 81 ins., 5 ft. 5 ins. and 5 ft. 4 ins. Careful attention has been given in the basic design of the body to the requirements of the chassis for which it is intended. This is light and flexible, so that provision had to be made in the design to provide the strength which would ensure long life and the flexibility which would obviate, the possibility of the chassis breaking after extensive use. The methods of achieving these contradictory requirements are simple and are typical of the special features of bodies with press-formed members.
The basis of the whole design is the floor. This is constructed of 16-gauge mild-steel sheet, built in parts, integral with which are six channel-section cross-bearers. On the edges of the floor are Welded longitudinal hannels which are cut away so as to ride clear of the cross-bearers.
The floor itself is thus rigid within definite .imits, and underneath -it are the mountings which fit on brackets on the chassis. Between he two are normal sandwich-type rubber buffers. Thus the chassis is free to move extensively before transmitting movement to the floor. The gap between the side members and cross-members of the floor also allows a further degree of movement without interaction.
The rest of the structure is built on more conventional lines, but designed to secure ease of assembly and repair, although still using only easily fabricated members. The main pillars, for example, are specially formed channels of 20-gauge sheet, spot-welded back-to-back to form a light and rigid H-section.
At floor level, these are bolted to T-shaped 10-gauge mild-steel gussets which bolt inside the floor crossbearers. The sides are built up complete with these gussets and bolted into position when the floor is assembled to the frame.
-An open box-section waist rail, pressed from 20-gauge elb
sheet, is cut away to permit the pillars to pass into position. Attachment is by small brackets spot-welded into position. Thus each joint is made completely rigid. At the top of each pillar, similar brackets .pick up on the underside of a Z-section lower halt of the cant-rail, which, again, is readily formed on a simple press.
The roof, built as a unit, carries the other half of the cant-rail, a box section similar to the waist rail, but open only on part of one side. When the roof is lowered on the sides, the two cant rails are easily riveted together.
Equally ingenious is the formation of the half roofsticks, which run from the cant-rail tothe head rail, itself a continuous box-section member like the upper cant-rail. Here, two small flanged triangular panels, one side of which is rounded to provide the roof contour, are spot-welded back-to-back, forming an H-section diaphragm. Panelling follows conventional lines, except that it is swaged at waist level to prevent drumming.
By careful planning, the framing can be adapted to a long list of body types---for example, a light bus, ambulance, or van. The van body can have three doors (two at the sides) or a rear roller shutter, a complete interior bulkhead, a half-bulkhead or any other arrangement required by the operator. All these variations are possible without alteration of the standard framing.
The need for these variations on the standard body must inevitably dictate some of the features of the basic design. Were these variations not required: the designer could; Using larger and more 'expensive -sheets of metal, employ the principles of pressed-metal construction to a greater degree. • For example, the side panels could have been designed, like the floor, to incorporate the equivalent of the cross-bearers—the pillars.
This, indeed, is what occurs with a pressed body for mass production in one or at most two basic forms. Light-van bodies have been built on these lines for some years, and the Austin A40 10-cwt. van and its utility version are cases in point.
Framing, in the accepted sense, is eliminated from a body of this type, except where there would be particular difficulty in forming a stiffening member in the complete panel. In the Austin van, which has only recently been constructed entirely of pressed parts and may be considered as the latest thought on pressed-metal design, there are in effect only seven main members. These are the two side panels, complete from skirt_to roof level, the roof, the front floor, the rear floor 'and two subunifs .attaChed inside the body carrying the floor supports, mounting brackets and door pillars. The Main floor of the body is timber and 'has no structural signifioance. The scuttle and screen pillars may be similarly dismissed for the purpose of this article.
The absence of pillars and waist rails is explained by. the shape of the side panels These are embossed above and below the Waist rail to take up all slack metal present in a panel of this siie. Being curved like a shallow channel, each side panel will resist bending, It is aided by the flange formed at the junction of the onepiece roof panel and the sides, which contributes torsional strength. Between them, the sides and the roof constitute the equivalent of an open channel.
At the points of maximum stress, behind the front doors and in front of the rear doors, small pressings are welded into place for local reinforcement. With the addition of the front and rear floors, the body becomes a box section vastly superior in strength to the open channel.
It will be noted that at the rear pillar of the front door, the front floor incorporates a.vertical heel board, running right across the body. This is, in effect, a cross-bearer of immense strength, because of its great depth. Similarly, at the rear, the aperture through which the spare wheel is inserted, and the floor of the spare-wheel compartment, constitute additional crossbearers of great depth, this time box-section bearers.
The intricacies of a design of this type are created more by the number of components which make up the body, than by its fundamental nature. To facilitate manufacture and assembly, certain parts of the body are broken down to small components, which in them selves appear to be unimportant. Their total effect, however, is to spread evenly throughout the body, including the panels, all the stresses set up in a moving vehicle.