Pickling and Priming Iron Components
Page 49
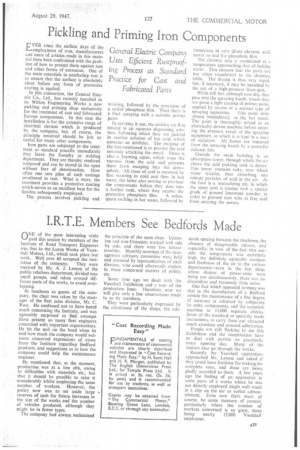
If you've noticed an error in this article please click here to report it so we can fix it.
VER since the earliest days of the employntent of iron, manufacturers and users of articles,made in this material have been confronted with the problem of how to protect them against rust and other forms of corrosion. One of the main essentials in combating rust is to ensure that the surface is absolutely clean before any form of protective coating is applied.
In this connection, the General Electric Co., Ltd., has recently installed in its Witton Engineering Works a new pickling and priming shop exclusively for the treatment of cast and fabricated ferrous components. in this case the installation is for the extensive range of electrical devices which is produced by the company, but, of course, the principle involved should be just as useful for many other components.
Iron parts are subjected to the treatment as standard practite immediately they leave the foundry or welding department. They are thereby rendered rustproof and can be stored in the open without fear of deterioration. How often one sees piles of such castings smothered in rust. What is more, the treatment provides a protective coating which serves as an excellent base for the finishes subsequently employed.
The process involves pickling and washing, .followed by the provision of a sealed phosphate film. Then there is a final spraying with a suitable primer paint.
In carrying it out, the articles are first treated in an aqueous degreasing solution, following which they are pickled in another solution of hot acid, which contains an inhibiter. The purpose of the last-mentioned is to prevent the acid seriously attacking the metal. There is also a foaming agent, which traps the 'vapours from the acid and prevents them from escaping into the atmosphere. All trace of acid is removed by first washing in cold and then in hot water, the latter also serving to pre-heat. the components before they pass into a further tank, where they receive the
protective phosphate film. A subseqiaent swilling in hot water, followed by
immersion in very dilute chromic acid. serves to seal the phosphate film.
The chromic acts.; is maintained at a temperature approaching that of boiling water. This ensures that the parts are hot when transferred to the draining table. The drying is thus very rapid. but, if necessary, it may be hastened by the use of a high-pressure blow-gun.
While still hot. although now dry, they pass into the spraying booth, where they are given a light coating of primer paint. applied by means of a normal type of spraying apparatus. This paint dries almost immediately on the hot metal. The paint is thoroughly mixed in an electrically driven machine before entering the pressure vessel or the spraying equipment, ia which ii is kept in a state of agitation. All fumes are removed from the spraying booth by a powerful exhaust fan
Outside the main building is an absorption tower, through which the air above the acid pickling tank is drawn. This tower contains coke, over which water trickles, thus absorbing any minute particles of acid in the air. At the foot is a neutralizing pit, in which the spent acid is treated with a special grade of ground limestone powder, in order to prevent iron salts or free acid from entering the sewers.