A RIVETING TALE
Page 38
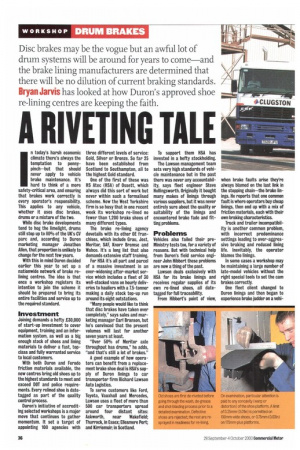
Page 39
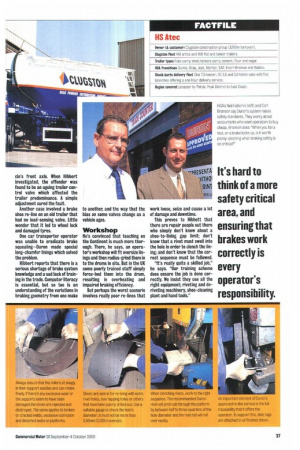
If you've noticed an error in this article please click here to report it so we can fix it.
Disc brakes may be the vogue but an awful lot of drum systems will be around for years to come—and the brake lining manufacturers are determined that there will be no dilution of current braking standards. Bryan Jarvis has looked at how Duron's approved shoe re-lining centres are keeping the faith.
In today's harsh economic climate there's always the temptation to pennypinch—but that should never apply to vehicle brake maintenance. Its hard to think of a more safety-critical area, and ensuring that brakes work correctly is every operator's responsibility. This applies to any vehicle, whether it uses disc brakes, drums or a mixture of the two.
While disc brake developments tend to hog the limelight, drums still stop up to BO% of the UK's CV parc and, according to Duren marketing manager Jonathon Allen, that proportion is unlikely to change for the next few years.
With this in mind Duron decided earlier this year to set up a nationwide network of brake relining centres. The idea is that once a workshop registers its intention to join the scheme it should be prepared to bring its entire facilities and service up to the required standard.
Investment
Joining demands a hefty £30,000 of start-up investment to cover equipment, training and an information system, as well as a big enough stock of shoes and lining materials to deliver a fast, topclass and fully warranted service to local customers.
With both Duron and Ferodo friction materials available, the new centres bring old shoes up to the highest standards to meet and exceed DOT and police requirements. Every relined shoe is datetagged as part of the quality control process.
Duron's initiative of accrediting selected workshops is a major move that continues to gather momentum. It set a target of appointing 100 agencies with three different levels of service: Gold, Silver or Bronze. So far 25 have been established from Scotland to Southampton, all to the highest Gold standard.
One of the first of these was HS Atec (HSA) of Ossett. which always did this sort of work but never within such a formalised scheme. Now the West Yorkshire firm is so busy that in one recent week its workshop re-lined no fewer than 1,200 brake shoes of many different types.
The brake re-lining agency dovetails with its other OE franchises, which include Grau, Jost, Mentor, SAF, Knorr Bremse and Wabco. It's a long list that also demands extensive staff training.
For HSA it's all part and parcel of a massive investment in an ever-widening after-market service which includes a fleet of 30 well-stocked vans on hourly deliveries to hauliers with a 7.5-tonner making a daily stock top-up run around its eight outstations.
"Many people would like to think that disc brakes have taken over completely," says sales and marketing manager Carl Branson, but he's convinced that the present volumes will last for another seven years at least.
"Over 50% of Mentor axle throughput has drums," he adds, "and that's still a lot of brakes."
A good example of how operators can benefit from a replacement brake shoe deal is HSA's supply of Duron linings to car transporter firm Richard Lawson Auto Logistics.
To serve customers like Ford, Toyota, Vauxhall and Mercedes, Lawson uses a fleet of more than 500 car transporters spread around four distant sites: Ackworth, near Wakefield; Thurrock, in Essex; Ellesmere Port; and Kirriemuir, in Scotland. To support them NSA has invested in a hefty stockholding.
The Lawson management team sets very high standards of vehicle maintenance but in the past there was never any accountability, says fleet engineer Steve Hollingsworth. Originally it bought many makes of linings through various suppliers, but it was never entirely sure about the quality or suitability of the linings and encountered brake fade and fitting problems.
Problems
Vehicles also failed their preMinistry tests too, for a variety of reasons. But with technical help from Duron's field service engineer John Hibbert these problems are now a thing of the past.
Lawson deals exclusively with HSA for its brake linings and receives regular supplies of its own re-lined shoes. all datetagged for full traceability.
From Hibbert's point of view, when brake faults arise they're always blamed on the last link in the stopping chain—the brake linings. He reports that one common fault is where operators buy cheap linings, then end up with a mix of friction materials, each with their own braking characteristics.
Truck and trailer incompatibility is another common problem, with incorrect predominance settings leading to over-aggressive braking and reduced lining life. Inevitably, the operator blames the linings.
In some cases a workshop may be maintaining a large number of late-model vehicles without the right special tools to set the cam brakes correctly.
One fleet client changed to Duran linings and then began to experience brake judder on a vehi de's front axle. When Hibbert investigated, the offender was found to be an ageing trailer control valve which affected the trailer predominance. A simple adjustment cured the fault.
Another case involved a brake shoe re-line on an old trailer that had no load-sensing valve. Little wonder that it led to wheel lock and damaged tyres.
One car transporter operator was unable to eradicate brake squealing—Duron made special long-chamfer linings which solved the problem.
Hibbert reports that there is a serious shortage of brake system knowledge and a sad lack of training in the trade. Computer literacy is essential, but so too is an understanding of the variations in braking geometry from one make to another, and the way that the bias on some valves change as a vehicle ages.
Workshop
He's convinced that teaching on the Continent is much more thorough. There, he says, an operator's workshop will fit oversize linings and then radius-grind them in to the drums in situ. But in the UK some poorly trained staff simply force-bed them into the drum, resulting in overheating and impaired braking efficiency.
But perhaps the worst scenario involves really poor re-lines that work loose, seize and cause a lot of damage and downtime.
This proves to Hibbett that there are repair people out there who simply don't know about a shoe-to-lining gap limit; don't knew that a rivet must swell into the hole in order to clench the lining; and don't know that the correct sequence must be followed.
"It's really quite a skilled job," he says. "Our training scheme does ensure the job is done correctly. We insist they use all the right equipment; riveting and deriveting machinery, shoe-cleaning plant and hand tools."