Selling the
Page 27
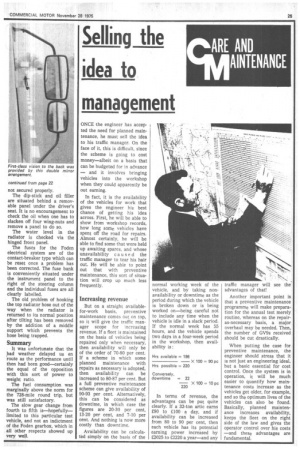
If you've noticed an error in this article please click here to report it so we can fix it.
idea to management
ONCE the engineer has accep ted the need for planned maintenance, he must sell the idea to his traffic manager. On the face of it, this is difficult, since the scheme is going to cost money—albeit on a basis that can be budgeted for in advance — and it involves bringing vehicles into the workshop when they could apparently be out earning.
In fact, it is the availability of the vehicles for work that gives the engineer his best chance of getting his idea across. First, he will be able to show from workshop records, how long some vehicles have spent off the road for repairs. Almost certainly, he will be able to find some that were held up awaiting spares, and whose unavailability caused the traffic manager to tear his hair out. He will be able to point out that with preventive maintenance, this sort of situation will crop up much less frequently.
Increasing revenue
But on a straight availablefor-work basis, preventive maintenance comes out on top, so it will give the traffic manager scope for increasing revenue. If a fleet is maintained on the basis of vehicles being repaired only when necessary, then availability will only be of the order of 70-80 per cent. If a scheme in which some planned maintenance with repairs as necessary is adopted, then availability can be increased to 80-87 per cent. But a full preventive maintenance scheme can give availability of 90-93 per cent. Alternatively, this can be considered as downtime, in which case the figures are 20-30 per cent, 13-20 per cent, and 7-10 per cent. And nothing is now more costly than downtime.
Availability can be calculated simply on the basis of the normal working week of the vehicle, and by taking nonavailability or downtime as the period during which the vehicle is broken down or is being worked on—being careful not to include any time when the vehicle is idle in a slack period. If the normal week has 55 hours, and the vehicle spends two days in a four-week period in the workshop, then availability is :
Firs available = 198 X 100 = 90 pc Firs possible = 220 Conversely.
downtime = 22
— X 100 = 10 pc
220
In terms of revenue, the advantages can be put quite clearly. If a 32-ton artic earns £90 to £100 a day, and if availability can be increased from 80 to 90 per cent, then each vehicle has its potential earning power increased by £2025 to £2220 a year—and any traffic manager will see the advantages of that!
Another important point is that a preventive maintenance programme will make preparation for the annual test merely routine, whereas on the repairas-necessary basis, a major overhaul may be needed. Then, the number of GV9s received should be cut drastically.
When putting the case for preventive maintenance, the engineer should stress that it is not just an engineering ideal, but a basic essential for cost control. Once the system is in operation, it will be much easier to quantify how maintenance costs increase as the vehicles get older, for example, and so the optimum lives of the vehicles can also be found. Basically, planned maintenance increases availability, keeps the fleet on the right side of the law and gives the operator control over his costs —and these advantages are fundamental.