Transport and the environment is the theme for this year's
Page 73
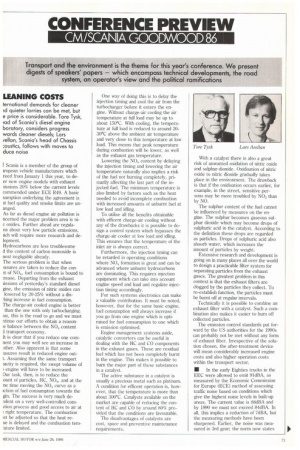
Page 74
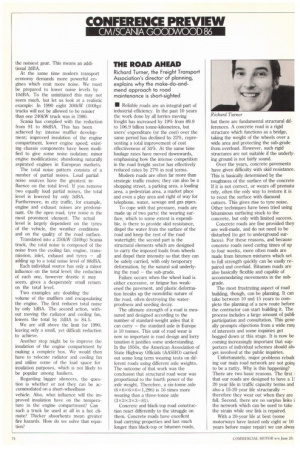
If you've noticed an error in this article please click here to report it so we can fix it.
conference. We present digests of speakers' papers — which encompass technical developments, the road system, an operator's view and the political ramifications
LEANING COSTS
ternational demands for cleaner id quieter lorries can be met, but
e price is considerable. Tore Tysk, !ad of Scania's diesel engine boratory, considers progress wards cleaner diesels; Lars rellan, Scania's head of Chassis :oustics, follows with moves to duce noise I Scania is a member of the group of iropean vehicle manufacturers which reed from January 1 this year, to deer new engine models with exhaust 'fissions 20% below the current levels commended under ECE R49. A basic sumption underlying the agreement is it fuel quality and smoke limits are unanged.
As far as diesel engine air pollution is ncemed the major problem area is ni c oxides. Further ahead are regulans about very low particle emissions, Lich will require more research and delopment.
Hydrocarbons are less troublesome d the content of carbon monoxide is nost negligable already.
The serious problem is that when ?.asures are taken to reduce the conIt of NOR, fuel consumption is bound to rease. Departing from the exhaust iissions of yesterday's standard diesel gine, the emission of nitric oxides can
lowered by 20-25% without a dis-bing increase in fuel consumption. The charge-air cooled engine is better than the one with only turbocharging. US, this is the road to go and we must ntinue our efforts to obtain a reasonle balance between the NO content I transport economy.
It is clear that if you reduce one cornnent you may well see an increase in )ther. Also apparent is that some !asures result in reduced engine outt. Assuming that the same transport mcity is required, the swept volume of
engine will have to be increased. Our task, then, is to reduce the Lount of particles, HC, NON, and at the ne time moving the NO curve as a lotion of fuel consumption towards the gin. The success is very much de
dent on a very well-controlled com3tion process and good access to air at right temperature. The combustion ist be adjusted so that the heat rese is delayed and the combustion temmture limited. One way of doing this is to delay the injection timing and cool the air from the turbocharger before it enters the engine. Without charge-air cooling the air temperature at full load may be up to about 150°C. With cooling, the temperature at full load is reduced to around 2030°C above the ambient air temperature and very close to this temperature at low load. This means that peak temperature during combustion will be lower, as well as the exhaust gas temperature.
Lowering the NO content by delaying the injection timing and lowering the air temperature naturally also implies a risk of the fuel not burning completely, primarily affecting the last part of the injected fuel. The minimum temperature is also limited by factors such as the heat needed to avoid incomplete combustion with increased amounts of unbumt fuel at low load and idling.
To utilise all the benefits obtainable with efficent charge-air cooling without any of the drawbacks it is possible to design a control system which bypasses the charge-air cooler at low load and idling. This ensures that the temperature of the inlet air is always correct.
Furthermore, the injection timing can be retarded in operating conditions where NO formation is great and can be advanced where unbumt hydrocarbons are dominating. This requires injection equipment which can take into account engine speed and load and regulate injection timing accordingly.
For such systems electronics can make a valuable contribution. It must be noted, however, that for the same basic engine, fuel consumption will always increase if you go from one engine which is optimised for fuel consumption to one which is emission optimised.
Engine management systems aside, catalytic converters can be useful in dealing with the HC and CO components in the exhaust gases. These are residual fuel which has not been completely burnt in the engine. This makes it possible to burn the major part of these substances in a catalyst.
The active substance in a catalyst is usually a precious metal such as platinum. A condition for efficent operation is, however, that the temperature is more than about 300°C. Catalysts available on the market are capable of reducing the content of 1-IC and CO by around 80% provided that the conditions are favourable.
The disadvantages of catalysts are cost, space and preventive maintenance requirements. With a catalyst there is also a great risk of unwanted oxidation of nitric oxide and sulphur-dioxide. Oxidisation of nitric oxide to nitric dioxide gradually takes place in the environment. The drawback is that if the oxidisation occurs earlier, for example, in the street, sensitive persons may be more troubled by NO2 than by NO.
The sulphur content of the fuel cannot be influenced by measures on the engine. The sulphur becomes gaseous sulphur dioxide which may become drops of sulphuric acid in the catalyst. According to the definition these drops are regarded as particles. Drops of sulphuric acid also absorb water, which increases the amount of particles by weight.
Extensive research and development is going on in many places all over the world to design a practicable filter system for separating particles from the exhaust gases. The greatest problem in this context is that the exhaust filters are clogged by the particles they collect. To re-establish function, the particles must be burnt off at regular intervals.
Technically it is possible to combine an exhaust filter with a catalyst. Such a combination also makes it easier to burn off collected particles.
The emission control standards put forward by the US authorities for the 1990s can probably not be met without any form of exhaust filter. Irrespective of the solution chosen, the after-treatment device will mean considerably increased engine costs and also higher operation costs within the transport sector.
• In the early Eighties trucks in the EEC were allowed to emit 91dBA, as measured by the Economic Commission for Europe (ECE) method of assessing traffic noise based on conditions which give the highest noise levels in built-up areas. The current value is 88dBA and by 1990 we must not exceed 84dliA. In all, this implies a reduction of 7dBA, but the measuring methods have been sharpened. Earlier, the noise was measured in 3rd gear; the norm now states
the noisiest gear. This means an additional 2dBA.
At the same time modern transport economy demands more powerful engines which emit more noise. We must be prepared to lower noise levels by 10dFiA. To the uninitiated this may not seem much, but let us look at a realistic example: In 1990 eight 300kW (400hp) trucks will not be allowed to be noisier than one 240kW truck was in 1980.
Scania has complied with the reduction from 91 to 88dBA. This has been achieved by: intense muffler development; improved insulation of the engine compartment, lower engine speed; existing chassis components have been modified to give some noise isolation; minor engine modifications; abandoning naturally aspirated engines in European markets.
The total noise pattern consists of a number of partial noises. Loud partial noise sources have the greatest influence on the total level. If you remove two equally loud partial noises, the total level is lowered by only 3dBA. Furthermore, in city traffic, for example, engine and exhaust noises are predominant. On the open road, tyre noise is the most prominent element. The actual level is largely dependent on the tyres of the vehicle, the weather conditions and on the quality of the road surface.
Translated into a 250kW (340hp) Scania truck, the total noise is composed of the noise from the cooling fan, engine, transmission, inlet, exhaust and tyres — all adding up to a total noise level of 88dBA.
Each individual source has only a minor influence on the total level; the reduction of each one, however drastic it may seem, gives a desperately small return on the total level.
Two examples are doubling the volume of the mufflers and encapsulating the engine. The first reduces total noise by only ldBA. The second action, without moving the radiator and cooling fan, lowers the total by 2dBA to 84.5.
We are still above the limit for 1990, leaving only a small, yet difficult reduction to achieve.
Another step might be to improve the insulation of the engine compartment by making a complete box. We would then have to relocate radiator and cooling fan and utilise some of the load space for insulation purposes, which is not likely to be popular among hauliers.
Regarding bigger silencers, the question is whether or not they can be accommodated on a short-wheelbase vehicle. Also, what influence will the improved insulation have on the temperature in the engine compartment? Can such a truck be used at all in a hot climate? Thicker absorbents mean greater fire hazards. How do we solve that equation?