Planning for Profit
Page 68
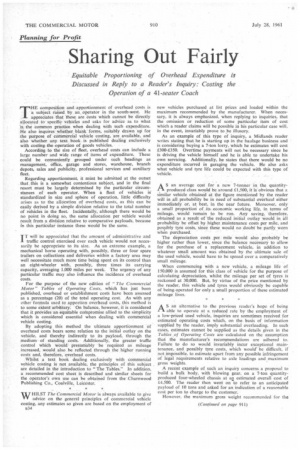
Page 71
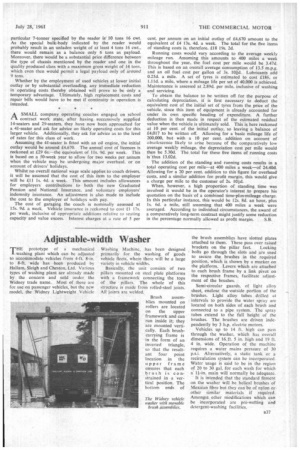
If you've noticed an error in this article please click here to report it so we can fix it.
Sharing Out Fairly
Equitable Proportioning of Overhead Expenditure is Discussed in Reply to a Reader's Inquiry: Costing the Operation of a 41-seater Coach
THE composition and:apportionment of overhead costs is a subject raged by. an, operator in the south-west. He appreciates that these are costs which cannot be directly allocated to specific vehicles and asks for advice as to what is. the common practice when dealing with such expenditure. He also inquires whether blank forms, suitably drawn up for the purpose of commercial vehicle costing, are available, and also whether any text book is published dealing exclusively with costing-the operation of goods vehicles.
According to the size of fleet, overhead costs can include a large number and wide range of items of expenditure. These could be conveniently grouped under such headings as management, office, garage and stores, warehouse, branch depots, sales and publicity, professional services and auxiliary fleet.
Regarding apportionment, it must be admitted at the outset that this is a somewhat contentious subject, and in the final resort must be largely determined by the particular circumstances of each operator. When a fleet of vehicles iS standardized in size and sphere of operation, little difficulty arises as to the allocation of overhead costs, as this can be easily derived by a simple division relative to the total number of vehicles in the fleet. Incidentally, although there would be no point in doing so, the same allocation per vehicle would result from a division relative to comparative payloads, because in this particular -instance these would be the same.
T T will be appreciated that the amount of administrative and 1 traffic control exercised over each vehicle would not necessarily be appropriate to its size. As an extreme example, a mechanical horse operating with, possibly, three or four spare trailers on collections and deliveries within a factory area may well necessitate much more time being spent on its control than an eight-wheeler with, possibly, three times its carrying capacity, averaging 1,000 miles per week. The urgency of any particular traffic may also influence the incidence of overhead costs.
For the purpose of the new edition of "The Commercial Motor" Tables of Operating Costs, which has just been published, overhead or establishment costs have been assessed as a percentage (20) of the total operating cost. As with any other formula used to apportion overhead costs, this method is to some extent arbitrary. On balance, however, it is considered that it provides an equitable compromise allied to the simplicity which is considered essential when dealing with commercial vehicle costing.
By adopting this method the ultimate apportionment of overhead costs bears some relation to the initial outlay on the vehicle, and thereby indirectly to its payload, through the medium of standing costs. Additionally, the greater traffic control which would presumably be required as mileage increased, would also be reflected through the higher running costs and, therefore, overhead costs.
Whilst a text book dealing exclusively with commercial vehicle costing is not available, the principles of this subject are detailed in the introduction to "The Tables." In addition, a recommended cost sheet is described and similar sheets for the operator's own use can be obtained from the Charnwood Publishing Co., Coalville, Leicester.
WHILST The Commercial Motor is always available to give advice on the general principles of commercial vehicle costing, any estimates so given arc based on the employment of n34
new vehicles purchased at list prices and loaded within the maximum recommended by the manufacturer. When necessary, it is always emphasized, when replying to inquiries, that the omission or reduction of some particular item of cost which a reader claims will be possible in his particular case will. in the event, invariably prove to be illusory.
As an example of this type of inquiry, a Midlands reader writes stating that he is starting up in the haulage business and is considering buying a 7-ton lorry, which he estimates will cost £3004350. Overtime payments will not be necessary since he is driving the vehicle himself and he is able to undertake his own servicing. Additionally, he states that there would be no expenditure incurred in garaging the vehicle. He also asks what vehicle and tyre life could be expected with this type of vehicle. .
/A
A S an average oast for a new 7-tanner in the quantity produced class would be around £1,500, it is obvious that a similar vehicle obtained at the figure mentioned by the reader will in all probability be in need of substantial overhaul either immediately or, at best, in the near future. Moreover, only a small proportion of its economic working life, in terms of mileage, would remain to be run. Any saving. 'therefore, obtained as a result of the reduced initial outlay would in all probability be offset by higher, maintenance costs per mile, and possibly tyre costs, since these would no doubt be partly worn when purchased.
The depreciation costs .per mile would also probably be higher rather than lower, since the balance necessary to allow for the purchase of a replacement vehicle, in addition to whatever small amount was obtained by the ultimate sale of the used vehicle, would have to be spread over a comparatively small mileage.
When commencing with a new vehicle, a mileage life of 150,000 is assumed for this class of vehicle for the purpose of calculating depreciation, whilst the mileage per set of tyres is reckoned at 30,000. But, by virtue of the price mentioned by the reader, this vehicle and tyres would obviously be capable of being operated for only a small proportion of these estimated mileage lives.
AS an alternative to the previous reader's hopc of being able to operate at a reduced rate by the employment of a low-priced used vehicle, inquiries are sometimes received for estimated operating costs which, on the basis of information supplied by the reader, imply substantial overloading. ln such cases, estimates cannot be supplied as the details given in the Tables of Operating Costs are calculated on the assumption that the manufacturer's recommendations are adhered to. Failure to do so would invariably incur exceptional maintenance, and possibly tyre costs, which would' be difficult, if not impossible. to estimate apart from any possible infringement of legal requirements relative to axle loadings and maximum gross weights.
A recent example of such an inquiry concerns a proposal to build a bulk body, with blowing gear, on a 7-ton quantityproduced four-wheeled chassis at an estimated overall cost of £4.500. The reader then went on to refer to an anticipated payload of TO tons and asked for an indication of a reasonable cost per ton to charge to the customer.
However, the maximum gross weight recommended for the particular 7-tonner specified by the reader is 10 tons 16 cwt. As the special bulk-body indicated by the reader would probably result in an unladen weight of at least 4 tons 16 cwt., there would remain as a balance only 6 tons as payload. Moreover, there would be a substantial price difference between the type of chassis mentioned by the reader and one in the quality produced class with a maximum gross weight of 14 tons, which even then would permit a legal payload only of around 9 tons.
Whether by the employment of used vehicles at lower initial outlay or by substantial overloading, any immediate reduction in operating costs thereby obtained will prove to be only a temporary advantage. Ultimately, high replacement costs and repair bills would have to be met if continuity in operation is intended.
ASMALL company operating coaches engaged on school contract work state, after having successively supplied 14-seaters and 29-seaters, they have now been approached for a 41-seater and ask for advice on likely operating costs for this larger vehicle. Additionally. they ask for advice as to the level of rates for this class of work.
Assuming the 4I-seater is fitted with an oil engine, the initial outlay would be around £4.670. The annual cost of licences is reckoned at £29 6s.-4he equivalent of I Is. 9d. per week. This is based on a 50-week year to allow for two weeks per annum when the vehicle may be undergoing major overhaul, or on account of drivers' holidays.
Whilst no overall national wage scale applies to coach drivers, it will be assumed that the cost of this item to the employer will be £11 Is. 4d. a week. This amount includes allowances for employers' contributions to both the new Graduated Pension and National Insurance, and voluntary employers' indemnity insurance. An adjustment is also made to include the cost to the employer of holidays with pay.
The cost of garaging the coach is nominally assessed at 15s. 9d. a week. Vehicle insurance is reckoned to cost 1 17s. pei week, inclusive of appropriate additions relative to seating capacity and value excess. Interest charges at a rate of 5 per cent, per annum on an initial outlay of £4,670 amount to the equivalent of £4 13s. 4d. a week. The total for the five items of standing costs is, therefore, £18 19s. 2d.
Running costs would vary according to the average weekly mileage run. Assuming this amounts to 400 miles a week throughout the year, the fuel cost per mile would be 3.47d. This is based on an overall average consumption of 13.5 m.p.g. and an oil fuel cost per gallon of 3s. 101d. Lubricants add 0.25d. a mile. A set of tyres is estimated to cost £186, or 1.11d. a mile, where a mileage life per set of 40.000 is achieved. Maintenance is assessed at 2.89d. per mile, inclusive of washing and servicing.
To obtain the, balance to be written off for the purpose of calculating depreciation, It is first necessary to deduct the equivalent cost of the initial set of tyres from the price of the vehicle, since this item of equipment is already accounted for under its own specific heading of expenditure. A further deduction is then made in respect of the estimated residual value when the vehicle is ultimately sold. This is here reckoned at 10 per cent. of the initial outlay, so leaving a balance of £4,017 to be written off. Allowing for a basic mileage life of 200,000, but with a 10 per cent. addition on account of obsolescence likely to arise because of thc comparatively low average weekly mileage, the depreciation cost per mile would then be 5.30d. The total for these five items of running costs is thus 13.02d.
The addition of the standing and running costs results in a total operating cost per mile—at 400 miles a week—of 24.40d. Allowing for a 20 per cent. addition to this figure for overhead costs, and a similar addition for profit margin, this would give a charge per mile to the customer of 2s. 10d.
When, however, a high proportion of standing time was involved it would be in the operator's interest to prepare his quotation on the basis of a combined time-plus-mileage charge. In this particular instance, this would be 12s. 8d. an hour, plus 1s. fid. a mile, still assuming that 400 miles a week were averaged. According to individual circumstances, the award of a comparatively long-term contract might justify some reduction in the percentage normally allowed as profit margin. S.B.