THE HYDROGENATION OF BITUMINOUS COAL
Page 48
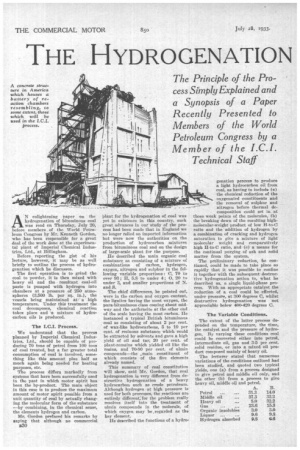
Page 49
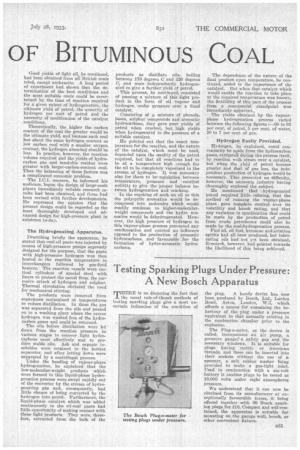
If you've noticed an error in this article please click here to report it so we can fix it.
The Principle of the Process Simply Explained and a Synopsis of a Paper Recently Presented to Members of the World Petroleum Congress by a Member of the I.C.I.
Technical Staff
AN enlightening paper on the hydrogenation of bituminous coal was read en Thursday, July 20, before members of the World Petroleum Congress by Mr. Kenneth Gordon, who has been responsible for a great deal of the work done at the experimental plant of Imperial Chemical Industries, Ltd., at Billing-ham.
Before reporting the gist of his lecture, however, it may be as well briefly to outline the process of hydrogenation which he discusses.
The first operation is to grind the coal to powder, it is then mixed with heavy oil and the resultant coal-oil paste is pumped with hydrogen into chambers at a pressure of 250 atmospheres (3,500 lb. per sq. in.), the vessels being maintained at a high temperature. Under this treatment the coal decomposes, chemical reaction takes place and a mixture of hydrocarbon oils is produced.
The I.C.I. Process. •
We understand that the process planned by Imperial Chemical Industries, Ltd., should be capable of producing 70 tons of petrol from 100 tons of coal treated, but a far greater total consumption of coal is involved, something like this amount plus half as much again being needed for heating purposes, etc.
The process differs markedly from systems that have been successfully used in the past in which motor spirit has been the by-product. The main object in this case is to produce the maximum amount of motor spirit possible from a unit quantity of coal by actually changing the molecular form of the substance —by combining, in the chemical sense, the elements hydrogen and carbon.
Mr. Gordon prefaced his remarks by saying that although no commercial B30 plant for the hydrogenation of coal was yet in existence in this country, such great advances in our study of the process had been made that in England we no longer relied on imported information but were now the authorities on the production of hydrocarbon mixtures from bituminous coal and on the design of large-scale plant for the purpose.
He described the main organic coal substance as consisting of a mixture of combinations of carbon, hydrogen, oxygen, nitrogen and sulphur in the following variable proportions: 0, 70 to over 93; H, 5.8 to under 4; 0, 20 to under 3, and smaller proportions of N. and S.
The chief differences, he pointed out, were in the carbon and oxygen content, the lignites having the most oxygen, the pars-bituminous class coming about midway and the anthracite at the other end of the scale having the most carbon. He instanced a typical British bituminous coal as consisting of about 2 per cent. of wax-like hydrocarbons, 5 to 10 per cent. of resinous substance which could be extracted by solvents and gave a high yield of Oil and tar, 20 per cent, of plant-remains which yielded oil like the resins, and 70-80 per cent, of ulmin compounds—the .,main constituent of which consists of the five elements already named.
This summary of coal constitution will show, said Mr. Gordon, that coal hydrogenation is very different from destructive hydrogenation of a heavy hydrocarbon such as crude petroleum. Although hydrogen at high pressure is used for both processes, the reactions are entirely different:for the problem really resolves itself into the treatment of ulmin compounds in the molecule, of which oxygen may be,regarded as the key element.
He described the functions of a hydro
genation process to produce a light hydrocarbon oil from coal, as having to include (a) the chemical reduction of the oxygenated constituents and the removal of sulphur and nitrogen before thermal de composition could set in at those weak points of the molecules, (b) the breaking down of the resulting highmolecular-weight product of low H-to-C ratio and the addition of hydrogen by a combination of cracking and hydrogen saturation to give a mixture of light molecular weight and comparatively high H-to-C ratio, and (c) a means for the continual purging of ash and solid matter from the system.
The preliminary reduction, he continued, could be made to take place so rapidly that it was possible to confine it together with the subsequent destructive hydrogenation action to, what he described as, a single liquid-phase process. With an appropriate catalyst the reduction of a coal could be effected, under pressure, at 300 degrees C, whilst destructive hydrogenation was not appreciable below 400420 degrees C.
The Variable Conditions.
The extent of the latter process depended on the temperature, the time, the catalyst and the pressure of hydrogen. By varying these conditions coal could be converted either into petrol, intermediate oil, gas and 3-5 per cent. solid residue, or into a mixed oil product composed mainly of heavy oiL The lecturer stated that numerous variations of the conditions outlined had been studied, and quoted two typical yields, one (a) from a process designed to give petrol and middle oil only, and the other (b) from a process to give heavy oil, middle oil and petrol. Good yields of light oil, be continued, had been obtained from all British coals tried, except anthracite. A long period of experiment had shown that the determination of the best conditions and the most suitable coals could be ascertained by the time of reaction required for a given extent of hydrogenation, the ultimate yield of petrol, the quantity of hydrogen per unit of petrol and the necessity of modification of the catalyst . conditions.
Theoretically, the higher the carbon content of the coal the greater would be the ultimate yield, and because such coal has about the same hydrogen content as low carbon coal with a smaller oxygen content, the hydrogen absorbed should be less. In practice, however, the reaction volume required and the yields of hydrocarbon gas and insoluble residue were greater with larger-carbon-content coal. Thus the balancing of these factors was a complicated economic problem.
The I.C.I. concern, he informed his audience, began the design of large-scale plants immediately reliable research results had been obtained, aad these had been revised with further developments. He expressed the opinion that the present design could be regarded as the most thoroughly developed and advanced design for high-pressure plant in existence to-day.
The Hydrogenating Apparatus.
Describing briefly the apparatus, he stated that coal-oil paste was injected by means of high-pressure pumps expressly designed for the purpose, that the paste with high-pressure hydrogen was then heated to the reaction temperature in interchangere followed by gas-fired heaters.. The -reaction vessels were vertical cylinders of special steel with liners to protect the metal from the corrosive attack of hydrogen and sulphur. Thermal circulation obviated the need for mechanical stirring.
The products were removed from separators maintained at temperatures to reduce distillation, In them the gas was separated from the oils and passed on to a washing plant where the excess hydrogen was washed free of the hydrocarbon gases and could be returned.
The oils before distillation were let • down from the reaction pressure in various stages to -recover light hydrocarbons most effectively and to prochic° stable oils. Ash and organic insolubles were retained in the hottest separator, and after letting down were separated by a centrifugal process.
Under the heading of vapour-phase hydrogenation, he explained that the low-molecular-weight products which were formed in this liquid-phase hydrogenation process were swept rapidly out of the converter by the stream of hydrogenating gas and, consequently, had little chance of being converted by the hydrogen into petrol. Furthermore, the liquid-phase catalyst which was added continuously to the oil-coal paste had little opportunity of making contact with these light products. They were, therefore, extracted from the bulk of the products as distillate oils, boiling between 170 degrees 0 and 320 degrees C, and were independently hydrogenated to give a further yield of petrol.
This process, he continued, consisted of passing a mixture of this aight product in the form of oil vapour and hydrogen under pressure over a fixed catalyst.
Consisting of a mixture of phenols, bases, sulphur compounds and aromatic hydrocarbons, they gave poor yields of petrol when cracked, but high yields when hydrogenated in the presence of a suitable catalyst.
He pointed out that the exact temperature for the reaction, and the nature of " the catalyst, which must be used, depended upon the quality of the petrol required, but that all -reactions had to be at a temperature high enough for the oil to be completely vaporized in the stream of hydrogen,. It was necessary also for there to be regulation between temperature, pressure and catalyst activity to give the proper balance between hydrogenation and cracking.
• In the cracking of such an oil as this the polycyclic aromatics would be decomposed into molecules which would readily condense to higher-molecularweight compounds and the hydro aromatics would be dehydrogenated. However, the high pressure of hydrogen in this vapour-phase process prevented any condensation and exerted an influence opposed to the production of aromatic hydrocarbons, and favourable for the formation of hydrosaromatic hydrocarbons. The dependence of the nature of the final product upon temperature, he continued, added to the importance of the catalyst. But when that catalyst which would enable the reaction to take place at the required temperature was known, the flexibility of this part of the process from a commercial atandpoint was immediately apparent., The yields obtained by the vapourphase hydrogenation process varied between the following figures :-80 to 93 per cent, of petrol, 5 per cent. of water, 20 to 7 per cent. of gas.
Hydrogen Easily Provided.
Hydrogen, he explained, could conveniently be made from the hydrocarbon gases, extiactel during the process itself, by reaction with steam over a catalyst, but when the yield of petrol became greater and that of gas less, the independent production of hydrogen would be necessary. This presented no difficulty, however, the ammonia industry having thoroughly explored the subject.
He mentioned that hydrogenated petrol required little refining, that the method of running the vapour-phase plant gave complete control over its volatility and knock rating, and that any variation in specification that could be made by the production of petrol from crude petroleums could also be made by the coal-hydrogenation process.
Fuel oil, oil fuel, kerosene and aviation spirits had all been produced, but lubricating oils had not yet been obtained. Research, however, bad, pointed towards the likelihood of this being achieved.