MOQUETTE WEAVING
Page 50
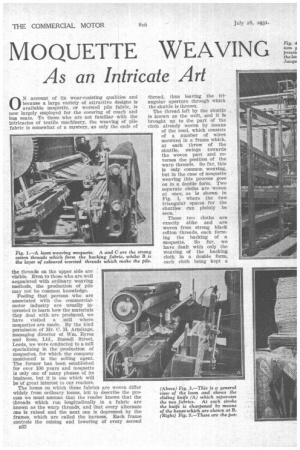
Page 51
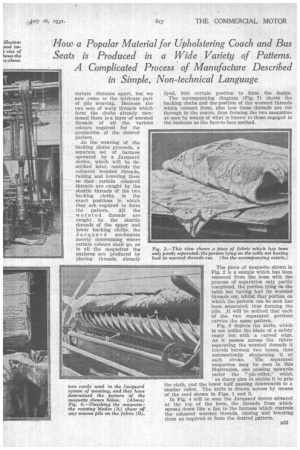
If you've noticed an error in this article please click here to report it so we can fix it.
As an Intricate Art
0 N account of its wear-resisting qualities and because a large variety of attractive designs is available moquette, or worsted pile fabric, is now largely employed for the covering of coach and bus seats. To those who are not familiar with the intricacies of textile machinery, the weaving of pile fabric is somewhat of a mystery, as only the ends of the threads on the upper side are visible. Even to those who are well acquainted with ordinary weaving methods, the production of pile may not be common knowledge.
Feeling that persons who are associated with the commercialmotor industry are usually interested to learn how the materials they deal with are produced, we have visited a mill where moquettes are made. By the kind permission of Mr. C. H. Armitage, managing director of Wm. Eyres and Sons, Ltd., Russell Street, Leeds, we were conducted to a mill specializing in the production of moquettes, for which the company mentioned is the selling agent. The former has been established for over 100 years and moquette is only one of many phases of its business, but it is one which will be of great interest to our readers.
The looms on which these fabrics are woven differ widely from ordinary looms, but to describe the pro cess we must assume that the reader knows that the threads which run longitudinally in a fabric are known as the warp threads, and that every alternate
one is raised and the next one is depressed by the frames, which are called the harness. Each frame controls the raising and lowering of every second B32
thread, thus leaving the triangular aperture through which the shuttle is thrown.
The thread left by the shuttle is known as the weft, and it is brought up to the part of the cloth already woven by means of the reed, which consists of a number of wires mounted in a frame which, at each throw of the shuttle, swings towards the woven part and reverses the position of the warp threads. So far, this is only common weaving, but in the case of moquette weaving this process goes on in a double form. Two separate cloths are woven at once, as is shown in Fig. 1, where the two triangular spaces for the shuttles• can plainly be seen.
These two cloths are exactly alike and are woven from strong black cotton threads, each forming the backing of a moquette. So far, we have dealt with only the weaving of the backing cloth in a double form, each cloth being kept a certain distance apart, but we now come to the intricate part of pile weaving. Between the two sets of warp threads which form the cloths already mentioned there is a layer of worsted threads of all the various colours required for the production of the desired pattern.
As the weaving of the backing cloths proceeds, a separate set of harness operated by a Jacquard device, which will be described later, controls the coloured worsted threads, raising and lowering them so that certain coloured threads are caught by the shuttle threads of the two backing cloths, in the exact positions in which they are required to form the pattern. All the worsted threads are caught by the shuttle threads of the upper and lower backing cloths, the Jacquard mechanism merely determining where certain colours shall go, as in all the •moquettes thQ patterns are produced by placing threads, already
dyed, into certain position to form the design.
The accompanying diagram (Fig. 7) shows the backing cloths and the position of the worsted threads which connect them, also how these threads are cut through in the centre, thus forming the two moquettes at once by means of what is known to those engaged in the business as the face-to-face method.
The piece of moquette shown in Fig. 2 is a sample which has been removed from the loom with the process of separation only partly completed, the portion lying on the table not having had its worsted threads cut, whilst that portion on which the pattern can be seen has been separated, thus forming the pile. it will be noticed that each of the two separated portions carries the same pattern.
Fig. 3 depicts the knife, which is not unlike the blade of a safety razor but with a curved edge. As it passes across the fabric separating the worsted threads it travels between two hones, thus automatically sharpening it at each stroke. The separated moquettes may, be seen in this illustration, one passing upwards under the "pin-roller," which " as sharp pins to enable it to grip the cloth, and the lower half passing downwards to a similar roller. The knife is drawn across by means of the cord shown in Figs. I_ and 3.
In Fig. 4 will be seen the Jacquard device situated at the top of the loom, the threads from which spread down like a fan to the harness which controls the coloured worsted threads, raising and lowering them as required to form the desired pattern.