Compliance science
Page 14
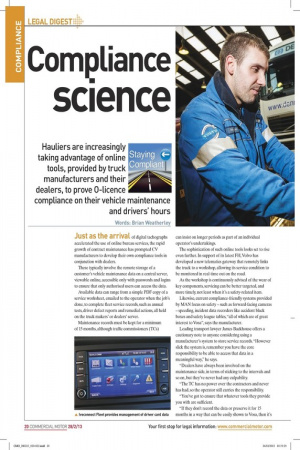
Page 15
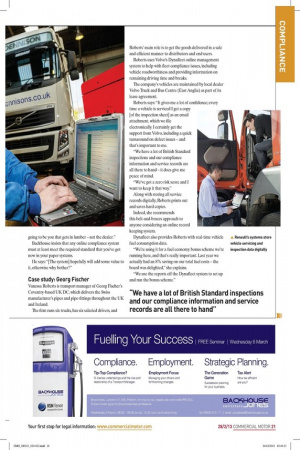
Page 16
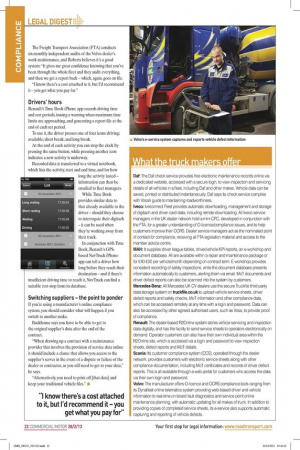
If you've noticed an error in this article please click here to report it so we can fix it.
Hauliers are increasingly taking advantage of online tools, provided by truck manufacturers and their dealers, to prove 0-licence compliance on their vehicle maintenance and drivers hours Words: Brian Weathertey Just as the arrival of digital tachographs accelerated the use of online bureau services, the rapid growth of contract maintenance has prompted CV manufacturers to develop their own compliance tools in conjunction with dealers.
These typically involve the remote storage of a customer's vehicle maintenance data on a central server, viewable online, accessible only with passwords and logins to ensure that only authorised users can access the data.
Available data can range from a simple PDF copy of a service worksheet, emailed to the operator when the job's done, to complete fleet service records, such as annual tests, driver defect reports and remedial actions, all held on the truck makers' or dealers' server.
Maintenance records must be kept for a minimum of 15 months, although traffic commissioners (TCs) can insist on longer periods as part of an individual operator's undertakings.
The sophistication of such online tools looks set to rise even further. In support of its latest FH,Volvo has developed a new telematics gateway that remotely links the truck to a workshop, allowing its service condition to be monitored in real-time out on the road.
As the workshop is continuously advised of the wear of key components, servicing can be better targeted, and more timely, not least when it's a safety-related item.
Likewise, current compliance-friendly systems provided by MAN focus on safety — such as forward-facing cameras — speeding, incident data recorders like accident black boxes and safety league tables, "all of which are of great interest to Vosa", says the manufacturer.
Leading transport lawyer James Backhouse offers a cautionary note to anyone considering using a manufacturer's system to store service records. "However slick the system is, remember you have the core responsibility to be able to access that data in a meaningful way," he says.
"Dealers have always been involved on the maintenance side, in terms of sticking to the intervals and so on, but they've never had any culpability.
"The TC has no power over the contractors and never has had, so the operator still carries the responsibility.
"You've got to ensure that whatever tools they provide you with are sufficient.
"If they don't record the data or preserve it for 15 months in a way that can be easily shown to Vosa, then it's going to be you that gets in lumber — not the dealer."
Backhouse insists that any online compliance system must at least meet the required standard that you've got now in your paper systems.
He says: "[The system] hopefully will add some value to it, otherwise why bother?"
Case study: Georg Fischer Vanessa Roberts is transport manager of Georg Fischer's Coventry-based UK DC, which delivers the Swiss manufacturer's pipes and pipe-fittings throughout the UK and Ireland.
The firm runs six trucks, has six salaried drivers, and Roberts' main role is to get the goods delivered in a safe and efficient manner to distributors and end users.
Roberts uses Volvo's Dynafleet online management system to help with fleet compliance issues, including vehicle roadworthiness and providing information on remaining driving time and breaks.
The company's vehicles are maintained by local dealer Volvo Truck and Bus Centre (East Anglia) as part of its lease agreement.
Roberts says: "It gives me a lot of confidence; every time a vehicle is serviced I get a copy [of the inspection sheet] as an email attachment, which we file electronically. I certainly get the support from Volvo, including a quick turnaround on defect issues — and that's important to me.
"We have a lot of British Standard inspections and our compliance information and service records are all there to hand — it does give me peace of mind.
"We've got a zero risk score and I want to keep it that way."
Along with storing all service records digitally, Roberts prints out and saves hard copies.
Indeed, she recommends this belt-and-braces approach to anyone considering an online record keeping system.
Dynafleet also provides Roberts with real-time vehicle fuel consumption data.
"We're using it for a fuel economy bonus scheme we're running here, and that's really important. Last year we actually had an 8% saving on our total fuel costs — the board was delighted," she explains.
"We use the reports off the Dynafleet system to set up and run the bonus scheme."
The Freight Transport Association (FTA) conducts six-monthly independent audits of the Volvo dealer's work maintenance, and Roberts believes it's a good system: "It gives me great confidence knowing that you've been through the whole fleet and they audit everything, and then we get a report back — which, again, goes on file.
"I know there's a cost attached to it, but I'd recommend it — you get what you pay for."
Drivers' hours Renault's Time Book iPhone app records driving time and rest periods, issuing a warning when maximum time limits are approaching, and generating a report file at the end of each set period.
To use it, the driver presses one of four icons: driving; available; short break; and long break.
At the end of each activity you can stop the clock by pressing the same button, while pressing another icon indicates a new activity is underway.
While Time Book provides similar data to that already available to the driver — should they choose to interrogate their digitach — it can be used when they're working away from their truck.
In conjunction with Time Book, Renault's GPSbased NavTruck iPhone app can tell a driver how long before they reach their destination — and if there's insufficient driving time to reach it, NavTruck can find a suitable rest-stop from its database.
Switching suppliers - the point to ponder If you're using a manufacturer's online compliance system, you should consider what will happen if you switch to another make.
Backhouse says you have to be able to get to the original supplier's data after the end of the contract.
"When drawing up a contract with a maintenance provider that involves the provision of service data online it should include a clause that allows you access to the supplier's server in the event of a dispute or failure of the dealer or contractor, as you still need to get to your data," he says.
"Alternatively, you need to print off [that data] and keep your traditional vehicle files." • Daf: The Daf check service provides free electronic maintenance records online via a dedicated website, accessed with a secure login, to view inspection and servicing details of all vehicles in a fleet, including Daf and other makes. Vehicle data can be saved, printed or distributed instantaneously. Daf says its check service complies with Vosa's guide to maintaining roadworthiness.
Iveco: Iveconnect Fleet provides automatic downloading, management and storage of digitach and driver card data, including remote downloading. All Iveco service managers in the UK dealer network hold a mini-CPC, developed in conjunction with the FTA, for a greater understanding of 0-licence/compliance issues, and to help customers improve their OCRS. Dealer service managers act as the nominated point of contact for compliance, receiving all FTA legislation material and access to the member advice centre.
MAN: It supplies driver league tables, driver/vehicle KPI reports, an e-workshop and document database. All are available within a repair and maintenance package or for £40-£50 per vehicle/month depending on contract term. E-workshop provides consistent recording of safety inspections, while the document database presents information automatically to customers, alerting them via email. MoT documents and driver defect reports can also be scanned into the system by customers. Mercedes-Benz: All Mercedes UK CV dealers use the secure Truckfile third-party data storage system on truckfile.co.uk to upload vehicle service sheets, driver defect reports and safety checks, MoT information and other compliance data, which can be accessed remotely at any time with a login and password. Data can also be accessed by other agreed authorised users, such as Vosa, to provide proof of compliance.
Renault: The dealer-based R2Online system stores vehicle servicing and inspection data digitally, and has the facility to send service sheets to operators electronically on demand. Operator customers can also have their own individual area within the R2Online site, which is accessed via a login and password to view inspection sheets, defect reports and MoT details.
Scania: Its customer compliance system (CCS), operated through the dealer network, provides customers with electronic service sheets along with other compliance documentation, including MoT certificates and records of driver defect reports. This is all available through a web portal for customers who access the data via their own login and password.
Volvo: The manufacturer offers 0-licence and OCRS compliance tools ranging from its Dynafleet online telematics system providing web-based driver and vehicle information to real-time on-board fault diagnostics and service point online maintenance planning, with automatic updating for all makes of truck. In addition to providing copies of completed service sheets, its e-service also supports automatic capturing and reporting of vehicle defects.