OILING EFFICIENCY A MATTER OF DESIGN.
Page 57
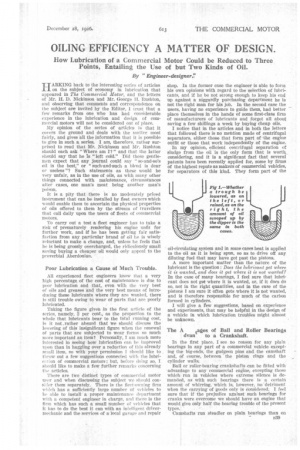
Page 58
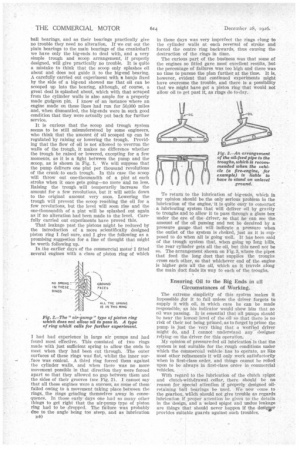
Page 59
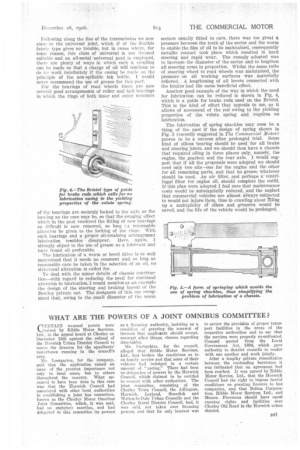
If you've noticed an error in this article please click here to report it so we can fix it.
How Lubrication of a Commercial Motor Could be Reduced to Three Points, Entailing the Use of but Two Kinds of Oil.
By "Engineer-designer."
HARKING back to the interesting series of articles on the subject of economy in lubrication that appeared in The Commercial Motor, and the letters of Mr. H. D. Nickinson and Mr. George IL Rushton, and observing that comments and correspondence on the subject are invited by the Editor, I trust that a few remarks from one who has had considerable experience in the lubrication and design of commercial motors will not be considered out of place.
My opinion of the series of articles is that it covers the ground and deals with the matter most fairly, and gives all the information that it is possible to give in such a. series. I am, therefore, rather surprised to read that Mr..Nickinson and Mr. Rushton should each ask "Where am I?" and that the latter should say that he is "left cold." Did these gentlemen expect that any journal could say "so-and-so's oil is the best," or "such-and-such a blend is dear' or useless "? Such statements as these would be very unfair, as in the use of oils, as with many other things connected with maintenance, circumstances alter cases, one man's meat being another man's poison,
It is a pity that there is no moderately priced instrument that can be installed by fleet owners which would enable them to ascertain the physical properties of oils offered to them by the stream of travellers that call daily upon the users of fleets of commercial motors.
To carry out a test a fleet engineer has to take a risk of prematurely rendering his engine unfit for further work, and if he has been getting fair satisfaction from any particular brand of oil he is wisely reluctant to make a change, and; unless he feels that he is being grossly overcharged, the ridiculously small saving buying a cheaper oil would only appeal to the proverbial Aberdonian.
Poor Lubrication a Cause of Much Trouble.
All experienced fleet engineers know that a very high percentage of the cost of maintenance -is due to Poor lubrication and that, even with the very best of oils and greases and the very best means of introducing these lubricants where they are wanted, there is still trouble owing to wear of parts that are poorly
lubricated.
Taking the figure given in the first article of the series, namely, 2 per cent., as the proportion to the whole that lubricants bear to the total running cost, is it not ,rather absurd that we should discuss the lowering of this insignificant figure when the renewal of parts that are subjected to wear forms so much niece important an item? Personally, I am much more interested in seeing how lubrication can be improved upon than in haggling over a reduction of this already small item, so with your permission I shonid like to throw out a few suggestions connected with the lubriestion of commercial motors but, before tiohig so, I should like to make a few further remarks concerning the nrticles.
There are two distinct types of commercial motor user and when discussing the subject we should conshier them them separately. There is the fleet-owning firm which. has a sufficiently large number of vehicles to he able to install a proper maintenance department with a competent engineer in charge, and there is the firm which has such a small number of' vehicles that it has to do the best it can with an intelligent drivermechanic and the services of a local garage and repair
shop. In the former case the engineer is able to form his own opinions with regard to the selection of lubricants, and if he be not strong enough to keep his end up against a niggardly purchasing department he is not the right man for his job. In the second case the users, having no experience to guide them, had better place themselves in the hands of some first-class firm of manufacturers of lubricants and forget all about saving a few shillings a week by buying cheap oils.
I notice that in the articles and in both the letters that followed there is no mention made of centrifugal separators, either those that form part of -the engine outfit or those that work independently of the engine.
In my opinion, efficient centrifugal separation of sludge from the oil is the only form that Is worth considering, and it is a significant fact that several patents have been recently applied for, some by firms of the highest repute as makers of commercial vehicles, for separators of this kind. They form part of the oil-circulating system and in some cases heat is applied to the oil as it is being spun, so as to drive off any diluting fuel that may have got past the pistons.
A more important matter than the nature of the lubricant is the question : Does the lubricant get where it ü wanted, and does it get where it is not wanted? In the case of many bearings, I feel sure that lubricant does not get where it is wanted, or, if it does do so, not in the right quantities, and in the case of the pistons I am sure it often gets where it is not wanted, and is therefore responsible for much of the carbon formed in cylinders.
I will give a few suggestions, based on experience and experiments, that may be helpful in the design of a vehicle in which lubrication troubles might almost be unknown.
The A rages of Ball and Roller Bearings dvan to a Crankshaft.
In the first place, I see no reason for any plain bearings in any part of a commercial vehicle excepting the big-ends, the gudgeon pins and the camshaft and, of course, between the piston rings and the cylinder walls.
Ball or roller-bearing crankshafts can be fitted with advantage to any commercial engine, excepting those which: run in vehicles where extreme silence is demanded, as with such bearings there is a certain amount of whirring, which is, however, no detriment when the carrying of goods only is considered I feel sure that if the prejudice against such bearings for cranks were overcome we should have an engine that would give only half the bearing trouble of the present types.
Camshafts run steadier on plain bearings than on 539
ball bearings, and as their bearings practically give no trouble they need no alteration_ If we cut out the plain bearings to the main bearings of the crankshaft we have only the big-ends to deal with, and a very simple trough and scoop arrangement, if properly designed, will give practically no trouble. It is quite a mistake to think that the scoop only splashes oil about and does not guide it to the big-end bearing. A carefully carried out experiment with a banjo fixed by the side of a big-end showed me that oil can be scooped up into the bearing, although, of course, a great deal is splashed about, which with that scraped from the cylinder walls is also ample for a properly made gudgeon pin. I know of an instance where an engine made on these lines had run for 50,000 miles and, when dismantled, the big-ends were in such good condition that they were actually put back for further service.
It is curious that the scoop and trough system seems to be still misunderstood by some engineers, who think that the amount of oil scooped up can be regulated by raising or lowering the trough. Providing that the flow of oil is not allowed to overrun the walls of the trough, it makes no difference whether the trough be raised or lowered, excepting for a few moments, as it is a fight between the pump and the scoop, as is shown in Pig. 1. We will suppose that the pump delivers one pint per thousand revolutions of the crank to each trough. In this case the scoop will throw out one-thousandth of a pint at each stroke when it once gets going—no more and no less. Raising the trough will temporarily increase the amount for a few revolutions, but it will settle down to the original amount very soon. Lowering the trough will prevent the scoop reaching the oil for a few revolutions, but the level will soon rise and the one-thousandth of a pint will be splashed out again as if no alteration had been made to the level. Carefully carried out experiments have proved this.
That leakage past the pistons might be reduced by the introduction of a more scientifically designed piston ring I feel sure, and I give the following as a promising suggestion for a line of thought that might be worth following up.
In the earlier days of the commercial motor I fitted several engines with a class of piston ring of which
I had had experience in large air pumps and had found most effective. This consisted of two rings made with just sufficient spring to allow the ends to meet when they had been cut through. The outer surfaces of these rings was flat, whilst the inner surface was conical. A third ring forced them against the cylinder walls, and when there was no more movement possible in that direction they were forced apart so that they allowed no gap between them and the sides of their grooves (see Pig. 2). I cannot say that all these engines were a success, as some of them' failed owing to a movement taking place between the rings, the rings grinding themselves away in consequence. In those early days one had so many other things to get right that the air-pump type of piston ring had to be dropped. The failure was probably due to the angle being too steep, and as lubrication
u-40 in those days was very imperfect the rings clung to the cylinder walls at each reversal of stroke and forced the centre ring backwards, thus causing the destruction of the rings in time The curious part of the business was that some of the engines so fitted gave most excellent results, but the percentage of failures was too high and there was no time to pursue the plan further at the time. It is, however, evident that continued experiments might have overcome the trouble, and there is a possibility that we might have got a piston ring that would not allow oil to get past it, as rings do to-day.
To return to the lubrication of big-ends, which in my opinion should be the only serious problem in the lubrication of the engine, it is quite easy to construct a lubricating system that will deliver oil by gravity to troughs and to allow it to pass through a glass box under the eye of the driver, so that he can see the amount of the oil passing and not be deceived by a pressure gauge that will indicate a pressure when the outlet of the system is choked, just as it is supposed to do when all is going well. It has been said of the trough system that, when going up long hills, the rear cylinder gets all the ail, but this need not be so. The arrangement shown on Fig. 3, where the Pipes that feed the long duct that supplies the troughs cross each other, so that whichever end of the engine is higher gets all the oil, which as it travels along the main duct finds its way to each of the troughs.
Ensuring Oil to the Big Ends in all Circumstances of Working.
The extreme simplicity of this system makes it impossible ,for it to fail unless the driver forgets to supply it with oil, in which case he can be made responsible, as his indicator would show him that no oil was passing, It is essential that all pumps should be near the lowest level of the oil so that there is no risk of their not being primed, as to forget to prime the pump is just the very thing that a worried driver might do, and I cannot understand any designer relying on the driver for this operation.
My opinion of pressure-fed oil lubrication is that the system is not suitable for the rough conditions under which the commercial vehicle has to operate, as like most other refinements it will only work satisfactorily when in first-class order, and things cannot be relied upon to be always in first-class order in commercial vehicles.
With regard to the lubrication of the clutch spigot and clutch-withdrawal collar, there should be no reasorl for special attention if properly designed oilretaining ball bearings be used. We now come to the gearbox, which should not give trouble as regards lubrication if proper attention he given to the details in the design, and a seized spigot and undue leakage are things that should never happen if the desigker provides suitable guards against such troubles. ""' Following along the line of the transmission we now come to the universal joint, which if of the flexible fabric type gives no trouble, but in eases where, for sonic reason, this class of universal is not deemed suitable and an all-metal universal joiht is employed, there are plenty of ways in which such a coupling can he made so that a charge of oil will continue to do its work indefinitely if the casing be made on the principle of the non-spillable ink bottle. I would never recommend the use of grease for this part.
For the bearings of road wheels there are now several good arrangements of roller and ball hearings in which the rings of both inner and outer members
of the bearings are securely locked to the axle, or the housing as the case may be, so that the swaging effect which in the past rendered the fitting of new bearings FO difficult is now removed, so long es reasonable attention be given to the locking of the rings. With such bearings and a proper oil-retaining arrangement lubrication troubles disappear. Here, again, I strongly object to the use of grease as a lubricant and have found oil preferable.
The lubrication of a worm or bevel drive is so well understood that it needs no _comment and, so long as reasonable care be taken in the selection of an oil, no structural alteration is called for.
To deal with the minor details of chassis construetion—with regard to reducing the need for continual attention to lubrication, I would mention as an example the design of the steering and braking layout of the Bentley private car. The designers of this car recognized that, owing to the small diameter of the worm sectors usually fitted to cars, there was too great a pressure between the teeth of the sector and the worm to enable the film of oil to be maintained, consequently metallic contact took place which resulted in hard steering and rapid wear. The remedy adopted was to increase the diameter of the sector and to lengthen all steering arms in proportion. Whilst the same ratio of steering wheel to road wheels was 'maintained, the pressure on all working surfaces was materially relieved. A lengthening of all levers connected with the brakes had the same beneficial effect.
Another good example of the way in which the need for lubrication can be reduced is shown in Fig. 4, which is a guide for brake rods used on the Bristol. This is the kind of effort that appeals to me, as it allows of movement of the rod owing to the yielding properties of the volute spring and requires no lubrication.
The lubrication of spring shackles may soon be a thing of the past if the design of spring shown in Fig. 5 (recently suggested in The Commercial Motor) proves to be a success after prolonged trial. Some kind of oilless bearing should be used for all brake and steering joints, and we should then have a chassis that required oiling in three places only, namely, the engine, the gearbox and the rear axle. I would suggest that if all the proposals were adopted we should need only two oils—one for the engine and the other for all remaining parts, and that ho grease whatever should be used. An air filter, and perhaps a-centrifugal filter for engine oil, should complete the outfit. If this plan were adopted I feel sure that maintenance costs would be substantially reduced, and the neglect that commercial vehicles are almost always subjected to would not injure them, time in crawling about Ming up a multiplicity of oilers and greasers would be saved, and the life of the vehicle would be prolonged.