el msuRvEy g O a ur ra s urvey em e p m l o b y r i n a g ce a d r o w u o n r d ks 8 h5o0ps t ech nicians and 148 apprentices,
Page 40
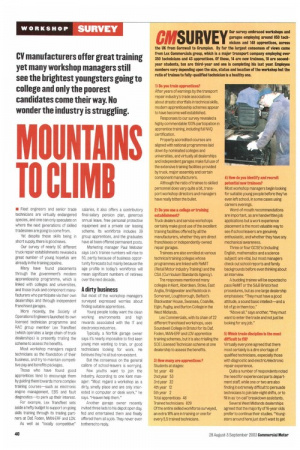
Page 41
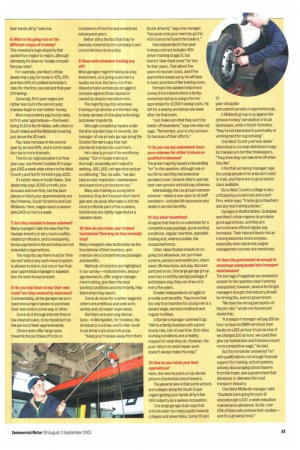
If you've noticed an error in this article please click here to report it so we can fix it.
across the UK from Cornwall to Grampian. By far the largest consensus of views came from Lex Commercials group. which is a major transport company employing over 350 technicians and 43 apprentices. Of these, 14 are new trainees, 18 are secondyear students, ten are third-year and one is completing his last year. Employee numbers vary depending upon the size, status and location of the workshop but the ratio of trainee to fully-qualified technician is a healthy one.
1) Do you train apprentices?
After years of warnings by the transport repair industry's trade associations about drastic shortfalls in technical skills, modern apprenticeship schemes appear to have become well established.
Responses to our survey revealed a highly commendable 100% participation in apprentice training, including full NVQ certification.
Properly accredited courses are aligned with national programmes laid down by nominated colleges and universities, and virtually all dealerships and independent garages make full use of the extensive training facilities provided by truck, major assembly and certain component manufacturers.
Although the ratio of trainee to shied personnel does vary quite a bit, transport workshop directors and managers have really bitten the bullet.
2) Do you use a college or training establishment?
Truck dealers and service workshops certainly make good use of the excellent training facilities offered by all the manufacturers, whether they are direct franchisees or independently-owned repair garages.
Trainees are also enrolled at various technical training colleges whose programmes are linked with ReMIT (Retail Motor Industry Training) and the GSA (Curriculum Standards Agency).
The responses mentioned many colleges in Kent, Aberdeen, Stoke, East Anglia, Bridgewater and Radstock in Somerset, Loughborough, Belfast's Blackwater House, Swansea, Coalville, Elgin, Rugby, and Burton College in the West Midlands.
Lex Commercials, with its chain of 22 different franchised workshops, uses Soundwell College in Bristol for its Daf, Foden, MAN-ERF and LDV apprentice training schemes, but it is also trialling the SOE Licensed Technician scheme at one dealership to assess the benefits.
3) How many are apprentices?
Students at stages: 1st year 49
2nd year 53 3rd year 32
4th year 12 5th year 2 Total apprentices 48 Trained technicians 829
Of the entire skilled workforce surveyed,
an extra 18% are in training or one for every 5.5 trained technicians. 4) How do you identify and recruit potential new trainees?
Most workshop managers begin looking for suitable young people before they've even left school, in some cases using careers evenings.
Word-of-mouth recommendations are important, as are handwritten job applications but a work experience placement is the most valuable way to see if school leavers are genuinely enthusiastic, and whether they have any mechanical awareness.
Three or four GCSE's (including English, mathematics and a science subject) are vital, but most managers check out school reports and family backgrounds before even thinking about an interview.
A budding trainee will be expected to pass ReMIT or the S&B Bristol test procedures, but as one large dealership emphasises: "They must have a good attitude, a sound basic intellect—and a bit of go in them too."
"Above all," says another, "they must want to enter the trade and not just be looking for any job."
5) Which trade discipline is the most difficult to fill?
Virtually everyone agreed that there most certainly is a dire shortage of qualified technicians, especially those with diagnostic and electric/electronic repair experience.
Quite a number of respondents noted the need for experienced parts department staff, while one or two are also finding it extremely difficult to persuade technicians to join late-night shifts, or to fill in as 'on-call' breakdown assistants.
Several West Midlands dealerships agreed that the majority of 16-year olds prefer to continue their studies. 'Youngsters around here just don't want to get
6) What is the going rate at the different stages of training?
This revealed a huge disparity that varied from region to region, although ultimately it's down to 'locally competitive pay rates'.
For example, one West Lothian dealership's pay formulae is 42%, 65% and then 80% of a skilled technician's rate (for the first, second and final year of training).
Generally first-year wages are rather lean but in the second year, trainees begin to earn better money.
Most respondents pay hourly rates to first-year apprentices—the lowest being 21.83 in North Wales, with others in South Wales and the Midlands hovering just above the £2 mark Pay rates increase in the second year by around 50%, and in some cases the rise is more dramatic.
There's no regional pattern to finalyear pay; one Home Counties firm pays just £160 a week while others in the West Country and North Yorkshire pay £220.
it's better news in South Wales. One dealership pays £1,100 a month, plus bonuses and overtime, but the plum places to finish your apprenticeship are the Potteries, South Yorkshire and East Midlands. Here, wages reach a reasonable £400 or more a week.
7) Are they included In bonus schemes? Many managers take the view that the haulage industry is very much a safetyrelated profession, and consequently, bonus payments in the workshop are not extended to apprentices.
The majority say there must be 'time served' before any such reward system is allowed to kick in, but one or two finalyear apprentices manage to squeeze into the team bonus bracket.
8) Do you help them to buy their own tools? Are they covered by insuranceP Commendably all the garages we surveyed encourage trainees to purchase their own tools in some way or other.
Some do it through interest-free or low-interest loans, to be repaid across the period of their apprenticeship.
Others even offer large sums towards the purchase of tools on completion of the first and sometimes subsequent years.
Better still is the fact that they're basically covered by the company's own corporate insurance policy.
9) Does such extensive training pay off?
Most garages regard training as a key investment, as is giving customers a quality service. But here, non-franchised private workshops struggle to compete against those backed or owned by chassis manufacturers.
The majority say that extensive training programmes are the best way to keep abreast of changing technology and dealer standards.
Although completing repairs under the time standard has its rewards, the manager of one private garage along the Scottish Borders says that high standards impress his customers.
He's clearly proud of his workforce, saying: "Our in-house training is thorough, especially with regard to welding, ABS, EBS, refrigeration and airconditioning." But, he adds, "we also have proper inspection, maintenance and supervisory procedures too."
Many see training as a long-term business; they don't expect short-term gain and, because aftersales is still the most profitable part of the business, technicians are rightly regarded as a valuable asset.
10) How do you retain your trained technicians? How long do they normally stay?
Many managers view technicians as the foundations of their business, and maintain very competitive pay packages and benefits.
Methods of retention are highlighted in our survey—motivate them, encourage teamwork, offer engine management training, give them the best working conditions and importantly help them when 'hey need it.
Some do move for a better wage but others are ambitious and seek work variety and a broader experience.
But there are worrying distractions—in Morayshire, for instance, the oil industry is a draw, and further south truck drivers are a bad influence.
"Keep your trainees away from them
[truck drivers]," says one manager, "because once your man has got his HGV licence he'll pack the trade in."
One independent's five-year trainee contract includes HGV driver training at age 21, but there's 'claw-back cover' for two further years. That allows five years to recover costs, and if the apprentice leaves early, he will have to bear a portion of the training costs.
Perhaps the saddest indictment comes from Ireland where a familyowned workshop is suing a former apprentice for 17,000 training costs. He left for a nearby workshop one week after his final exam.
"Just make sure that they won't be better off elsewhere," says one wise old sage. "Remember, you're only successful because of their efforts."
11) Do you run any endowment Insurance schemes for either trainees or qualified tradesmen?
The great majority issued a resounding "no" to this question, although one or two firms said they had extensive accident cover. Several others operate their own pension and sick pay schemes.
Interestingly, the Lex group's pension scheme—which is now open to all staff members—includes life assurance and death in service benefits.
12) Any other Incentives?
All agree that there's no substitute for a competitive pay package, good working conditions, regular overtime, specialist training and, where possible, the occasional bonus.
Other ideas floated include an ongoing tool allowance, car purchase scheme, pension and healthcare, share saver, life insurance, sick pay, discount card and so on. One large garage group even has a monthly savings package; if technicians stay, they can draw on it every five years.
Smaller independents struggle to provide such benefits. They know that the only true incentive for young men is a decent wage, service conditions and regular holidays.
A Borders manager summed it up: "We're a family business with a good hourly rate, lots of overtime, first-class working conditions and a healthy respect for what they do. However, the poor return on retail repair work doesn't always make this easy."
13) How do you retain your best apprentices?
Here, the returns paint a truly dismal picture of potential school-leavers.
The general view is that some schools and colleges along the South Coast regard getting your hands dirty in the HGV industry as a useless occupation.
One large garage chain says that schools steer too many pupils towards colleges and universities. Some 20 and
21 year-old applic
ants cannot survive on apprentice pay.
A Midlands group is up against the `grease monkey' perception of truck technicians, while in South Yorkshire, "they're not interested in punctuality or working hard for a good living".
One West Country service dealer sited close to six main distributors says its trainees are terrible timekeepers. "They think they can take time off when they like".
A Norfolk workshop manager says the young people in his area don't want to train, and there are no good technicians available.
But a West Country college is also criticised by a local truck and coach firm, which says: "It lacks good teachers and any real training policies."
Garages in Bedfordshire, Grampian and West Lothian regions do produce good apprentices, and they are nurtured and offered regular pay increases. Their interest levels rise as training becomes more complex, especially when electronic engine management courses are mentioned.
14) Does the government do enough to encourage young people into transport maintenance?
The barrage of negatives we received in answer to this question wasn't entirely unexpected; however, several forthright managers thought that industry should be driving this, and not government.
"We have the wrong perception of the job rata," wrote one Avonmouth dealership.
"A transport manager will pay £50 an hour to have his BMW serviced, then baulks at a25 an hour truck service; if we charged £50 an hour, we could then give our technicians and trainees a much more competitive wage," he said.
But the remainder answered "no" with qualifications: not enough financial support for training, school systems actively discouraging school leavers from the trade, and a government that distances or alienates the road transport industry.
One West Midlands manager said; "Students here going for post-16 education get a £30 a week education maintenance allowance. So far, over 63% of them will continue their studies— and it's a growing trend."