Roots to success
Page 20
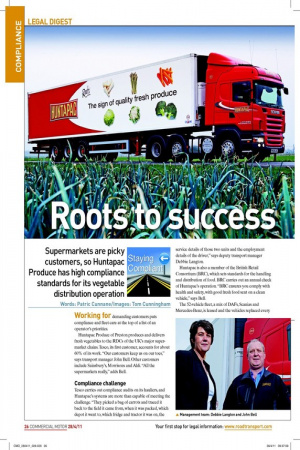
Page 21
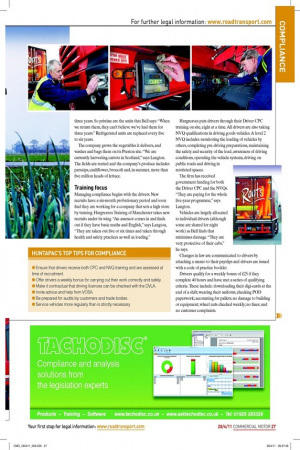
Page 22
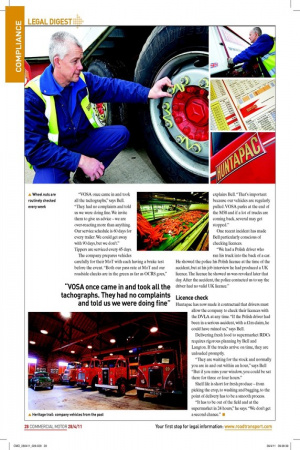
If you've noticed an error in this article please click here to report it so we can fix it.
Supermarkets are picky customers, so Huntapac Produce has high compliance standards for its vegetable distribution operation
Words: Patric Cunnane/Images: Tom Cunningham Working for demanding customers puts compliance and leet care at the top of a list of an operator’s priorities.
Huntapac Produce of Preston produces and delivers fresh vegetables to the RDCs of the UK’s major supermarket chains. Tesco, its irst customer, accounts for about 60% of its work. “Our customers keep us on our toes,” says transport manager John Bell. Other customers include Sainsbury’s, Morrisons and Aldi. “All the supermarkets really,” adds Bell.
Compliance challenge
Tesco carries out compliance audits on its hauliers, and Huntapac’s systems are more than capable of meeting the challenge. “They picked a bag of carrots and traced it back to the ield it came from, when it was packed, which depot it went to, which fridge and tractor it was on, the service details of those two units and the employment details of the driver,” says deputy transport manager Debbie Langton.
Huntapac is also a member of the British Retail Consortium (BRC), which sets standards for the handling and distribution of food. BRC carries out an annual check of Huntapac’s operation. “BRC ensures you comply with health and safety, with good fresh food sent on a clean vehicle,” says Bell.
The 52-vehicle leet, a mix of DAFs, Scanias and Mercedes-Benz, is leased and the vehicles replaced every three years. So pristine are the units that Bell says: “When we return them, they can’t believe we’ve had them for three years.” Refrigerated units are replaced every ive to six years.
The company grows the vegetables it delivers, and washes and bags them on its Preston site. “We are currently harvesting carrots in Scotland,” says Langton. The ields are rented and the company’s produce includes parsnips, caulilower, broccoli and, in summer, more than ive million heads of lettuce.
Training focus
Managing compliance begins with the drivers. New recruits have a six-month probationary period and soon ind they are working for a company that sets a high store by training. Hargreaves Training of Manchester takes new recruits under its wing. “An assessor comes in and inds out if they have basic maths and English,” says Langton, “They are taken out ive or six times and taken through health and safety practices as well as loading.” Hargreaves puts drivers through their Driver CPC training on site, eight at a time. All drivers are also taking NVQ qualiications in driving goods vehicles. A level 2 NVQ includes monitoring the loading of vehicles by others, completing pre-driving preparations, maintaining the safety and security of the load, awareness of driving conditions, operating the vehicle systems, driving on public roads and driving in restricted spaces.
The irm has received government funding for both the Driver CPC and the NVQs. “They are paying for the whole ive-year programme,” says Langton.
Vehicles are largely allocated to individual drivers (although some are shared for night work) as Bell inds that minimises damage. “They are very protective of their cabs,” he says.
Changes in law are communicated to drivers by attaching a memo to their payslips and drivers are issued with a code of practice booklet.
Drivers qualify for a weekly bonus of £25 if they complete 40 hours and have met a series of qualifying criteria. These include: downloading their digi-cards at the end of a shift; wearing their uniform; checking POD paperwork; accounting for pallets; no damage to building or equipment; wheel nuts checked weekly; no ines; and no customer complaints. “VOSA once came in and took all the tachographs,” says Bell.
“They had no complaints and told us we were doing ine. We invite them to give us advice – we are over-reacting more than anything.
Our service schedule is 60 days for every trailer. We could get away with 90 days, but we don’t.” Tippers are serviced every 45 days.
The company prepares vehicles carefully for their MoT with each having a brake test before the event. “Both our pass rate at MoT and our roadside checks are in the green as far as OCRS goes,” explains Bell. “That’s important because our vehicles are regularly pulled. VOSA parks at the end of the M58 and if a lot of trucks are coming back, several may get stopped.” One recent incident has made Bell particularly conscious of checking licences.
“We had a Polish driver who ran his truck into the back of a car.
He showed the police his Polish licence at the time of the accident, but at his job interview he had produced a UK licence. The licence he showed us was revoked later that day. After the accident, the police contacted us to say the driver had no valid UK licence.”
Licence check
Huntapac has now made it contractual that drivers must allow the company to check their licences with the DVLA at any time. “If the Polish driver had been in a serious accident, with a £1m claim, he could have ruined us,” says Bell.
Delivering fresh food to supermarket RDCs requires rigorous planning by Bell and Langton. If the trucks arrive on time, they are unloaded promptly.
“They are waiting for the stock and normally you are in and out within an hour,” says Bell “But if you miss your window, you could be sat there for three or four hours.” Shelf life is short for fresh produce – from picking the crop, to washing and bagging, to the point of delivery has to be a smooth process.
“It has to be out of the ield and at the supermarket in 24 hours,” he says. “We don’t get a second chance.” ■