Flexible, Light and Arong...
Page 37
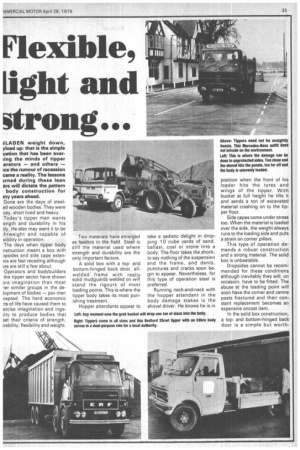
Page 38
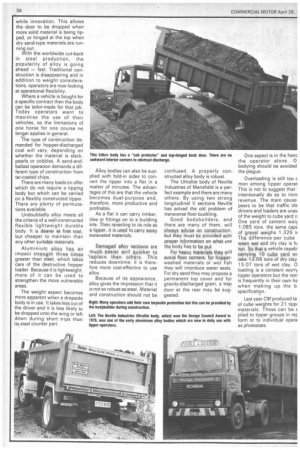
If you've noticed an error in this article please click here to report it so we can fix it.
tILADEN weight down, yload up: that is the simple uation that has been exerting the minds of tipper orators — and others — ice the rumour of recession came a reality. The lessons 3rned during these lean ars will dictate the pattern body construction for my years ahead.
Gone are the days of steeled wooden bodies. They were cey, short lived and heavy. Today's tipper man wants ength and durability in his dy. He also may want it to be htweight and capable of xibility in operation.
The days when tipper body nstruction meant a box with D ps ides and side cape extenins are fast receding although are are still a few about.
Operators and bodybuilders the tipper sector have shown D re imagination than most ler similar groups in the delopment of bodies — psv men cepted. The hard economic :ts of life have caused them to ercise imagination and ingeiity to produce bodies that aet their criteria of strength, irability, flexibility and weight.
Two materials have emerged as leaders in the field_ Steel is still the material used where strength and durability are the only important factors.
A solid box with a topand bottom-hinged back door, allwelded frame with really solid mudguards welded on will stand the rigours of most loading points. This is where the tipper body takes its most punishing treatment.
Hopper attendants appear to take a sadistic delight in dropping 10 cube yards of sand, ballast, coal or stone into a body. The floor takes the shock, to say nothing of the suspension and the frame, and dents, punctures and cracks soon begin to appear. Nevertheless, for this type of operation steel is preferred.
Running neck-and-neck with the hopper attendant in the body damage stakes is the shovel driver. He knows he is in position when the front of his loader hits the tyres and wings of the tipper. With bucket at full height he tilts it and sends a ton of excavated material crashing on to the tipper floor.
Side capes come under stress too. When the material is loaded over the side, the weight always runs to the loading side and puts a strain on corner pillars.
This type of operation demands a robust construction and a strong material. The solid box is unbeatable.
Dropsides cannot be recommended for these conditions although inevitably they will, on occasion, have to be fitted. The abuse at the loading point will soon have the corner and centre posts fractured and their constant replacement becomes an expensive oncost item.
In the solid box construction, a topand bottom-hinged back door is a simple but worth while innovation. This allows the door to be dropped when more solid material is being tipped, or hinged at the top when dry sand-type materials are running out With the worldwide cut-back in steel production, the popularity of alloy is going ahead — fast. Traditional construction is disappearing and in addition to weight considerations, operators are now looking at operational flexibility.
Where a vehicle is bought for a specific contract then the body can be tailor-made for that job. Today operators want to maximise the use of their vehicles, so the limitations of one horse for one course no longer applies in general.
The type of construction demanded for hopper-discharged coal will vary, depending on whether the material is slack, pearls or cobbles. A sand-andballast operation demands a different type of construction from tar-coated chips.
There are many loads on offer which do not require a tipping body but which can be carried on a flexibly constructed tipper. There are plenty of permutations available.
Undoubtedly alloy meets all the criteria of a well-constructed flexible lightweight durable body. It is dearer at first cost, but cheaper to maintain than any other suitable materials.
Aluminium alloy has an impact strength three times greater than steel, which takes care of the destructive hopper loader. Because it is lightweight, more of it can be used to strengthen the more vulnerable areas.
The weight aspect becomes more apparent when a dropside body is in use. It takes less out of the driver and it is less likely to be dropped onto the wing or left. down during short trips than its steel counter part. Alloy bodies can also be supplied with fold-in sides to convert the tipper into a flat in a matter of minutes. The advantages of this are that the vehicle becomes dual-purpose and, therefore, more productive and profitable.
As a flat it can carry timber, tiles or fittings on to a building site. Then reverting to its role as a tipper, it is used to carry away excavated materials.
Damaged alloy sections are much easier and quicker to replace than others. This reduces downtime; it is therefore more cost-effective to use alloy.
Because of its appearance, alloy gives the impression that it is not so robust as steel. Material and construction should not be confused. A properly constructed alloy body is robust.
The Ultralite body of Neville Industries of Mansfield is a per'feet example and there are many others. By using two strong longitudinal V sections Neville has solved the old problem of transverse floor buckling.
Good bodybuilders, and there are many of them, will always advise on construction, but they must be provided with proper information on what use the body has to be put.
For heavy materials they will avoid floor corners; for hopperwashed materials or wet fish they will intorduce water seals. For dry sand they may propose a permanent top cover and for gravity-discharged grain, a trap door at the rear may be sug: gested. One aspect is in the hanc the operator alone. 0 bodying should be avoided the plague.
Overloading is still too c mon among tipper operat This is not to suggest that intentionally do so to inert revenue. The main cause pears to be that traffic cle drivers and loaders are unav of the weight to cube yard n One yard of cement wei 1_085 tons, the same cape of gravel weighs 1.325 to The difference per cube ween wet and dry clay is h. ton. So that a vehicle capab carrying 10 cube yard wc take 12.05 tons of dry clay 1 5.07 tons of wet clay. 0 loading is a constant worry tipper operators but the rerr is frequently in their own hE when making up the b specification.
Last year CM produced ta of cube weights for 21 tipp materials. These can be E plied to tipper groups in rer form or to individual opera as photostats.