Workshop cost millions
Page 56
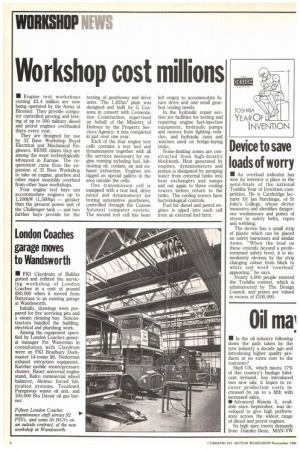
If you've noticed an error in this article please click here to report it so we can fix it.
• Engine test workshops costing 23.4 million are now being operated by the Army at Bicester. They provide computer controlled proving and testing of up to 500 military diesel and petrol engines overhauled there every year.
They are designed for use by 32 Base Workshop Royal Electrical and Mechanical Engineers. REME claims they are among the most technologically advanced in Europe. The requirement came from the expansion of 32 Base Workshop to take on engine, gearbox and other major assembly overhaul from other base workshops.
Four engine test bays can accommodate engines up to 1,100kW (1,500hp) — greater than the present power unit of the Challenger tank — and two further bays provide for the testing of gearboxes and drive units. The 1,825m2 plant was designed and built by G Cussons in consort with Cementation Construction, supervised on behalf of the Ministry of Defence by the Property Services Agency; it was completed in just over one year.
Each of the four engine test cells contains a test bed and dynamometer together with all the services necessary for engine running including fuel, lubricating oil, coolant, air and exhaust extraction. Engines are rigged on special pallets in the area outside the cells.
One transmission cell is equipped with a test bed, drive motor and dynamometer for testing automotive gearboxes, controlled through the Cusson Autotest computer system. The second test cell has been left empty to accommodate future drive unit and small gearbox testing needs.
In the hydraulic repair section are facilities for testing and repairing engine fuel-injection equipment, hydraulic pumps and motors from fighting vehicles, and hydraulic rams and winches used on bridge-laying tanks.
Noise-limiting zones are constructed from high-density blockwork. Heat generated by engines, dynamometers and pumps is dissipated by pumping water from external tanks into heat exchangers and sumps and out again to three cooling towers before return to the tanks. The cooling towers have bacteriological controls.
Fuel for diesel and petrol engines is piped into each cell from an external fuel farm.