NEW DEPOTS: NEW TRAFFIC FLOWS
Page 78
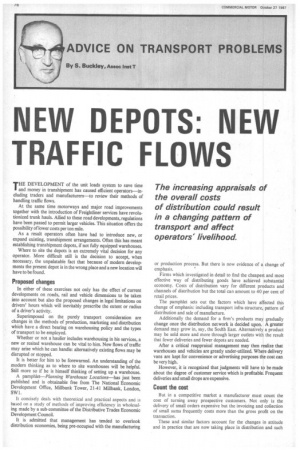
Page 79
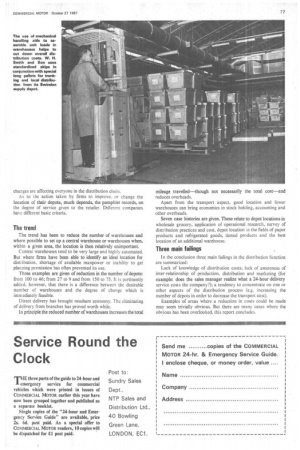
If you've noticed an error in this article please click here to report it so we can fix it.
The increasing appraisals of the overall costs of distribution could result in a changing pattern of transport and affect operators' livelihood.
THE DEVELOPMENT of the unit loads system to save time and money in transhipment has caused efficient operators—including traders and manufacturers—to review their methods of handling traffic flows.
At the same time motorways and major road improvements together with the introduction of Freightliner services have revolutionized trunk hauls. Allied to these road developments, regulations have been passed to permit larger vehicles. This situation offers the possibility of lower costs per ton mile.
As a result operators often have had to introduce new, or expand existing, transhipment arrangements. Often this has meant establishing transhipment depots, if not fully equipped warehouses.
Where to site the depots is an extremely vital decision for any operator. More difficult still is the decision to accept, when necessary, the unpalatable fact that because of modern developments the present depot is in the wrong place and a new location will have to be found.
Proposed changes In either of these exercises not only has the effect of current developments on roads, rail and vehicle dimensions to be taken into account but also the proposed changes in legal limitations on drivers' hours which will inevitably prescribe the extent or radius of a driver's activity.
Superimposed on the purely transport consideration are changes in the methods of production, marketing and distribution which have a direct bearing on warehousing policy and the types of transport to be employed.
Whether or not a haulier includes warehousing in his services, a new or resited warehouse can be vital to him. New flows of traffic may arise which he can handle: alternatively existing flows may be disrupted or stopped.
It is better for him to be forewarned. An understanding of the modern thinking as to where to site warehouses will be helpful. Still more so if he is himself thinking of setting up a warehouse.
A pamphlet—Planning Warehouse Locations—has just been published and is obtainable free from The National Economic Development Office, Millbank Tower, 21-41 Millbank, London, SW1.
It concisely deals with theoretical and practical aspects and is based on a study of methods of improving efficiency in wholesaling made by a sub-committee of the Distributive Trades Economic Development Council.
It is admitted that management has tended to overlook distribution economies, being pre-occupied with the manufacturing or production process. But there is now evidence of a change of emphasis.
Firms which investigated in detail to find the cheapest and most effective way of distributing goods have achieved substantial economy. Costs of distribution vary for different products and channels of distribution but the total can amount to 40 per cent of retail prices.
The pamphlet sets out the factors which have affected this change of emphasis: including transport infra-structure, pattern of distribution and sale of manufacture.
Additionally the demand for a firm's products may gradually change once the distribution network is decided upon. A greater demand may grow in, say, the Sotith East. Alternatively a product may be sold more and more through larger outlets with the result that fewer deliveries and fewer depots are needed.
After a critical reappraisal management may then realize that warehouses and vehicles are greatly under-utilized. Where delivery vans are kept for convenience or advertising purposes the cost can be very high.
However, it is recognized that judgments will have to be made about the degree of customer service which is profitable. Frequent deliveries and small drops are expensive.
Count the cost
But in a competitive market a manufacturer must count the cost of turning away prospective customers. Not only is the delivery of small orders expensive but the invoicing and collection of small sums frequently costs more than the gross profit on the transaction.
These and similar factors account for the changes in attitude and in practice that are now taking place in distribution and such changes arc affecting everyone in the distribution chain.
As to the action taken by firms to improve, or change the location of their depots, much depends, the pamphlet records, on the degree of service given to the retailer. Different companies have different basic criteria.
The trend The trend has been to reduce the number of warehouses and where possible to set up a central warehouse or warehouses when, within a given area, the location is then relatively unimportant.
Central warehouses tend to be very large and highly automated. But where firms have been able to identify an ideal location for distribution, shortage of available manpower or inability to get planning permission has often prevented its use.
Three examples are given of reduction in the number of depots: from 100 to 46; from 27 to 9 and from 150 to 75. It is pertinently added, however, that there is a difference between the desirable number of warehouses and the degree of change which is immediately feasible.
Direct delivery has brought resultant economy. The eliminating of delivery from branches has proved worth while.
In principle the reduced number of warehouses increases the total mileage travelled—though not necessarily the total cost—and reduces overheads.
Apart from the transport aspect, good location and fewer warehouses can bring economies in stock holding, accounting and other overheads.
Seven case histories are given. These relate to depot locations in wholesale grocery, application of operational research, survey of distribution practices and cost, depot location in the fields of paper products and refrigerated goods, tinned products and the best location of an additional warehouse.
Three main failings In the conclusion three main failings in the distribution function are summarized:
Lack of knowledge of distribution costs; lack of awareness of inter-relationship of production, distribution and marketing (for example: does the sales manager realize what a 24-hour delivery service costs the company?); a tendency to concentrate on one or other aspects of the distribution process (e.g. increasing the number of depots in order to decrease the transport cost).
Examples of areas where a reduction in costs could be made may seem trivially obvious. But there are many cases where the obvious has been overlooked, this report concludes.