1. A 20 per cent cut in tipper payloads
Page 62
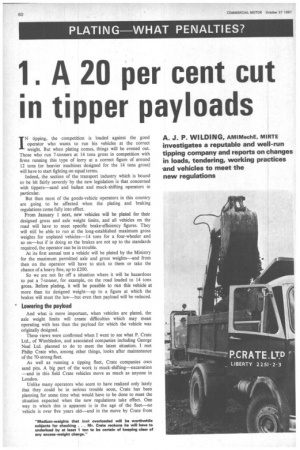
Page 63
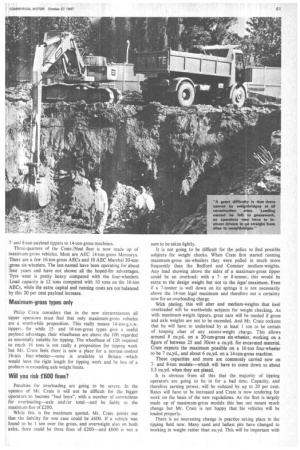
Page 64
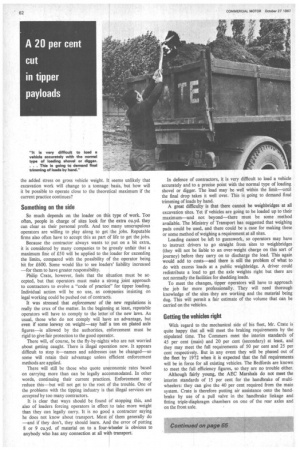
Page 67
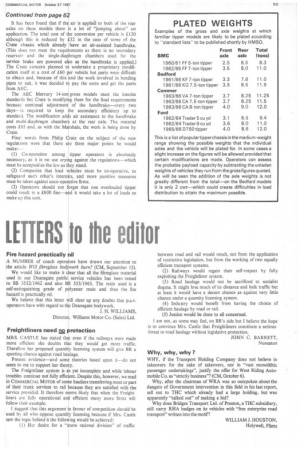
If you've noticed an error in this article please click here to report it so we can fix it.
INT tipping, the competition is loaded against the good operator who wants to run his vehicles at the correct weight. But when plating comes, things will be evened out. Those who run 7-tonners at 14 tons gross in competition with firms running this type of lorry at a correct figure of around 12 tons (or heavier machines designed for the 14 tons gross) will have to start fighting on equal terms.
Indeed, the section of the transport industry which is bound to be hit fairly severely by the new legislation is that concerned with tippers—sand and ballast and muck-shifting operators in particular.
But then most of the goods-vehicle operators in this country are going to be affected when the plating and braking regulations come fully into effect.
From January I next, new vehicles will be plated for their designed gross and axle weight limits, and all vehicles on the road will have to meet specific brake-efficiency figures. They will still be able to run at the long-established maximum gross weights for unplated vehicles-14 tons for a four-wheeler and so on—but if in doing so the brakes are not up to the standards required, the operator can be in trouble.
At its first annual test a vehicle will be plated by the Ministry for the maximum permitted axle and gross weights—and from then on the operator will have to stick to them or take the chance of a heavy fine, up to £200.
So we are not far off a situation where it will be hazardous to put a 7-tonner, for example, on the road loaded to 14 tons gross. Before plating, it will be possible to run this vehicle at more than its designed weight—up to a figure at which the brakes will meet the law—but even then payload will be reduced.
Lowering the payload
And what is more important, when vehicles are plated, the axle weight limits will create difficulties which may mean operating with less than the payload for which the vehicle was originally designed.
These views were confirmed when I went to see what P. Crate Ltd., of Wimbledon, and associated companies including George Neal Ltd. planned to do to meet the latest situation. I met Philip Crate who, among other things, looks after maintenance of the 70-strong fleet.
As well as running a tipping fleet, Crate companies own sand pits. A big part of the work is muck-shifting—excavation —and in this field Crate vehicles move as much as anyone in London.
Unlike many operators who seem to have realized only lately that they could be in serious trouble soon, Crate has been planning for some time what would have to be done to meet the situation expected when the new regulations take effect. One way in which this is apparent is in the age of the fleet—no vehicle is over five years old—and in the move by Crate from 7and 8-ton-payload tippers to 14-ton-gross machines.
Three-quarters of the Crate/Neal fleet is now made up of maximum-gross vehicles. Most are AEC 14-ton-gross Mercurys. There are a few 16-ton-gross AECs and 10 AEC Marshal 20-tongross six-wheelers. The last-named have been operating for about four years and have not shown all the hoped-for advantages. Tyre wear is pretty heavy compared with the four-wheelers. Load capacity is 12 tons compared with 10 tons on the 16-ton AECs, while the extra capital and running costs are not balanced by this 20 per cent payload increase.
Maximum-gross types only
Philip Crate considers that in the new circumstances all tipper operators must find that only maximum-gross vehicles are a worthwhile proposition. This really means 14-ton-g.v.w. tippers. for while 15and 16-ton-gross types give a useful payload advantage, their wheelbases are above the 10ft regarded as essentially suitable for tipping. The wheelbase of 12ft required to reach 16 tons is not really a proposition for tipping work but Mr. Crate feels there is now a place for a normal-control 16-ton four-wheeler—none is available in Britain -----which would have the right length for tipping work and be less of a problem in exceeding axle weight limits.
Will you risk £600 fines?
Penalties for overloading are going to be severe. In the opinion of Mr. Crate it will not be difficult for the bigger operators to become "bad boys", with a number of convictions for overloading—axle and /or total—and be liable to the maximum fine of £200.
While this is the maximum quoted. Mr. Crate points out that the liability for one case could be £600. If a vehicle was found to be 1 ton over the gross, and overweight also on both axles, there could be three fines of £200—and £600 is not a sum to be taken lightly.
It is not going to be difficult for the police to find possible subjects for weight checks. When Crate first started running maximum-gross six-wheelers they were pulled in much more frequently than the Bedford and Commer medium-weights. Any load showing above the sides of a maximum-gross tipper could be an overload: with a 7or 8-tonner, this would be extra to the design weight but not to the legal maximum. Even if a 7-tonner is well down on its springs it is not necessarily above the 14-ton legal maximum and therefore not a certainty now for an overloading charge.
With plating, this will alter and medium-weights that look overloaded will be worthwhile subjects for weight checking. As with maximum-weight tippers, great care will be needed if gross and axle weights are not to be exceeded. And Mr. Crate reckons that he will have to underload by at least 1 ton to be certain of keeping clear of any excess-weight charge. This allows around 8 cu.yd. on a 20-ton-gross six-wheeler, working on a figure of between 25 and 30cwt a cu.yd. for excavated material. Crate expects the maximum possible on a 16-ton four-wheeler to be 7 cu.yd., and about 6 cu.yd. on a 14-ton-gross machine.
These capacities and more are commonly carried now on 7and 8-ton models—which will have to come down to about 5.5 cu.yd. when they are plated.
It is obvious from all this that the majority of tipping operators are going to be in for a bad time. Capacity, and therefore earning power, will be reduced by up to 20 per cent. Rates will have to be increased and Crate is now tendering for work on the basis of the new regulations. As the fleet is largely made up of maximum-gross models this has not meant much change but Mr. Crate is not happy that his vehicles will be loaded properly.
There is an interesting change in practice taking place in the tipping field now. Many sand and ballast pits have changed to working in weight rather than cu.yd. This will be important with the added stress on gross vehicle weight. It seems unlikely that excavation work will change to a tonnage basis, but how will it be possible to operate close to the theoretical maximum if the current practice continues?
Something on the side
So much depends on the loader on this type of work. Too often, people in charge of sites look for the extra cu.yd. they can clear as their personal profit. And too many unscrupulous operators are willing to play along to get the jobs. Reputable firms also often have to accept this as part of life to get the jobs.
Because the contractor always wants to put on a bit extra, it is considered by many companies to be grossly unfair that a maximum fine of £.50 will be applied to the loader for exceeding the limits, compared with the possibility of the operator being hit for £600. Some would like to see loaders' liability increased —for them to have greater responsibility.
Philip Crate, however, feels that the situation must be accepted, but that operators must make a strong joint approach to contractors to evolve a "code of practice" for tipper loading. Individual action will be no use, as companies insisting on legal working could be pushed out of contracts.
It was stressed that enforcement of the new regulations is really the crux of the matter. In the beginning at least, reputable operators will have to comply to the letter of the new laws. As usual, those who do not comply will have an advantage, but even if some leeway on weight—say half a ton on plated axle figures—is allowed by the authorities, enforcement must be rigid to give fair protection to the good operator.
There will, of course, be the fly-by-nights who are not worried about getting caught. There is illegal operation now. It appears difficult to stop it—names and addresses can be changed—so some will retain their advantage unless efficient enforcement methods are applied.
There will still be those who quote uneconomic rates based on carrying more than can be legally accommodated. In other words, continuing their current practices. Enforcement may reduce this—but will not get to the root of the trouble. One of the problems with the tipping industry is that illegal services are accepted by too many contractors.
It is clear that ways should be found of stopping this, and also of loaders forcing operators in effect to take more weight than they can legally carry. It is no good a contractor saying he does not know about transport. Most of them generally do —and if they don't, they should learn. And the error of putting 8 or 9 cu.yd. of material on to a four-wheeler is obvious to anybody who has any connection at all with transport. In defence of contractors, it is very difficult to load a vehicle accurately and to a precise point with the normal type of loading shovel or digger. The load may be well within the limit—until the final drop takes it well over. This is going to demand final trimming of loads by hand. A great difficulty is that there cannot be weighbridges at all excavation sites. Yet if vehicles are going to be loaded up to their maximum—and not beyond—there must be some method available. The Ministry of Transport has suggested that weighing pads could be used, and there could be a case for making these or some method of weighing a requirement at all sites.
Loading cannot be left to guesswork, so operators may have to instruct drivers to go straight from sites to weighbridges (they will not be liable to an over-weight charge on this sort of journey) before they carry on to discharge the load. This again would add to costs—and there is still the problem of what to do with excess loads at a public weighbridge. A driver could redistribute a load to get the axle weights right but there are not normally the facilities for shedding loads.
To meet the changes, tipper operators will have to approach the job far more professionally. They will need thorough knowledge of the sites they are working and the material being dug. This will permit a fair estimate of the volume that can be carried on the vehicles.
Getting the vehicles right
With regard to the mechanical side of his fleet, Mr. Crate is quite happy that all will meet the braking requirements by the stipulated time. The Commers meet the interim standards of 45 per cent (main) and 20 per cent (secondary) at least, and they may meet the full requirements of 50 per cent and 25 per cent respectively. But in any event they will be phased out of the fleet by 1972 when it is expected that the full requirements will be in force for all existing vehicles. The Bedfords are known to meet the full efficiency figures, so they are no trouble either.
Although fairly young, the AEC Marshals do not meet the interim standards of 15 per cent for the handbrake of multiwheelers: they can give the 40 per cent required from the main system. Crate is therefore putting air assistance onto the handbrake by use of a pull valve in the handbrake linkage and fitting triple-diaphragm chambers on one of the rear axles and on the front axle.
It has been found that if thel air is applie-d to both of the rear axles on these models there s a lot of "jumping about" on application. The total cost of the conversion per vehicle is £130 although this is reduced by t 32 in the case of some of the Crate chassis which already have an air-assisted handbrake. (This does not meet the requirements as there is no secondary reservoir and the single-diaphragm chambers used for the service brake are powered alp() as the handbrake is applied.) The Crate concern planned t9 undertake a proprietary modification itself at a cost of £60 per vehicle but parts were difficult to obtain and, because of this and the work involved in bending pipes to suit, it was decided to pay the extra and get the parts from AEC.
The AEC Mercury 14-totl-gross models meet the interim standards but Crate is modifying them for the final requirements because continual adjustment l of the handbrake every two days-is required to keep the secondary efficiency up to standard. The modification adds air assistance to the handbrake and multi-diaphragm chamber'§ at the rear axle. The material costs £85 and, as with the Matshals, the work is being done by Crate.
Final words from Philip Crate on the subject of the new regulations were that there ak.e three major points he would make:-
(1) Co-operation among tipper operators is absolutely necessary, as it is no use eryi4 against the regulations-which must be accepted as the law as they stand.
(2) Companies that load lehieles must be co-operative, to safeguard each other's interets, and more punitive measures must be taken against unco-operative firms.
(3) Operators should not forget that one overloaded tipper could result in a £600 fine-and it would take a lot of loads to make up this sum.