Chemical De-rusting Speeds Reconditioning
Page 105
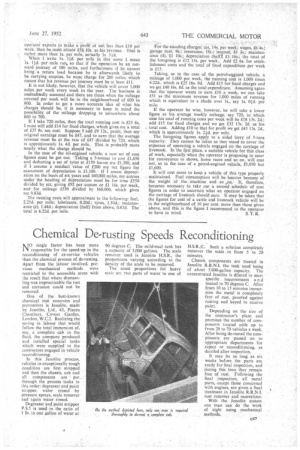
If you've noticed an error in this article please click here to report it so we can fix it.
NO single factor has been more responsible for the speed-up in the reconditioning of ex-service vehicles than the chemical process of de-rusting. Apart from the labour involved, previous mechanical methods were restricted to the accessible areas with the result that where dismantling was impracticable the rust and corrosion could not be removed. .
One of the best-known chemical rust removers and preventives is. Jenolite, made by Jenolite, Ltd., 43, Piazza Chambers, Covent Garden, London, W.C.2. Realizing the saving in labour that would follow the total immersion of, say, a complete cab in the fluid, the company produced and installed special tanks which' were supplied' to the contractors engaged in vehicle reconditioning.
In this Jenolite process, vehicles in exceptionally rough condition are first stripped and then the chassis, cab and all components are put through the process tanks in this order: degreaser and paint stripper, water rinsed by pressure sprays, scale remover and again water rinsed.
Degreaser and paint stripper P.S.5 is used -in the ratio of 1 lb. to one gallon of water at 90 degrees C. The mild=steel tank has a capacity of 3,000 gallons. The scale remover used. is Jenolite H.S.R., the proportions varying according to the density of the scale to be removed.
The usual proportions for heavy scale are two parts of water to one of H.S.R./C. Such a solution completely removes the scale in from 5 to 20 minutes.
Chassis components are treated in
Jenolite the tank used being of about 5,000-gallon capacity. The concentrated Jenolite is diluted to meet specific requirements a n d heated to 70 degrees C. After from 10 to 15 minutes immersion the metal is completely free of rust, proofed against rusting and keyed to receive paint.
Depending on the size of the contractor's plant and premises the number of components treated adds up to from 20 to 70 vehicles a week. After being de-rusted the components are passed on to appropriate departments for repair or reconditioning, as decided after inspection.
It may be as long . as six weeks before the parts are ready for final inspection, and during this time they remain free of rust. Following the final inspection, all metal parts,-except those concerned with engines, are given a final treatment in Jenolite R.R.N.I. rust remover, and neutralizer.
With the Jenolite system one man can do the work of eight using mechanical methods.