B efore the emission laws, engine manufacturers were concentrating on reducing
Page 32
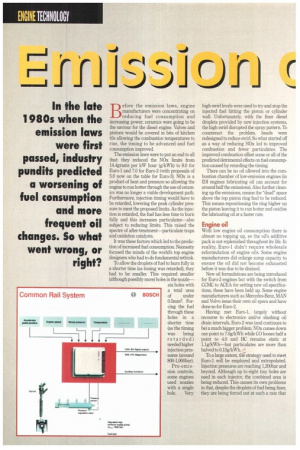
Page 33
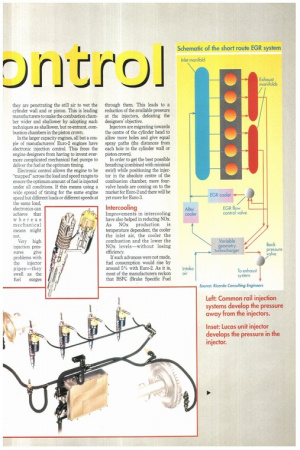
Page 34
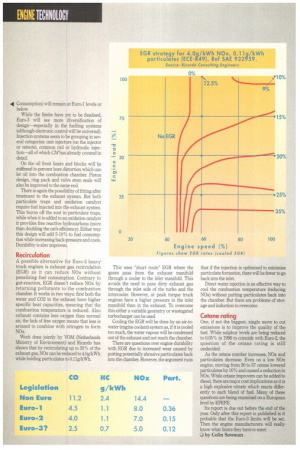
If you've noticed an error in this article please click here to report it so we can fix it.
fuel consumption and increasing power; ceramics were going to be the saviour for the diesel engine. Valves and pistons would be covered in bits of kitchen tile allowing the combustion temperatures to rise, the timing to be advanced and fuel consumption improved.
The emission laws were to put an end to all that: they reduced the NOx limits from 14.4grams per kW hour (g/kWh) to 8.0 for Euro-1 and 7.0 for Euro-2 (with proposals of 5.0 now on the table for Euro-3). NOx is a product of heat and pressure so allowing the engine to run hotter through the use of ceramics was no longer a viable development path. Furthermore, injection timing would have to be retarded, lowering the peak cylinder pressure to meet the proposed limits. As the injection is retarded, the fuel has less time to burn fully and this increases particulates—also subject to reducing limits. This raised the spectre of after-treatment—particulate traps and oxidation catalysts, It was these factors which led to the prediction of increased fuel consumption. Necessity focused the minds of the world's top engine designers who had to do fundamental rethink.
To allow the droplets of fuel to burn fully in a shorter time (as timing was retarded), they had to be smaller. This required smaller (although possibly more) holes in the nozzle— six holes with a total area
of under 0.5mm2. Forcing the fuel through these holes in a shorter time (as the timing was being retarded) needed higher injection pressures (around 800-1,000bar).
Pre-emission controls, some engines used nozzles with a single hole. Very
high swirl levels were used to try and stop the injected fuel hitting the piston or cylinder wall. Unfortunately, with the finer diesel droplets provided by new injection systems, the high swirl disrupted the spray pattern. To counteract the problem, heads were redesigned to reduce swirl. So what started off as a way. of reducing NOx led to improved combustion and fewer particulates. The improved combustion offset some or all of the predicted detrimental effects on fuel consumption caused by retarding the timing.
There can be no oil allowed into the combustion chamber of low-emission engines (in DI engines lubricating oil can account for around half the emissions). Also further cleaning up the emissions, means the "dead" space above the top piston ring had to be reduced. This means repositioning the ring higher up the piston leaving it to run hotter and oxidise the lubricating oil at a faster rate.
Engine oil
With low engine oil consumption there is almost no topping up, so the oil's additive pack is not replenished throughout its life. In reality, Euro-1 didn't require wholesale reformulation of engine oils. Some engine manufacturers did enlarge sump capacity to ensure the oil did not become exhausted before it was due to be drained.
New oil formulations are being introduced for Euro-2 engines but with the switch from CCMC to ACEA for setting new oil specifications, these have been held up. Some engine manufacturers such as Mercedes-Benz, MAN and Volvo issue their own oil specs and have done so for Euro-2.
Having met Euro-1, largely without recourse to electronics and/or slashing oil drain intervals, Euro-2 was (and continues to be) a much bigger problem. NOx comes down one point to 7.0g/kWh while CO looses half a point to 4.0 and HC remains static at 1.1g/kWh—but particulates are more than halved to 0.15g/kWh,
To a large extent, the-strategy used to meet Eui-o-1 will be employed and extrapolated. Injection pressures are reaching 1,200bar and beyond. Although up to eight tiny holes are used in each injector, the combined area is being reduced. This causes its own problems in that, despite the droplets of fuel being finer, they are being forced out at such a rate that
they are penetrating the still air to wet the cylinder wall and or piston. This is leading manufacturers to make the combustion chamber wider and shallower by adopting such techniques as shallower, but re-entrant, combustion chambers in the piston crown.
In the larger capacity engines, all but a couple of manufacturers' Euro-2 engines have electronic injection control. This frees the engine designers from having to invent evermore complicated mechanical fuel pumps to deliver the fuel at the optimum timing.
Electronic control allows the engine to be 'Mapped" across the load and speed ranges to ensure the optimum amount of fuel is injected under all conditions. If this means using a wide spread of timing for the same engine speed but different loads or different speeds at the same load, electronics can achieve that whereas mechanical means might not Very high injection pres sures give problems with the injector pipes—they swell as the fuel surges through them. This leads to a reduction of the available pressure at the injectors, defeating the designers' objective.
Injectors are migrating towards the centre of the cylinder head to allow more holes and give equal spray paths (the distances from each hole to the cylinder wall or piston crown).
In order to get the best possible breathing (combined with minimal swirl) while positioning the injector in the absolute centre of the combustion chamber, more fourvalve heads are coming on to the market for Euro-2 and there will be yet more for Euro-3.
Intercooling
Improvements in intercooling have also helped in reducing NOx. As NOx production is temperature dependent, the cooler the inlet air, the cooler the combustion and the lower the NOx levels—without losing efficiency.
If such advances were not made, fuel consumption would rise by around 5% with Euro-2. As it is, most of the manufacturers reckon that BSFC (Brake Specific Fuel
4 Consumption) will remain at Euro-1 levels or below.
While the limits have yet to be finalised, Euro-3 will see more diversification of design—especially in the fuelling systems (although electronic control will be universal). Injection systems seem to be grouping in several categories: unit injectors (on the injector or remote), common rail or hydraulic injec. tion—all of which CM has already covered in detail.
On the oil front liners and blocks will be stiffened to prevent bore distortion which can let oil into the combustion chamber. Piston design, ring pack and valve stem seals will also be improved to the same end.
There is again the possibility of fitting after treatment to the exhaust system. But both particulate traps and oxidation catalyst require fuel injected into the exhaust system. This burns off the soot in particulate traps, while when it is added to an oxidation catalyst it provides free reactive hydrocarbons (more than doubling the cat's efficiency). Either way this design will add 5-10% to fuel consumption while increasing back-pressure and costs. Durability is also unproven.
Recirculation
A possible alternative for Euro-3 heavy truck engines is exhaust gas recirculation (EGR) as it can reduce NOx without penalising fuel consumption. Contrary to gut-reaction, EGR doesn't reduce NOx by returning pollutants to the combustion chamber. It works in two ways: first both the water and CO2 in the exhaust have higher specific heat capacities, meaning that the combustion temperature is reduced. Also exhaust contains less oxygen than normal air, the lack of free oxygen means that less is around to combine with nitrogen to form NOx.
Work done jointly by VOM (Netherlands Ministry of Environment) and Ricardo has shown that by recirculating up to 35% of the exhaust gas, NOx can be reduced to 4.0g/kWh while holding particulates to 0.11g/kWh.
This uses "short route" EGR where the gases pass from the exhaust manifold through a cooler to the inlet manifold. This avoids the need to pass dirty exhaust gas through the inlet side of the turbo and the intercooler. However, at peak torque truck engines have a higher pressure in the inlet manifold than in the exhaust. To overcome this either a variable geometry or wastegated turbocharger can be used.
Cooling the EGR will be done by an air-towater (engine coolant) system as, if it is cooled too much, the water vapour will be condensed out of the exhaust and not reach the chamber.
There are questions over engine durability with EGR due to increased wear caused by putting potentially abrasive particulates back into the chamber. However, the argument runs that if the injection is optimised to minimise particulate formation, there will be fewer to go back into the inlet.
Direct water injection is an effective way to cool the combustion temperature (reducing NOx) without putting particulates back into the chamber. But there are problems of storage and induction to overcome.
Cetane rating
One, if not the biggest, single move to cut emissions is to improve the quality of the fuel. While sulphur levels are being reduced to 0.05% in 1996 to coincide with Euro-2, the question of the cetane rating is still undecided.
As the cetane number increases, NOx and particulates decrease. Even on a low NOx engine, moving from 50 to 57 cetane lowered particulates by 10% and caused a reduction in NOx. While cetane improvers can be added to diesel, there are major cost implications as it is a high explosive nitrate which reacts differently to each blend of fuel. Many of these questions are being examined on a European level by EPEFE.
Its report is due out before the end of the year. Only after this report is published is it probable that the Euro-3 limits will be set. Then the engine manufacturers will really know what limits they have to meet.
0 by Colin Sowman