A lot of our readers are in the market for
Page 38
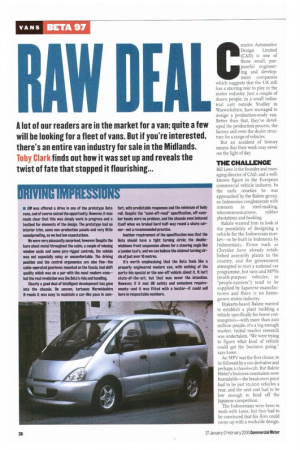
Page 39
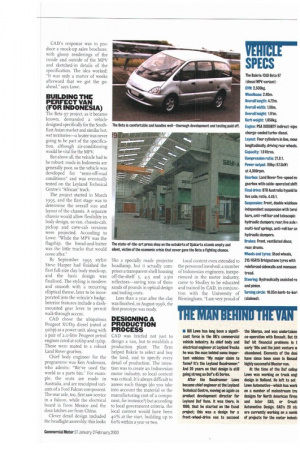
Page 40
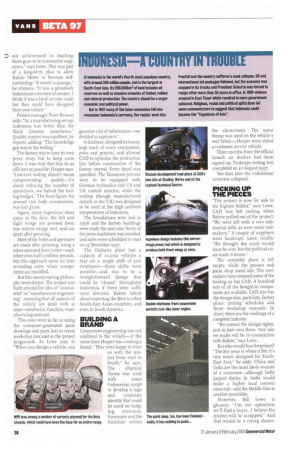
If you've noticed an error in this article please click here to report it so we can fix it.
a van; quite a few will be looking for a fleet of vans. But if you're interested, there's an entire van industry for sale in the Midlands. Toby Clark finds out how it was set up and reveals the twist of fate that stopped it flourishing...
reative Automotive
Design Limited (CAD) is one of those small, purposeful engineering and development companies
which suggests that the UK still has a starring role to play in the motor industry. Just a couple of dozen people, in a small industrial unit outside Studley in Warwickshire, have managed to design a production-ready van. Better than that, they've developed the production process, the factory and even the dealer structure for a range of vehicles.
But an accident of history means that their work may never see the light of day.
THE CHALLENGE
Bill Lowe is the founder and managing director of CAD, and a wellknown figure in the European commercial vehicle industry. In the early nineties he was approached by the Bakrie group, an Indonesian conglomerate with nterests in steel-making,
telecommunications, rubber plantations and banking Bakrie wanted him to look at the possibility of designing a vehicle for the Indonesian market—to be built in Indonesia by Indonesians. Firms such as Chrysler have already established assembly plants in the country, and the government attempted to start a national car programme, but vans and MPVs (multi-purpose vehicles, or "people-carriers") tend to be supplied by Japanese manufacurers and there is no homegrown motor industry.
Djakarta-based Bakrie wanted to establish a plant building a vehicle specifically for home consumption—with more than zoo million people, it's a big enough market. Initial market research was undertaken. "We were trying to figure what kind of vehicle could get the business going," says Lowe.
An MPV was the first choice, to be followed by a van derivative and perhaps a chassis-cab. But Bakrie Motor's business constraints were formidable—the break-even point had to be just ro,000 vehicles a year, and the unit cost had to be low enough to fend off the Japanese competition.
The Indonesians were keen to work with Lowe, but they had to be convinced that his firm could come up with a workable design. CAD's response was to produce a mock-up sales brochure, with glossy renderings of the inside and outside of the MPV and sketched-in details of the specification. The idea worked: "It was only a matter of weeks afterward that we got the goahead," says Lowe.
BUILDING THE PERFECT VAN won INDONESIA)
The Beta 97 project, as it became known, demanded a vehicle designed specifically for the SouthEast Asian market and similar hot, wet territories—a heater was never going to be part of the specificafion, although air-conditioning would be vital for the MPV.
But above all, the vehicle had to be robust: roads in Indonesia are generally poor, so the vehicle was developed for "semi-off-road conditions" and was eventually tested on the Leyland Technical Centre's "African" track.
The project started in March 1995, and the first stage was to determine the overall size and layout of the chassis. A separate chassis would allow flexibility in body design, so van, chassis-cab. pickup and crew-cab versions were projected. According to Lowe: "While the MPV was the flagship, the bread-and-butter was the little trucks that would come after."
By September '995 stylist Steve Harper had finished the first full-size clay body mock-up, and the basic design was finalised. The styling is modern and smooth with a recurring elliptical theme, later to be incorporated into the vehicle's badge. Interior features include a dashmounted gear lever to permit walk-through access.
CAD chose the ubiquitous Peugeot XU D9 diesel (rated at 9ohp) as a power unit, along with a pair of 2.o-litre Peugeot petrol engines rated at ioGhp and I3ihp. These were mated to a robust Land Rover gearbox.
Chief body engineer for the programme was Ken Anderson, who admits: "We've used the world as a parts bin." For example. the seats are made in Australia, and are resculpted variants of a Ford Falcon component. The rear axle, too, first saw service in a Falcon, while the electrical board is from Mexico and the door latches are from China.
Clever detail design included the headlight assembly: this looks like a specially made projector headlamp, but it actually comprises a transparent shell housing off-the-shelf 5, 4.5 and 2.5in reflectors—saving tens of thousands of pounds in optical design and tooling costs.
Less than a year after the clay was finished, in August '996, the first prototype was ready.
DESIGNING A PRODUCTION PROCESS
LAD was briefed not just to design a van, but to establish a production plant. The firm helped Bakrie to select and buy the land, and to specify every detail of production. The intention was to create an Indonesian motor industry, so local content was critical. It's always difficult to assess such things (do you take into account the material or the manufacturing cost of a component. for instance?) but according to local government criteria, the local content would have been 40% at the start, building up to Go% within a year or two. Local content even extended to the personnel involved: a number of Indonesian engineers, inexperienced in the motor industry, came to Studley to be educated and trained by CAD, in conjunction with the University of Birmingham. "I am very proud of
3 our achievement in teaching these guys to be automotive engineers," says Lowe. This was part of a long-term plan to allow Bakrie Motor to become selfsustaining: "It wasn't a quango," he stresses. "It was a genuinely Indonesian commercial project. I think it was a hard 20-year road, but they could have designed their own vehicle."
Project manager Peter Benson adds: "As a manufacturing set-up, Indonesia was better than the Black Country sometimes." Quality control was excellent, he reports, adding: "The knowledge gap was in the tooling."
The factory was to have its own press shop, but to keep costs down it was vital that this be as efficient as possible. Harper says: "Low-cost tooling doesn't mean compromising quality—it's about reducing the number of operations...we halved the tooling budget." The final figure, for around coo body components, was just f12m.
Again, some ingenious ideas came to the fore: the left and right wings are pressed from one mirror-image tool, and cut apart after pressing.
Most of the holes and apertures are made after pressing, using a robot-operated laser cutter—each robot costs half a million pounds, but this approach saves on later re-tooling costs when components are modified.
But this money-saving philosophy went deeper. The project was built around the idea of "concurrent" or "simultaneous engineering", ensuring that all aspects of the vehicle are dealt with at once—aesthetics, function, manufacturing and cost.
This even went as far as using the computer-generated parts drawings and parts lists to create workshop manuals as the project progressed. As Lowe puts it: "When you design a vehicle, you generate a lot of information—we decided to capture it."
A database, designed in-house. kept track of every component. price and process, and allowed CAD to optimise the production line before construction of the factory started. Every detail wa, specified. The Taiwanese presse, were to be equipped wit Ii German hydraulics and US and UK control systems, while the tooling (though manufactured mainly in the UK) was designed to be used in the high ambient temperatures of Indonesia.
The foundations were laid in 1996 and the factory buildings were ready the next year. Some of the press machinery was installed and sales were scheduled to start on 14 December 1997.
The Djakarta plant had capacity of to,000 vehicles a year on a single shift of 300 employees—three shifts were possible—and was to be a straightforward design that could be "cloned" throughout Indonesia if there were sufficient demand. Bakrie talked about exporting the Beta to other South-East Asian countries, and even to South America.
BUILDING A BRAND
Concurrent engineering was not confined to the vehicle—at the same time Harper was creating a brand: "They were happy to trust us with the project from start to finish," he says.
The elliptical theme was used with some Indonesian script to develop a logo and corporate identity that could be used on badging, stationery, forecourts and the furniture within the showrooms. The same theme was used on the vehicle's seat fabric—Harper even styled a customer service vehicle.
Three months from the official launch 20 dealers had been signed up. Prototype testing was completed on to August 1997.
Ten days later the Indonesian economy collapsed.
PICKING UP THE PIECES
"The project is now for sale to the highest bidder," says Lowe. CAD was left reeling when Bakrie pulled out of the project: "We were left with a very substantial debt, as were some toolmakers." A couple of suppliers went bankrupt. Lowe recalls: "We thought the crash would soon be over, but the political crisis made it worse."
The assembly plant is left empty, while the presses and paint shop stand idle. The toolmakers have retained some of the tooling, as has CAD. A hundred sets of all the bought-in components are available. CAD also has the design data, parts lists, factory plans, pricing schedules and those workshop manuals. In short, there are the makings of a complete industry.
"We control the design rights, and in part own them. Any sale we make will be in conjunction with Bakrie," says Lowe.
But who would buy the project? "The key issue is where it fits: it's very much designed for SouthEast Asia," he adds. China and India are the most likely sources of a customer—although hefty import duties in India would make a higher local content essential—and the Middle East is another possibility.
However, Bill Lowe is gloomy: "I'm not optimistic we'll find a buyer.. .1 believe the project will be scrapped." And that would be a crying shame.