Break with Bodybuilding Tradition
Page 30
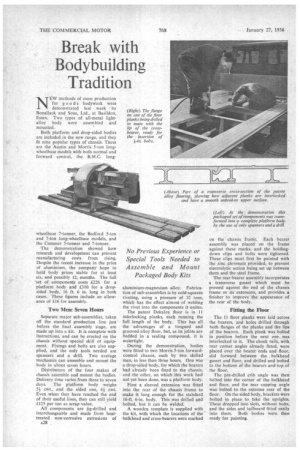
If you've noticed an error in this article please click here to report it so we can fix it.
NEW methods of mass production for goods bodywork were demonstrated last . week by Bonallack and Sons, Ltd., at Basildon, Essex. Two types of all-metal lightalloy body were assembled and mounted.
Both platform and drop-sided bodies are included in the new range, and they fit nine popular types of chassis. These are the Austin and Morris 5-ton longwheelbase models with both normal and forward control, the B.M.C. long wheelbase 7-tonner, the Bedford 5-ton and 7-ton long-wheelbase models, and the Commer 5-tonner and 7-tanner.
The demonstration showed how research and development can prevent manufacturing costs from rising. Despite the recent increase in the price of aluminium, the company hope to hold body prices stable for at least six, and possibly 12, months. The full set of components costs £226 for a platform body and £.310 for a dropsided body, 16 ft. 6 in. long in both cases. These figures include an allowance of 16 for assembly.
Two Men: Seven Hours
Separate major sub-assemblies, taken off the standard production line just before the final assembly stage, are made up into a kit. It is complete with instructions, and can be erected on the chassis without special skill or equipment. Fixings and bolts are also supplied, and the only tools needed are spanners and a drill. Two average mechanics can assemble and mount the body in about seven hours.
Distributors of the four makes of chassis assemble and mount the bodies. Delivery time varies from three to seven days. The platform body weighs 5* cwt., and the sided one, 61 cwt. Even when they have reached the end of their useful lives, they can still yield 125 per ton as scrap value.
All components are jig-drilled and interchangeable and made from heattreated non-corrosive extrusions of A28 aluminium-magnesium alloy. Fabrication of sub-assemblies is by cold-squeeze riveting, using a pressure •of 32 tons, which has the effect almost of welding the rivet into the components it unites.
The patent Dekaloy floor is in 11 interlocking planks, each running the full length of the body. This has all the advantages of a tongued and grooved alloy floor, but, as its joints are bedded in a sealing compound, it is watertight.
During the demonstration, bodies were fitted to two Morris 5-ton forwardcontrol chassis, each by two skilled men, in less than three hours. One was a drop-sided body, for which the bearers had already been fixed to the chassis, and the other, on which this work had not yet been done, was a platform body.
First a sleeved extension was fitted into the rear of the chassis frame to make it long enough for the standard I6-ft. 6-in. body. This was drilled and bolted, but it can be welded.
A wooden template is supplied with the kit, with which the locations of the bulkhead and cross-bearers were marked
on the chassis frame. Each bearer assembly was placed on the frame against these marks, and the holdingdown clips and bolts were tightened. These clips must first be painted with the zinc chromate provided, to prevent electrolytic action being set up between them and the steel frame.
The rear-bearer assembly incorporates a transverse gusset which must be pressed against the end of the chassis frame or its extension, and provides a finisher to improve the appearance of the rear of the body.
Fitting the Floor The 11 floor planks were laid across the bearers, and holes drilled through both flanges of the planks and the lips of the bearers. Each plank was bolted in position before the next one was interlocked to it. The chock rails, with rear corner angles already fitted, were placed over the bearer ends and floor, slid forward between the bulkhead gusset and floor, and drilled and bolted to the bottom of the bearers and top of the floor.
The pre-drilled crib angle was then bolted into the corner of the bulkhead and floor, and the rear capping angle was bolted to the extreme rear of the floor. On the sided body, brackets were bolted in place to take the uprights. These dropped into slots, without bolts, and the sides and tailboard fitted easily into them. Both bodies were then ready for painting.