Multi-axled flatbed trucks with loading cranes normally shift building materials
Page 40
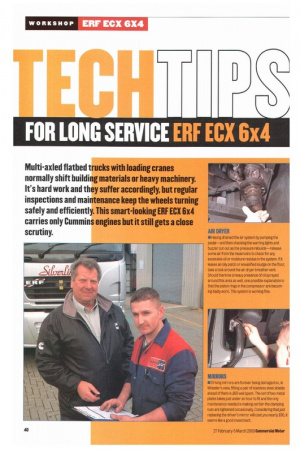
Page 41
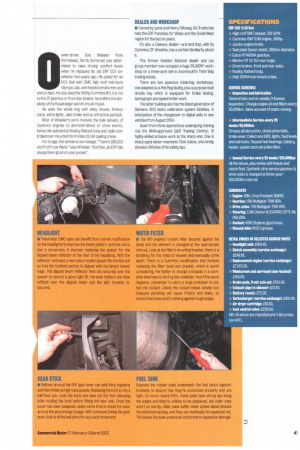
Page 42
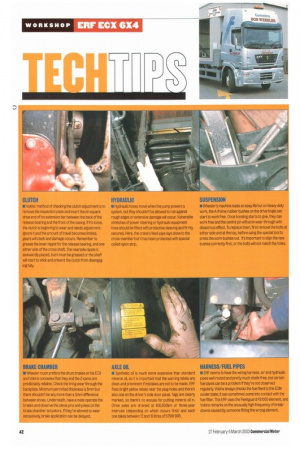
If you've noticed an error in this article please click here to report it so we can fix it.
or heavy machinery. It's hard work and they suffer accordingly, but regular inspections and maintenance keep the wheels turning safely and efficiently. This smart-looking ERF ECX 5x4 carries only Cummins engines but it still gets a close scrutiny.
AIR DRYER • Having drained the air system by pumping the pedal—and then checking the warning lights and buzzer cut-out as the pressure rebuiids—release some air from the reservoirs to check for any excessive oil or moisture residue in the system. if it leaves an oily patch or emulsified sludge on the floor. take a look around the air dryer breather vent. Should there be a heavy presence of oil sprayed around this area as well, one possible explanation is that the piston rings in the compressor are becoming badly worn. This system is working fine.
MIRRORS • Driving mirrors are forever being damaged so, in Wheeler's view, fitting a pair of stainless steel shields ahead of them is 160 well spent. The set of two metal plates takes just under an hour to fit and the only maintenance needed is making certain the clamping nuts are tightened occasionally. Considering thatjust replacing the driver's mirror will cost you nearly £90, it seems like a good investment. HEADLIGHT • These later SMC cabs can benefit from a small modification on the headlights to improve the beam pattern, and this one is due a conversion, It involves replacing the spacer for the dipped beam reflector at the rear of the headlamp. With the reflector removed, a new colour-coded spacer fits into the unit so that the toothed section is aligned with the lamp's lowest edge. The dipped beam reflector then sits securely over the spacer to ensure a good tight fit. Harness holders are then refitted over the dipped beam and the light housing resecured.
GEAR STICK • Bellows around the ERF gear lever can split fairly regularly and then inflate at high road speeds. Replacing the boot is only a half-hour job; undo the knob and take out the four clamping bolts holding the boot before fitting the new one. Once the cover has been swapped, spare some time to check for wear around the gearchange linkage. With someone jinking the gear lever, look at all the ball joints for any slack movement. WATER FILTER • The M11 engine's coolant fitter secures against the block and the element is changed at the appropriate interval. Look at the filter's mounting bracket: there is a tendency for the metal to weaken and eventually come apart. There is a Cummins modification that involves replacing the filter head and bracket, which is worth considering. Far better to change a bracket in a workshop than have to do it by the roadside—but if the worst happens, remember to carry a large container to collect the coolant. Check the coolant hoses closely too: insecure plumbing will cause friction and leaks, so ensure the hoses aren't rubbing against rough edges.
FUEL TANK Examine the robber pads underneath the fuel tank's support brackets to ensure that they're positioned properly and are tight. On more recent ERFs, these pads have strong lips along the edges and they're unlikely to be displaced, but older ones aren't so sturdy. Older pads suffer when spilled diesel attacks the adhesive backing, and they can eventually be squeezed out. This leaves the tank unsecured and prone to expensive damage.
CLUTCH
Vokins' method of checking the clutch adjustment is to remove the inspection plate and insert theAn square drive end of his extension bar between the back of the release bearing and the front of the casing. VA's loose, the clutch is beginning to wear and needs adjustment Ignore it and the amount of travel becomes limited, gears will clash and damage occurs. Remember to grease the inner nipple for the release bearing, and one either side of the cross shaft. The nearside nipple is awkwardly placed, but it must be greased or the shaft will start to stick and prevent the clutch from disengaging fully
HYDRAULIC
• Hydraulic hoses move when the pump powers a system, but they shouldn't be allowed to rub against rough edges or extensive damage will occur. Vulnerable stretches of power steering or hydraulic equipment hose should be fitted with protective sleeving and firmly secured, Here, the crane's feed-pipe lays close to the cross-member but it has been protected with special coiled nylon strip.
SUSPENSION
• Wheeler's machine leads an easy life but on heavy-duty work, the A-frame rubber bushes on the drive bogie can start to work free, Once bonding starts to give, they can work free and the centre pin will soon wear through with disastrous effect. To replace them, first remove the bolts at either side and at the top, before using the special tool to press the worn bushes out. It's important to align the new bushes correctly first, or the hafts will not match the holes.
BRAKE CHAMBER
III Wheeler much prefers the drum brakes on his ECX and Vokins concedes that they and the Z-cams are predictably reliable, Check the lining wear through the backplate. Minimum permitted thickness is 5mm but there shouldn't be any more than a 3mm difference between shoes. Underneath, have a mate operate the brakes and observe the clevis pins and yokes on the brake chamber actuators. If they're allowed to wear excessively, brake application can be delayed.
AXLE OIL
• Synthetic oil is much more expensive than standard mineral oil, so it is important that the warning labels are clean and prominent if mistakes are not to be made. ERF fixes bright yellow labels near the plug-holes and there's also one on the driver's side door panel. Tags are clearly marked, so there's no excuse for putting mineral oil in. Drive axles are drained at 400,000km or three-year intervals (depending on which occurs first) and each one takes between 12 and 15 litres of 575W 90R.
HARNESS/FUEL PIPES
• ERF seems to have the wiring harness, air and hydraulic pipes well routed and pretty much chafe-free, but certain fuel pipes can be a problem if they're not observed regularly. Vokins always checks the fuel feed to the ECM cooler plate; it can sometimes come into contact with the fuel filter. This ERF uses the Reetguard FS1000 element, and Vokins remarks on the unusually high frequency of breakdowns caused by someone fitting the wrong element.