road and workshop
Page 37
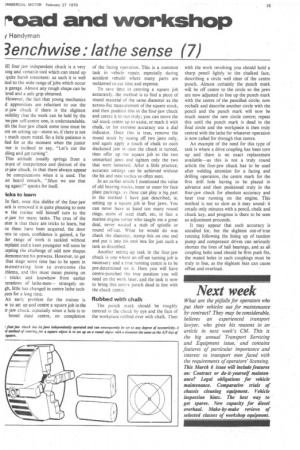
If you've noticed an error in this article please click here to report it so we can fix it.
,t Handyman
3enchwise: lathe sense (7)
IE four-jaw independent chuck is a very ong and versatile tool Which can stand up quite harsh treatment: us such it is well ited to the wide range of jobs which occur a garage. Almost any rough shape can be ired and a safe grip obtained.
However, the fact that young mechanics d apprentices are reluctant to use the Jr-jaw chuck if there is the slightest ssibility that the work can be held by the 'ft-jaw self-centre one, is understandable. ith the four-jaw chuck some time must be ent on setting up—more so, if there is not ) Much spare metaL So a little patience is lied for at the moment when the junior .ner is inclined to say, "Let's cut the tiling and get turning".
This attitude usually springs from a xture of inexperience and distrust of the ar-jaw chuck, in that there always appear be complications when it is used. The .en heard remark, "Must we use that ng again?" speaks for itself.
icks to learn In fact, once this dislike of the four-jai uck is removed it is quite pleasing to note w the trainee will himself turn to the ir-jaw for many tasks. The crux of the itter is that there are tricks to learn, but ce these have been acquired, the door ms to open, confidence is gained, a far Jer range of work is tackled without mplaint and a keen youngster will soon be 2epting the challenge of odd new shapes demonstrate his prowess. However, to get that stage some time has to be spent in monstrating how to overcome the )blems, and this must mean passing on
tricks and knowhow from earlier ierations of lathe-men— strangely engh, little has changed in centre lathe techrues for a long time.
An early problem for the trainee is w to set up and centre a square job in the ii-jaw chuck, especially when a hole is to bored dead centre, on completion of the facing operation. This is a common task in vehicle repair, especially during accident rebuild where many parts are reclaimed to cut time and expense.
To save time in centring a square job accurately, the method is to find a piece of round material of the same diameter as the across-flat measurement of the square stock, and then position this in the four-jaw chuck and centre it to run truly; you can move the tail stock centre up to assist, or mark it with chalk, or for extreme accuracy use a dial indicator. Once this is true, remove the round stock by easing off two jaws only, and again apply a touch of chalk to each slackened jaw in case the chuck is turned, then offer up the square job to the two unmarked jaws and tighten only the two that were loosened. After a little practice, accurate settings can be achieved without the hit and miss tactics so often seen.
In an earlier article 1 mentioned the value of old bearing tracks, inner or outer for face plate packings, as these can play a big part in the method I have just described, ie, setting up a square job in four jaws. You can never have at hand too many round rings, stubs of steel shaft, etc, in fact a marine engine turner who taught me a great deal, never wasted a stub of spindle or round off-cut. What he would do was check the diameter, stamp this on one end and put it into his tool box for just such a task as described.
Another setting-up task in the four-jaw chuck is one where an off-set turning job is necessary and a true running centre is to be pre-determined on it. Here you will have centre-punched the true position you will need on the work later, and the task is now to bring this centre punch dead in line with the chuck centre.
Rubbed with chalk The punch mark should be roughly centred in the chuck by eye and the face of the workpicce rubbed over with chalk. Then with the work revolving you should hold a sharp pencil lightly to the chalked face, describing a circle well clear of the centre punch. Almost certainly the punch mark will be off centre to the circle so the jaws are now adjusted to line up the punch mark with the centre of the pencilled circle; now rechalk and describe another circle with the pencil and the punch mark will now be much nearer the new circle centre; repeat this until the punch mark is dead in the final circle and the workpiece is then truly central with the lathe for whatever operation is now called for through that centre.
An example of the need for this type of task is where a drive coupling has been torn up and there is no exact replacement available—as this is not a truly round article the four-jaw chuck has to be used after welding attention for a facing and drilling operation, the centre mark for the first drill hole having to be placed in advance and then positioned truly in the four-jaw chuck for absolute accuracy and later true running on the engine. This method is not so slow as it may sound: it entails only minutes with a pencil, chalk and chuck key, and progress is there to be seen as adjustment proceeds.
It may appear that such accuracy is uncalled for, but the slightest out-of-true running following the lining up of tandem pump and compressor drives can seriously shorten the lives of ball bearings, and as all coupling bolts used should be firm push fits, the mated holes in such couplings must be truly in line, as the slightest bias can cause offset and overload.