container
Page 29
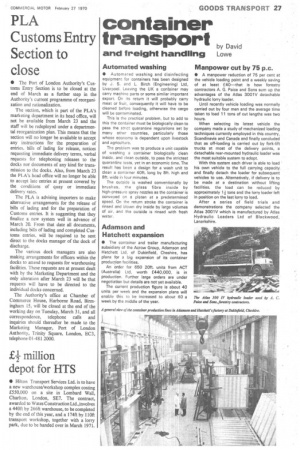
If you've noticed an error in this article please click here to report it so we can fix it.
transport by David and freight handling Lowe
Automated washing
• Automated washing and disinfecting equipment for containers has been designed by J. S. and L. Birch (Engineering) Ltd, Liverpool. Leaving the UK a container may carry machine parts or some similar important export. On its return it will probably carry meat or fruit, consequently it will have to be cleaned before loading, otherwise the cargo will be contaminated.
This is the practical problem, but to add to this the container must be biologically clean to pass the strict quarantine regulations set by many other countries, particularly those whose economy is dependent upon livestock and agriculture.
The problem was to produce a unit capable of washing a container biologically clean inside, and clean outside, to pass the strictest quarantine tests, yet in an economic time. The result has been a design for a wash unit to clean a container 40ft. long by 8ft. high and 8ft. wide in four minutes.
The outside is washed conventionally by brushes, the glass fibre inside by high-pressure spray nozzles as the container is conveyed on a platen at a predetermined speed. On the return stroke the container is rinsed and blown dry inside by large volumes of air, and the outside is rinsed with fresh water.
Adamson and Hatchett expansion
• The container and trailer manufacturing subsidiary of the Acrow Group, Adamson and Hatchett Ltd, of Dukinfieid, Cheshire, has plans for a big expansion of its container production facilities.
An order for 650 20ft. units from ACT (Australia) Ltd, worth £440,000, is in production. Further large orders are under negotiation but details are not yet available.
The current production figure is about 40 units per week and the expansion plans will enable this to be increased to about 60 a week by the middle of the year.
Manpower cut by 75 p.c.
• A manpower reduction of 75 per cent at the vehicle loading point and a weekly saving of at least f40—that is how forestry contractors A. G. Paice and Sons sum up the advantages of the Atlas 3001V detachable hydraulic lorry loader.
Until recently vehicle loading was normally carried out by four men and the average time taken to load 11 tons of cut lengths was two hours.
When selecting its latest vehicle the company made a study of mechanized loading techniques currently employed in this country, Scandinavia and Canada and finally concluded that as off-loading is carried out by fork-lift trucks at most of the delivery points, a detachable rear-mounted hydraulic loader was the most suitable system to adopt.
With this system each driver is able to load his own vehicle to the full carrying capacity and finally detach the loader for subsequent vehicles to use. Alternatively, if delivery is to be made at a destination without lifting facilities, the load can be reduced by approximately 1:I, tons and the lorry loader left in position on the last lorry to load.
After a series of field trials and demonstrations the company selected the Atlas 3001V which is manufactured by Atlas Hydraulic Loaders Ltd of Blackwood, Lanarkshire.