Surface Hardening by Electrical Induction
Page 34
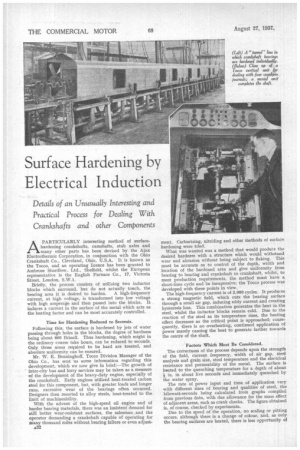
Page 35
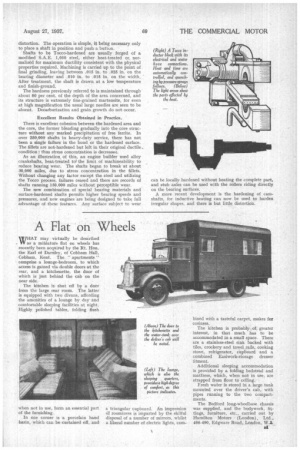
If you've noticed an error in this article please click here to report it so we can fix it.
Details of an Unusually interesting and Practical Process for Dealing With Crankshafts and other Components APARTICULARLY interesting method of surfacehardening crankshafts, camshafts, stub axles and many other parts has been devised by the Ajax Electrothermic Corporation, in conjunction with the Ohio Crankshaft Co., Cleveland, Ohio, U.S.A. It is known as the Tocco, and an operating licence has been granted to Ambrose Shardlow, Ltd., Sheffield, whilst the European representative is the English Furnace Co., 17, Victoria Street, London, S.W.I.
Briefly, the process consists of utilizing two inductor blocks which surround, but do not actually touch, the bearing area it is desired to harden. A high-frequency current, at high voltage, is transformed into low voltage with high amperage and then passed into the blocks. It induces a current in the surface of the metal which acts as the beating factor and can be most accurately controlled.
Time for Hardening Reduced to Seconds.
Following this, the surface is hardened by jets of water passing through holes in the blocks, the degree of hardness being about 600 Brinell. Thus hardening, which might in the ordinary course take hours, can be reduced to seconds. Only those areas required to be hard are treated, and absolute uniformity can be ensured.
Mr. W. E. Benninghoff, Tocco Division Manager of the Ohio Co., has sent us some information regarding this development, which we now give in brief:—The growth of inter-city bus and lorry services may be taken as a measure of the development of the heavy-duty engine, especially of the crankshaft. Early engines utilized heat-treated carbon steel for this component, but, with greater loads and longer runs, excessive wear of the bearings often occurred. Designers then resorted to alloy steels, heat-treated to the limit of machineability.
With the advent of the high-speed oil engine and of harder bearing materials, there was an insistent demand for still better wear-resistant surfaces, the salesman and the operator demanding a crankshaft capable of operating for many thousand miles without bearing failure or even adjust a.32 ment. Carburizing, nitriding and other methods of surface hardening were tried. What was wanted was a method that would produce the desired hardness with a structure which would withstand wear and abrasion without being subject to flaking. This must be accurate as to control of the depth, width and location of the hardened area and give uniformity from bearing to bearing and crankshaft to crankshaft, whilst, to meet production requirements, the method must have a short-time cycle and be inexpensive; the Tocco process was developed with these points in view. The high-frequency current is of 2,000 cycles. It produces a strong magnetic field, which cuts the bearing surface through a small air gap, inducing eddy current and creating hysteresis loss. This combination generates the heat in the steel, whilst the inductor blocks remain cold. Due to the reaction of the steel as its temperature rises, the heating effect decreases as the critical point is approached; consequently, there is no overheating, continued application of power merely causing the heat to generate farther towards the centre of the shaft.
Factors Which Must Be Considered.
The correctness of the process depends upon the strength of the field, current frequency, width of air gap, steel analysis and grain size, steel temperature and the electrical resistance and permeability of the metal. The surface is heated to the quenching temperature for a depth of about in. in about five seconds and immediately quenched by the water spray. The rate of power input and time of application vary with different sizes of bearing and qualities of steel, the kilowatt-seconds being calculated from graphs compiled from previous data, with due allowance for the mass effect of adjacent areas, such as crank cheeks. The figure obtained is, of course, checked by experiments.
Due to the speed of the operation, no scaling or pitting occurs, although there is a change of colour, and, as only the bearing surfaces are heated, there is less opportunity of
distortion. The operation is simple, it being necessary only to place a shaft in position and push a button.
Shafts to be Tocco-hardened are usually forged of a modified S.A.E. 1,050 steel, either heat-treated or, normalized for maximum ductility consistent with the physical properties required. Machining is carried up to the point of final grinding, leaving between .015 in. to .025 in. on the bearing diameter and .010 in. to .015 in. on the width. After treatment, the shaft is drawn at a low temperature and finish-ground.
The hardness previously referred to is maintained through about 80 per cent, of the depth of the area concerned, and its structure is extremely fine-grained martensite, for even at high magnification the usual large needles are seen to be absent_ Decarburization and grain growth do not occur.
Excellent Results Obtained in Practice.
There is excellent cohesion between the hardened area and the core, the former blending gradually into -the core structure without any marked precipitation of free ferrite. In over 250,000 shafts in heavy-duty service, there has not been a single failure in the bond or the hardened surface. The fillets are not hardened but left in their original ductile. condition; thus stress concentration is decreased.
As an illustration. of this, an engine builder used alloy crankshafts, heat-treated to the limit of machineability to reduce bearing wear. The shafts began to break at about 30,000 miles, due to stress concentration in the fillets. Without changing any factor except the steel and utilizing the Tocco process, failures ceased and there are records of shafts running 150,000 miles without perceptible wear.
The new combination of special bearing materials and surface-hardened shafts permits higher bearing speeds and pressures, and new engines are being designed to take full advantage of these features. Any surface subject to wear
can be locally hardened without heating the complete past, and stub axles can be used with the rollers riding directly on the bearing surfaces.
A more recent development is the hardening of camshafts, for inductive heating can now be used to harden irregular shapes, and there is but little distortion.