1.CONTAINERS
Page 64
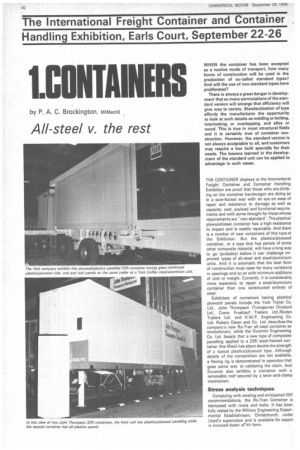
Page 65
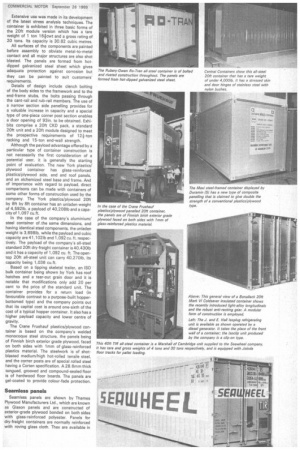
Page 66
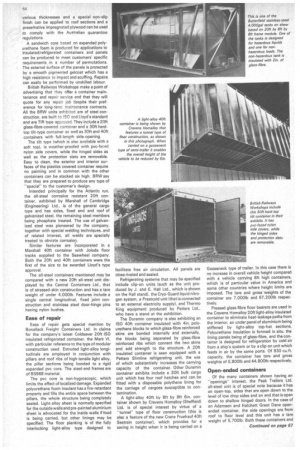
Page 77
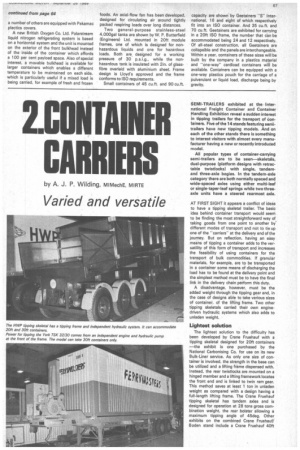
If you've noticed an error in this article please click here to report it so we can fix it.
by P. A. C. Brockington, MIMechE
All-steel v. the rest
WHEN the container has been accepted as a routine mode of transport, how many forms of construction will be used in the production of so-called standard types? And will the use of non-standard types have proliferated?
There is always a great danger in development that so many permutations of the standard version will emerge that efficiency will give way to variety. Standardization of type affords the manufacturer the opportunity to look at such details as welding or bolting, interlocking or overlapping, and alloy or wood. This is true in most structural fields and it is certainly true of container construction. However, the standard version is not always acceptable to all, and customers may require a box built specially for their needs. The lessons learned in the development of the standard unit can be applied to advantage in such cases.
THE CONTAINER displays at the International Freight Container and Container Handling Exhibition are proof that those who are climbing on the container bandwagon are doing so in a sure-footed way with an eye on ease of repair and resistance to damage as well as capacity, cost, payload and functional requirements and with some thought for those whose requirements are "non-standard". The plastics/ plywood/steel container has a high resistance to impact and is readily repairable. And there is a number of new containers of this type at the Exhibition. But the plastics/plywood container, or a type that has panels of some other composite material, will have a long way to go (probably) before it can challenge improved types of all-steel and steel/aluminium units. And it is axiomatic that the best form of construction must cater for many variations in openings and so on with minimum additions of cost or weight. Currently, it is considerably more expensive to repair a steel/aluminium container than one constructed entirely of steel.
Exhibitors of containers having plastics/ plywood panels include the York Trailer Co. Ltd., John Thompson (Transporter Division} Ltd., Crane Fruehauf Trailers Ltd./Boden Trailers Ltd. and H.W.P. Engineering Co. Ltd. Rubery Owen and Co. Ltd. describes the company's new Ro-Tran all-steel container as revolutionary, while the Duramin Engineering Co. Ltd. boasts that a new type of composite panelling applied to a 20ft steel-framed container (the Maxi} has about double the strength of a typical plastics/plywood type. Although details of the composition are not available, a flexing rig is demonstrated in operation that goes some way to validating the claim. And Duramin also exhibits a container with a removable roof secured by a lever-and-clamp mechanism.
Stress analysis techniques
Complying with existing and anticipated ISO recommendations. the Ro-Tran Container is fabricated with rivets and bolts. It has been fully tested by the Military Engineering Experimental Establishment. Christchurch, under Lloyd's supervision and is available for export is knocked-down or kit form.
Extensive use was made in its development of the latest stress analysis techniques. The container is exhibited in three basic forms of the 20ft module version which has a tare weight of 1 ton 1 6-icwt and a gross rating of 20 tons. Its capacity is 30.82 cubic metres.
All surfaces of the components are painted before assembly to obviate metal-to-metal contact and all major structures are also shot blasted. The panels are formed from hotdipped galvanized steel sheet which gives adequate protection against corrosion but they can be painted to suit customers' requirements.
Details of design include clench bolting of the body sides to the framework and to the end-frame stubs, the bolts passing through the cant-rail and rub-rail members. The use of a narrow section side panelling provides for a valuable increase in capacity and a special type of one-piece corner post section enables a door opening of 93in. to be obtained. Exhibits comprise a 20ft CKD pack, a standard 20ft unit and a 20ft module designed to meet the prospective requirements of 124-ton racking and 15-tan end-wall strength.
Although the payload advantage offered by a particular type of container construction is not necessarily the first consideration of a potential user, it is generally the starting point of evaluation. The new York plastics/ plywood container has glass-reinforced plastics/plywood side, end and roof panels, and an alchemized steel base and frame. And of importance with regard to payload, direct comparisons can be made with containers of some other forms of construction used by the company. The York plastics/plywood 20ft by 8ft by 8ft container has an unladen weight of 4,5921b, a payload of 40,2081b and a capacity of 1,097 cu.ft.
In the case of the company's aluminium/ steel container of the same dimensions, and having identical steel components, the unladen weight is 3,6981b, while the payload and cubic capacity are 41,1 02Ib and 1.092 Cu. ft. respectively. The payload of the company's all-steel standard 20ft dry-freight container is 40.4301b and it has a capacity of 1,092 Cu. ft. The opentop 20ft all-steel unit can carry 40,270Ib, its capacity being 1,036 cu.ft.
Based on a tipping skeletal trailer. an ISO bulk container being shown by York has roof hatches and a tear-out grain door and it is notable that modifications only add 20 per cent to the price of the standard unit. The container provides for a return load (in favourable contrast to a purpose-built hopperbottomed type) and the company points out that its capital cost is around one-sixth of the cost of a typical hopper container. It also has a higher payload capacity and lower centre of gravity.
The Crane Fruehauf plastics/plywood container is based on the company's welded monocoque steel structure, the panels being of Finnish birch exterior grade plywood, faced on both sides with 1mm of glass-reinforced plastics material. The steelwork is of shotblasted medium/high hot-rolled tensile steel, and the corner posts are of special rolled steel having a Corten specification. A 28.6mm thick tongued, grooved and compound-sealed floor is of hardwood floor boards. The panels are gel-coated to provide colour-fade protection.
Seamless panels
Seamless panels are shown by Thames Plywood Manufacturers Ltd.. which are known as Glason panels and are constructed of exterior-grade plywood bonded on both sides with glass-reinforced polyester. Panels for dry-freight containers are normally reinforced with roving glass cloth. They are available in various thicknesses and a special non-slip finish can be applied to roof sections and a preserVative impregnated plywood can be used to comply with the Australian quarantine regulations.
A sandwich core based on expanded polyurethane foam is produced for applications to insulated/refrigerated containers and panels can be produced to meet customers' specific requirements in a number of permutations. The external surface of the panels is protected by a smooth pigmented gelcoat which has a high resistance to impact and scuffing. Repairs can easily be performed by unskilled labour.
British Railways Workshops make a point of advertising that they offer a container maintenance and repair service and that they will quote for any repair job despite their preference for long-term maintenance contracts. All the BRW units exhibited are of steel construction, are built to !SO and Lloyd's standard and are TIR type approved. They include a 20ft glass-fibre-covered container and a 30ft hardtop tilt-type container as well as 30ft and 40ft containers with full-length side-opening.
The tilt type (which is also available with a soft top), is weather-proofed with pvc-faced nylon side covers, while the hinged sides as well as the protection slats are removable. Easy to clean, the exterior and interior surfaces of the plastics covered container require no painting and in common with the other containers can be stacked six high. RAW say that they are prepared to produce any type of "specialto the customer's design.
Intended principally for the Atlantic run. the all-steel corrosive resistant 20ft container, exhibited by Marshall of Cambridge (Engineering) Ltd., is of the general cargo type and has sides, fixed end and roof of galvanized steel, the remaining steel members being phosphate treated. The use of galvanized steel was pioneered by the company, together with special welding techniques, and of related interest, all welds are specially treated to obviate corrosion.
Similar features are incorporated in a Marshall 40ft container with Joloda floor tracks supplied to the Seawheel company. Both the 20ft and 40ft containers were the first of the size to be awarded Lloyd's type approval The all-steel containers mentioned may be compared with a new 20ft all-steel unit displayed by the Central Containers Ltd., that is of stressed-skin construction and has a tare weight of under 4,0001b. Features include a single central longitudinal, fixed joint construction and stainless steel door-hinge pins having nylon bushes.
Ease of repair
Ease of repair gets special mention by Bonallack Freight Containers Ltd. in claims for the company's latest Coldsaver 20ft ISO insulated refrigerated container, the Mark VI, with particular reference to the type of modular construction used. Extruded light-alloy longitudinals are employed in conjunction with pillars and roof ribs of high-tensile light alloy. the pillar sections being bonded to a rigid expanded pvc core. The steel-end frames are of 13S968 material.
The pvc core is non-hygroscopic, which limits the effect of localized damage. Expanded polyurethane foam insulant has a fire-retardant property and fills the entire space between the pillars, the whole structure being completely sealed. Light-alloy sheet is normally specified for the outside walls and pre-painted aluminium sheet is advocated for the inside walls if food is being carried, but other linings may be specified. The floor planking is of the fully interlocking light-alloy type designed tc facilitate free air circulation. All panels are close riveted and sealed, Refrigerating systems that may be specified include clip-on units such as the unit produced by J. and E. Hall Ltd., which is shown on the Hall stand), the Cryo-Guard liquid nitrogen system, a Prestcold unit (that is connected to an external electricity supply), and Thermo King equipment produced by Petters Ltd., who have a stand at the exhibition.
The Duramin company is also exhibiting an ISO 40ft container insulated with 4in. polyurethane blocks to which glass-fibre reinforced skins are bonded internally and externally, the blocks being separated by glass-fibre reinforced ribs which connect the two skins and add strength to the structure. A 20ft insulated container is seen equipped with a Petters Slimline refrigerating unit, the use of which substantially increases the carrying capacity of the container. Other Duramin container exhibits include a 30ft bulk cargo Unit which has four roof hatches and can.be fitted with a disposable polythene lining for the carriage of cargoes susceptible to contamination.
A light-alloy 40ft by 8ft by 8ft 6in, container shown by Cravens Homalloy (Sheffield) Ltd. is of special interest by virtue of a "tunnel" type of floor construction this is also a feature of the new Crane Fruehauf 40ft Seatrain container), which provides for a saving in height when it is being carried on a Gooseneck type of trailer. In this case there is no increase in overall vehicle height compared with a vehicle carrying 8ft high containers, which is of particular value in America and some other countries where height limits are imposed. The tare and gross weights of the container are 7,000lb and 67,200Ib respectively.
Pressed glass-fibre floor bearers are used in the Cravens Homalloy 20ft light-alloy insulated container to eliminate heat-leakage paths from the interior, an under panel of aluminium being stiffened by light-alloy top-hat sections. Polyurethane insulation is foamed in situ, the lining panels being of glass-fibre, and the container is designed for refrigeration by cold air from a ship's system or by a clip-on unit which feeds in air by the same ports. Of 930 cu.ft. capacity, the container has tare and gross weights of 5,800lb and 44.800lb respectively.
Open-ended containers
Of the many containers shown having an "openings" interest, the Peak Trailers Ltd. all-steel unit is of special note because it has an open-top, sides that are open down to the level of low drop sides and an end that is open down to shallow hinged doors. In the case of an Adamson and Flatchett Great Dane openended container, the side openings are from roof to floor level and this unit has a tare weight of 5,7001b. Both these containers and a number of others are equipped with Pakamac plactics covers.
A new British Oxygen Co. Ltd. Polarstream liquid nitrogen refrigerating system is based on a horizontal system and the unit is mounted on the exterior of the front bulkhead instead of the inside of the container which affords a 100 per cent payload space. Also of special interest, a movable bulkhead is available for larger containers which enables a different temperature to be maintained on each side, which is particularly useful if a mixed load is being carried, for example of fresh and frozen foods. An axial-flow fan has been developed. designed for circulating air around tightly packed respiring loads over long distances.
Two general-purpose stainless-steel 4,000gal tanks are shown by W. P. Butterfield (Engineers) Ltd. mounted in 20ft module frames, one of which is designed for nonhazardous liquids and one for hazardous loads. Both are designed for a working pressure of 30 p.s.i.g., while the nonhazardous tank is insulated with 2in. of glassfibre overlaid with aluminium sheet. Frame design is Lloyd's approved and the frame conforms to ISO requirements.
Small containers of 45 cu.ft. and 90 cu.ft.
capacity are shown by Geetainers "S" international, 16 and eight of which respectively fit into an ISO container. And 35 cu.ft. and 70 cu.ft. Geetainers are exhibited for carrying in a 20ft ISO frame, the number that can be accommodated being 24 and 12 respectively. Of all-steel construction, all Geetainers are collapsible and the panels are interchangeable. Within a year, containers of these sizes will be built by the company in a plastics material and "one-waycardload containers will be available. Containers can be equipped with a one-way plastics pouch for the carriage of a pulverulent or liquid load, discharge being by gravity.