FREIGHT BEST PRACTICE
Page 16
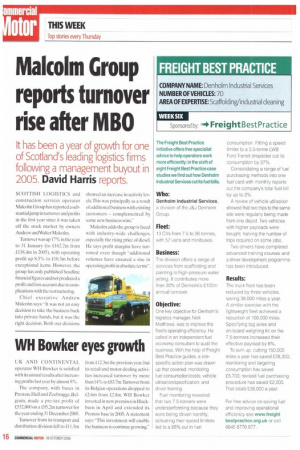
If you've noticed an error in this article please click here to report it so we can fix it.
COMPANY NAME: Den holm Industrial Services NUMBER OF VEHICLES: 70 AREA OF EXPERTISE: Scaffolding/industrial cleaning WEEK SIX
Sponsored by: -+ Freight Best Practice
The Freight Best Practice initiative offers free specialist advice to help operators work more efficiently: in the sixth of eight Freight Best Practice case studies we find out how Denholm Industrial Services cut its fuel bills.
Who: Denholm Industrial Services, a division of the J&J Denholm Group.
Fleet:
13 CVs from 7.5 to 26 tonnes, with 57 vans and minibuses.
Business:
The division offers a range of services from scaffolding and painting to high-pressure water jetting. It contributes more than 30% of Denholm's 2.100m annual turnover.
Objective:
One key objective for Denholm's logistics manager, Nick Matthews, was to improve the fleet's operating efficiency. He called in an independent fuel economy consultant to audit the business. With the help of Freight Best Practice guides, a sitespecific action plan was drawn up that covered: monitoring fuel consumption/costs; vehicle utilisation/specification; and driver training.
Fuel monitoring revealed that two 7.5-tonners were underperforming because they were being driven harshly; activating their speed limiters led to a 68% cut in fuel consumption. Fitting a speed limiter to a 3.5-tonne LWB Ford Transit dropsider cut its consumption by 27%.
Consolidating a range of fuel purchasing methods into one fuel card with monthly reports cut the company's total fuel bill by up to 2%.
A review of vehicle utilisation showed that two trips to the same site were regularly being made from one depot. Two vehicles with higher payloads were bought, halving the number of trips required on some jobs.
Two drivers have completed advanced training courses and a driver development programme has been introduced.
Results:
The truck fleet has been reduced by three vehicles, saving 38,000 miles a year. A similar exercise with the lightweight fleet achieved a reduction of 100,000 miles. Specifying tag axles and on-board weighing kit on the 7.5-tonners increased their effective payload by 6%.
To sum up, cutting 150,000 miles a year has saved £28,300; monitoring and targeting consumption has saved £5,700; revised fuel purchasing procedure has saved £2,000. That totals £36,000 a year.
For free advice on saving fuel and improving operational efficiency see www.freight bestpractice.org.uk or call 0845 8770 877.