WHAT MAKES .„ G
Page 42
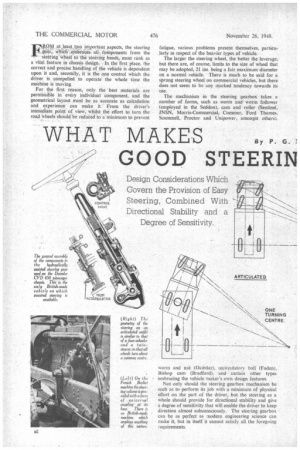
Page 43
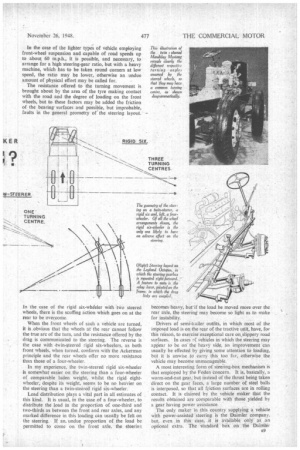
Page 44
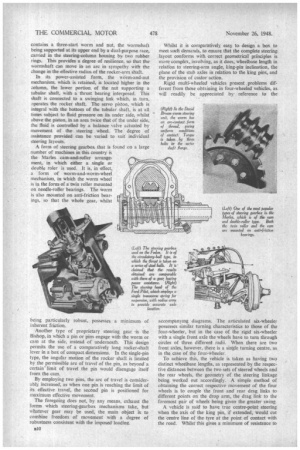
Page 47
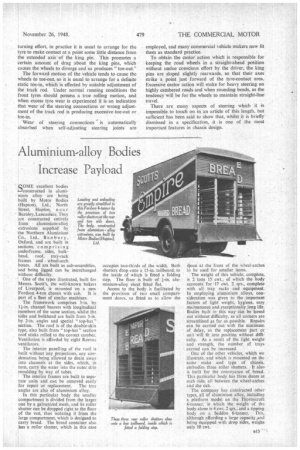
If you've noticed an error in this article please click here to report it so we can fix it.
KER
FROM ats1cag,tyr9 important aspects, the steering gear, Which L t tii b fa ce s all . components from the
stetting Wheel to "the steering heads, mist rank as a vital feature in chassis design. In the first place. the correct and precise handling of the vehicle is dependent upon it and, secondly, it is the one control which the driver is compelled to operate" the whole time the machine is moving For the first reason, only the best materials are permissible in eviry individual component, and the geometrical layout must be as accurate as calculation and . experience can make it From the driver's immediate point of view, whilst the effort to turn the road wheels should be reduced to a minimum to prevent worm and mit (Daimler), recirculatory ball (Foden), Bishop cam (Bradford), and certain other types embracing the vehicle maker's own design features.
Not only should the steering gearbox mechanism be such as to perform its job with a minimum of physical effort on the part of the driver, but the steering as a whole should provide for directional stability and give a degree of sensitivity that will enable the driver to keep direction almost subconsciously. The steering gearbox can be as perfect as modern engineering science can make it, but in itself it cannot satisfy all the foregoing requirements.
fatigue; various problems present themselves, particularly in respect of the heavier types of vehicle.
The larger the steering wheel, the better the leverage, but there are, of course, limits to the size of wheel that may be adopted, 21 ins, being a fair maximum diameter on a normal vehicle. There is much to be said for a sprung steering wheel on commercial vehicles, but there does not seem to be any marked tendency towards its use.
The mechanism in the steering gearbox takes a number of forms, such as worm and worm follower (employed in the Seddon), cam and roller (Sentinel, JNSN, Morris-Commercial, Comtner, Ford Thames, Scammell, Proctor and Unipower, amongst others), in the case of the lighter types of vehicle employing front-wheel suspension and capable of road speeds up to about 60 m.p.h., it is possible, and necessary, to arrange for a high steering-gear ratio, but with a heavy machine, which has to be taken round corners at low speed, the ratio may be lower, otherwise an undue amount of physical effort may be called for.
The resistance offered to the turning movement is brought about by the area of the tyre making contact with the road and the degree of loading on the front wheels, but to these factors may be added the friction of the bearing surfaces and possible, but improbable, faults in the general geometry or the steering layout.
In the case of the rigid six-wheeler with two steered wheels, there is the scuffing action which goes on at the rear to be overcome.
When the front wheels of such a vehicle are turned, it is obvious that the wheels at the rear cannot follow the true arc of the turn, and the resistance offered by the drag is communicated to the steering. The reverse is the case with -twin-steered rigid six-wheelers, as both front wheels, when turned, conform with the Ackerman principle and the rear wheels offer no more resistance than those of a four-wheeler.
In my experience, the twin-steered rigid six-wheeler is somewhat easier on the steering than a four-wheeler of comparable laden weight, whilst the rigid eightwheeler, despite its weight, seems to be no heavier on the steering than a twin-steered rigid six-wheeler.
Load distribution plays a vital part in all estimates of this kind. It is usual, in the case of a four-wheeler, to distribute the load in the proportion of one-third and two-thirds as between the front and rear axles, and any marked difference in this loading can usually be felt on the steering. If an undue proportion of the load be permitted to come on the front axle, the steerine becomes heavy, butlf the load be moved more over the rear axle, the steering may become so light as to make for instability.
Drivers of semi-trailer outfits, in which most of the imposed load is on the rear of the tractive unit, have, for this reason, to exercise exceptional care on,slippery road surfaces. In cases r:q vehicles in which the steering may appear to be on the heavy side, an improvement can usually be effected by giving some attention to loading, but it is unwise to carry this too far, otherwise the vehicle may become unmanageable.
A most interesting form of steering-box mechanism is that employed by the Foden concern. It is, basically, a worm-and-nut gear; but instead of the thrust being taken direct on the gear faces, a large number of steel balls is interposed, so that all friction surfaces are in rolling contact. It is claimed by the vehicle maker that the results obtained are comparable with those yielded by a gear having power assistance.
The only maker in this country supplying a vehicle with power-assisted steering is the Daimler company, but, even in this case, it is available only as an optional extra. The statidafd box on the Daimler contains a three-start worm and nut, the worinshaft being supported at its upper end by a dual-purpose race, carried in the steering-column housing by two rubber rings. This provides a degree of resilience, so that the wormshaft can move in an arc in sympathy with the change in the effective radius of the rocker-arm shaft.
In its power-assisted form, the worm-and-nut mechanism, which is retained, is located higher in the column, the lower portion of the nut supporting a tubular shaft, with a thrust bearing interposed. This shaft is connected to a swinging link which, in turn, operates the rocker shaft. The servo piston, which is integral with the battom of the tubular shaft, is at all times subject to fluid pressure on its under side, whilst above the piston, in an area twice that of the under side, the fluid is controlled by a balance valve actuated by movement of the steering wheel. The degree of • assistance provided can be varied to suit individual steering layouts.
A form of steering gearbox that is found on a. large
number of machines in this country is the Manes cam-and-roller arrange ment, in which either a single or double roler is used. It is, in effect, a form of worm-and-worm-wheel mechanism, in which the worm wheel is in the form of a twin roller mounted on needle-roller bearings. The worm is also mounted on anti-friction bearings, so that the whole gear, whilst being particularly robust, possesses a minimum of inherent friction.
Another type of proprietary steering gear -is the Bishop, in which a pin or pins engage with the worm or cam at the side, instead of underneath. This design permits the use of a comparatively long rocker-shaft lever in a box of compact dimensions. In the single-pin type, the angular motion of the rocker shaft is limited by the permissible are of travel of the pin, as beyond a certain' limit of travel the pin would disengage itself from the cam.
By employing two pins, the arc of travel is considerably increased, as when one pin is reaching the limit of its effective travel, the second pin is positioned for maximum effective movement.
The foregoing does not, by any means, exhaust the forms which steering-gearbox mechanisms take, but whatever gear may be used, the main object is to combine freedom of movement with a degree of robustness consistent with the imposed loading.
Whilst it is comparatively easy to design a box to meet such demands, to ensure that the complete steering layout conforms with. correct geometrical principles is more complex,. involving, as it does,, wheelbase length in relation to steering-arm angle; king-pin inclination, the plane of the stub axres in relation to the king pins, and the provision of castor action.
Rigid multi-wheeled vehicles present .problems different from those obtaining in fOur-wheeled vehicles, as will readily be appreciated by. reference to the accompanying diagrams. The articulated six-wheeler possesses similar turning characteristics to those of the four-wheeler, but in the case of the rigid six-wheeler with a single front axle the wheels have to turn through circles of three different radii. When there are two front axles, however, there is a single turning centre, as in the case of the four-wheeler.
To achieve this, the vehicle is taken as having two distinct wheelbase lengths, as represented by the respective distances between the two sets of steered wheels and the rear wheels, the geometry of the steering linkage being worked out accordingly. A simple method of obtaining the correct respective movement of the four wheels is to couple the front and rear drag links to different points on the drop arm, the drag link to the foremost pair of wheels being given the greater swing.
A vehicle is said to have true centre-point steering when the axis of the king pin, if extended, would cut the -centre line of the tyre at the point of contact with the road. Whilst this gives a minimum of resistance to
turning effort, in practice it is usual to arrange for the tyre to make contact at a point some little distance from the extended axis of the king pin. This promotes a certain amount of drag about the king pins, which causes the wheels to diverge and so produces "toe-out."
The forward motion of the vehicle tends to cause the wheels to toe-out, so it is usual to arrange for a definite static toe-in, which is effected by suitable adjustment of the track rod. Under normal running conditions the front tyres should possess a true rolling motion, and when excess tyre wear is experienced it is an indication that wear of the steering connections or wrong adjustment of the track rod is producing excessive toe-out or Wear of steering connections is automatically absorbed when self-adjusting steering joints are employed, and many commercial vehicle makers now fit them as standard practice.
To obtain the castor action which is responsible for keeping the road wheels in a straight-ahead position without undue conscious effort by the driver, the king pins are sloped slightly rearwards, so that their axes strike a point just forward of the tyre-contact area. Excessive castor action will make for heavy steering on highly cambered roads and when rounding bends, as the tendency will be for the wheels to maintain straight-line travel.
There are many aspects of steering which it is impossible to touch on in an article of this. length, but sufficient has been said to show that, whilst it is briefly dismissed in a specification, it is one of the most important features in chassis design.