Watch the washers
Page 123
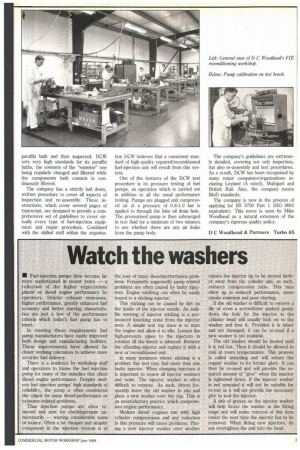
If you've noticed an error in this article please click here to report it so we can fix it.
• Fuel-injection pumps have become far more sophisticated in recent years — a reflection of the higher expectations placed on diesel engine performance by operators. Stricter exhaust emissions, higher performance, greatly enhanced fuel economy and better starting characteristics are just a few of the performance criteria which today's fuel pump has to meet.
In meeting these requirements fuel pump manufacturers have vastly improved both design and manufacturing facilities. These improvements have allowed far closer working tolerances to achieve more accurate fuel delivery.
There is a tendency by workshop staff and operators to blame the fuel injection pump for many of the maladies that affect diesel engine performance. Despite modem fuel injection pumps' high standards of reliability, the pump is often considered the culprit for many diesel-performance or economy-related problems.
Thus injection pumps are often removed and sent for checking/repair unnecessarily — wasting considerable sums of money. Often a far cheaper and simpler component in the injection system is at the root of many diesel/performance problems. Frequently supposedly pump related problems are often caused by faulty injectors. Engine misfiring can often be easily traced to a sticking injector.
This sticking can be caused by dirt on the inside of the injector nozzle. An audible warning of injector sticking is a pronounced knocking noise from the injector area. A simple test top trace is to start the engine and allow it to idle. Loosen the high-pressure pipes to the injectors in rotation till the knock is silenced. Remove the offending injector and replace it with a new or reconditioned unit.
In many instances where sticking is a problem this test may find more than one faulty injector. When changing injectors it is important to renew all injector washers and seals. The injector washer is often difficult to remove. As such, fitters frequently leave the old washer in situ and place a new washer over the top. This is an unsatisfactory practice which compromises engine performance.
Modern diesel engines run with high cylinder compressions and any reduction in this pressure will cause problems. Placing a new injector washer over another causes the injector tip to be moved further away from the cylinder and, as such, reduces compression ratio. This may show up in reduced performance, more smoke emission and poor starting.
If the old washer is difficult to remove a file or even a screwdriver pushed gently down the hole for the injector in the cylinder head will usually lock on to the washer and free it. Provided it is intact and not damaged, it can be re-used if a new washer is not available.
The old washer should be heated until it is red hot. Then it should be allowed to cool at room temperatures. This process is called annealing and will return the copper washer to its former glory. It can then be re-used and will provide the required amount of "give" when the injector is tightened down. If the injector washer is not annealed it will not be suitable for re-use as it will not provide the necessary give to seal the injector.
A dab of grease on the injector washer will help locate the washer at the fitting stage and will make removal of this item easier the next time the injector has to he removed. When fitting new injectors, do not overtighten the unit into the head.