24-hour SI Modern Quantity-production Methods fir Vehicles Demand that Girling,
Page 51
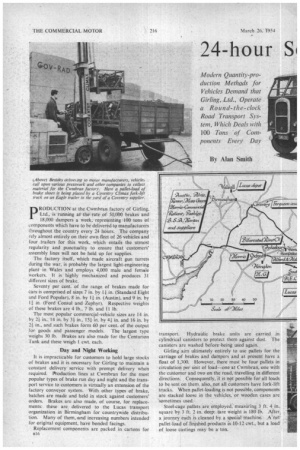
If you've noticed an error in this article please click here to report it so we can fix it.
Ltd., Operate a Round-the-clock Road Transport System, Which Deals with 100 Tons of Components Every Day
By Alan Smith
pRODUCTION at the Cwmbran factory of Girling. Ltd., is running at the rate of 50,000 brakes and 18,000 dampers a week, representing '100 tons of components which have to be delivered to manufacturers throughout the country every 24 hours. The company rely almost entirely on their own fleet of 26 vehicles and four trailers for this work, which entails the utmost regularity and punctuality to ensure that customers' . assembly lines will not be held up for supplies.
The factory itself, which made aircraft gun turrets during the war, is probably the largest light-engineering plant in Wales and employs 4,000 male and female Workers. It is highly mechanized and produces 31 different sizes of brake.
Seventy per cent. of the .range of brakes made for cam is comprised of sizes 7 in. by 11 in. (Standard Eight and Ford Popular), 8 in. by 11 in. (Austin), and 9 in. by in. (Ford Consul and Zephyr). Respective weights of these brakes are 4 lb., 7 lb. and Ii lb.
The most popular commercial-vehicle sizes are 14 in. by 21 in.. 14 in. by 31 in., 151 in. by 41 in. and 16 in. by 21 in., and such brakes form 60 per cent, of the output for goods and passenger models. The largest type weighs 30 lb. Brakes are also made for the Centurion Tank and these weigh 1 cwt. each.
Day and Night Working
It is impracticable for customers to hold large stocks of brakes and it is necessary for Girling to maintain a constant delivery service with prompt delivery when required. Production lines at Cwmbran for the most popular types of brake run day and night and the transport service to customers is virtually an extension of the factory conveyor system. With other types of brake, batches are made and held in stock against customers' orders. Brakes are also made, of course, for replacements: these are delivered to the Lucas transport
organization in Birmingham for countrywide distribution. Many of them, and increasing numbers intended for original equipment, have bonded facings.
Replacement components are packed in cartons for 1 6
transport. Hydraulic brake units are carried in cylindrical canisters to protect them against dust. The canisters are washed before-being used again.
Girling aim ultimately entirely to use pallets for the carriage of brakes and dampers and at present have a float of 1,300. However, there must be four pallets in circulation per Unit of load-one at Cwmbran, one with the customer and two on the road, travelling in different directions. Consequently, it is not possible for all loads to be sent on them, also, not all customers have fork-lift trucks. When pallet-loading is not possible, components are stacked loose in the vehicles, or wooden cases are sometimes used.
Steel-cage pallets are employed, measuring 3 ft. 4 in.. square by 3 ft. 2 in. deep: tare weight is 180 lb. After. a journey each is cleaned by a special machine. A net pallet-load of fin,ished products is 10-12 cwt., but a load' of loose 'castings may be a ton.