Cleaners' Fleet Must Work 24 Hours a Day
Page 30
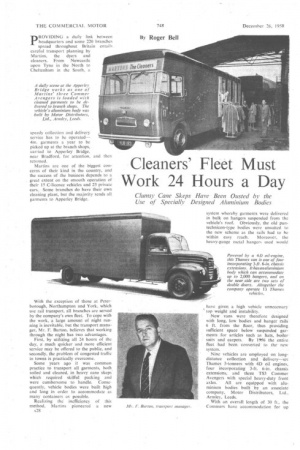
Page 31
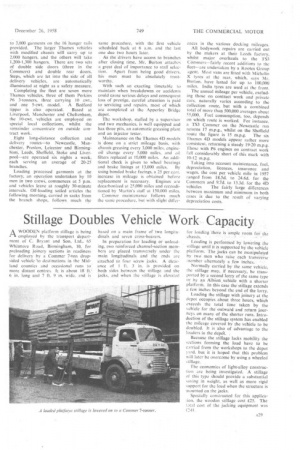
If you've noticed an error in this article please click here to report it so we can fix it.
Clumsy Cane Skeps Have Been Ousted by the Use of Specially Designed Aluminium Bodies
pROVIDING a daily link between headquarters and some 220 branches spread throughout Britain entails careful transport planning by Martins, the dyers and cleaners. From Newcastle upon Tyne in the North to Cheltenham in the South, a
speedy collection and delivery service has to be operated4m. garments a year to be picked up at the branch shops, carried to Apperley Bridge. near Bradford, for attention, and then returned.
Martins are one of the biggest concerns of their kind in the country, and the success of the business depends to a great extent on the smooth operation of their 15 C-licence vehicles and 23 private cars. Some branches do have their own cleaning plant, but the majority sends all garments to Appertey Bridge.
With the exception of those at Peterborough, Northampton and York, which use rail transport, all branches are served by the company's own fleet. To cope with the work, a large amount of night running is inevitable, but the transport manager, Mr. F. Burton, believes that working through the night has two advantages.
First, by utilizing all 24 hours of the day, a much quicker and more efficient service may be offered to the public, and secondly, the problem of congested traffic in towns is practically overcome.
Some years ago it was common practice to transport all garments, both soiled and cleaned, in heavy cane skeps which required skilful packing and were cumbersome to handle. Consequently, vehicle bodies were built high and Icing in order to accommodate as many containers as possible.
Realizing the inefficiency of this method, Martins pioneered a new A28 system whereby garments were delivered in bulk on hangers suspended from the vehicle's roof. Obviously, the old pantechnicon-type bodies were unsuited to the new scheme as the rails had to he within easy reach. Moreover, the heavy-gauge metal hangers used would have given a high vehicle unnecessary top weight and instability.
New vans were therefore designed with long, low bodies and hanger rails • 6 ft. from the floor, thus providing sufficient space• below suspended garments for articles such as hats, boiler
• suits and Carpets. By 1966 the entire. fleet had been converted to the new system.
Nine vehicles are employed on longdistance collection and delivery—six Thames 3-tonners with 4D oil engines, four incorporating 3-ft. 6-in, chassis extensions, and three TS3 Cormner Avengers with special heavy-duty front axles. All are equipped with aluminium bodies built by an associate company, Motor Distributors, Ltd., Arm ley, Leeds.
With an overall length of 30 ft., the Commers have accommodation for up to 3,000 garments on the 16. hanger rails provided. The larger Thames vehicles with modified' chassis Will carry up to 2,000 hangers, and the others will take 1,200-1,300 hangers. There are two sets of double side doors (three in the Comrners) and double rear doors. Steps, which are let into the side of all delivery vehicles, are automatically illuminated, at night as a safety measure.
Completing the fleet are seven more Thames vehicles, three of them Perkins P6 3-tonners, three carrying 10 cwt., and . one 5-cwt. model. A Bedford tipper is also operated. Based at Liverpool. Manchester and Cheltenham, the 10-cwt. vehicles are employed on special local collections, " whilst the remainder concentrate on outside contract work.
. Eight long-distance collection and delivery routes—to Newcastle, Manchester, Preston, Leicester and Birmingham, Leeds, Sheffield, Stoke and Liverpool—are operated six nights a week, each serving an average of 20-25 branches.
Loading processed garments at the factory, an operation undertaken by 10 men in two crews, commences at 5 p.m. and vehicles leave at roughly 30-minute intervals. Off-loading soiled articles the following morning, carried in sacks from the branch shops, follows. much the
same procedure, with the first vehicle scheduled back at 6 a.m. and the last one due two hours later.
AS the drivers have access to branches after closing time, Mr. Button attaches a great deal of importance to staff selec tion. Apart from being good drivers. his men must be absolutely trustworthy.
With such an exacting timetable to maintain when breakdowns or accidents could cause serious delays and consequent Loss of prestige, careful attention is paid to servicing and repairs, most of which are completed at the Apperley Bridge depot.
The workshop, staffed by a supervisor and two mechanics, is well equipped and has three pits, an automatic greasing plant and an injector tester.
Maintenance on the Thames 4D models is done on a strict mileage basis, with chassis greasing every 3,000 miles. engineMI Change every 5,000 miles, and oil filters replaced at 10,000 miles. An additional check is given to wheel bearings and brake linings at 13,000 miles. By using bonded brake facings, a 25 per cent. increase in mileage is obtained before replacement is necessary. Engines are decarbonized at 25.000 miles and reconditioned by Martin's staff at 150,000 miles.
Commer maintenance follows much the same procedure, but with slight differ
ences in the various docking mileages.
All bodywork repairs are carried out by the Makers at their Leeds factory, whilst major overhauls to the TS3 COmmers—fairly recent additions to the fleet—are undertaken by a Rootes Group agent. Most vans are fitted with Michelin X tyres at the rear, which, says Mr. Burton, have lasted for up to 100,000 miles. India tyres are used at the front.
The annual mileage per vehicle, excluding those on contract work and private cars, naturally varies according to the collection route, but with a combined total of more than 500,000 averages about 55,000. Fuel consumption, too, depends on which route is worked. For instance, a TS3 Commer on the Newcastle run returns 17 m.p.g., whilst on the Sheffield route the figure is 15 m.p.g. The six Thames 4D models appear rather more consistent, returning a steady 19-20 m.p.g. [hose with P6 engines on contract work Fall considerably short of this mark with 10-12 m.p.g.
Taking into account maintenance, fuel, depreciation, licences, insurance and wages, the cost per vehicle mile in 1957 ranged from 18.5d. to 24.6d. for the Commers and 9.7d. to 13.3d. for the 4D vehicles The fairly large differences between maximum and minimum in both cases is due to the result of varying depreciation costs.