Austin's 500hp turbine would have given trucks 'car performance
Page 53
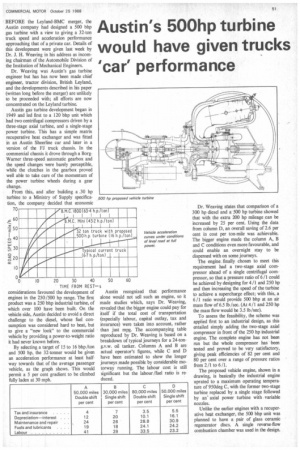
If you've noticed an error in this article please click here to report it so we can fix it.
BEFORE the Leyland-BMC merger, the Austin company had designed a 500 bhp gas turbine with a view to giving a 32-ton truck speed and acceleration performance approaching that of a private car. Details of this development were given last week by Dr. J. H. Weaving in his address as incoming chairman of the Automobile Division of the Institution of Mechanical Engineers.
Dr. Weaving was Austin's gas turbine engineer but has has now been made chief engineer, tractor division, British Leyland, and the developments described in his paper (written long before the merger) are unlikely to be proceeded with; all efforts are now concentrated on the Leyland turbine.
Austin gas turbine development began in 1949 and led first to a 120 bhp unit which had two centrifugal compressors driven by a three-stage axial turbine, and a single-stage power turbine. This has a simple matrix recuperative heat exchanger and was fitted in an Austin Sheerline car and later in a version of the FJ truck chassis. In the commercial chassis it drove through a BorgWarner three-speed automatic gearbox and the speed changes were barely perceptible, while the clutches in the gearbox proved well able to take care of the momentum of the power turbine wheels during a gear change.
From this, and after building a .30 hp turbine to a Ministry of Supply specification, the company decided that economic considerations favoured the development of engines in the 250/500 hp range. The first product was a 250 bhp industrial turbine, of which over 100 have been built. On the vehicle side, Austin decided to avoid a direct challenge to the diesel, whose fuel consumption was considered hard to beat, but to give a new look" to the commercial vehicle by providing a power-to-weight ratio it had never known before.
By selecting a target of 15 to 16 bhp/ton and 500 hp, the 32-tonner would be given an acceleration performance at least halfway towards that of the average passenger vehicle, as the graph shows. This would permit a 5 per cent gradient to be climbed fully laden at 30 mph. Austin recognized that performance alone would not sell such an engine, so it made studies which, says Dr. Weaving, revealed that the bigger engine could pay for itself if the total cost of transportation (especially labour, capital outlay, tax and insurance) were taken into account, rather than just mpg. The accompanying table reproduced by Dr. Weaving is based on a breakdown of typical journeys for a 24-tong.v.w. oil tanker. Columns A and B are actual operator's figures, while C and D have been estimated to show the longer journeys made possible by considerable motorway running. The labour cost is still significant but the labour /fuel ratio is reduced. Dr. Weaving states that comparison of a 300 hp diesel and a 500 hp turbine showed that with the extra 200 hp mileage can be increased by 25 per cent. Using the data from column D, an overall saving of 2.6 per cent in cost per ton-mile was achievable. The bigger engine made the column A, B and C conditions even more favourable, and could enable an overnight stay to be dispensed with on some journeys.
The engine finally chosen to meet this requirement had a two-stage axial compressor ahead of a single centrifugal compressor, so that a pressure ratio of 6/1 could be achieved by designing for 4/1 and 250 hp and then increasing the speed of the turbine to achieve a supercharge effect; with this, a 6/1 ratio would provide 500 bhp at an air mass flow of 6.5 lb/sec. (At 4/1 and 250 hp the mass flow would be 3.5 lb/sec).
To assess the feasibility, the scheme was applied first to an industrial design, as this entailed simply adding the two-stage axial compressor in front of the 250 hp industrial engine. The complete engine has not been run but the whole compressor has been tested and proved to be very satisfactory, giving peak efficiencies of 82 per cent and 80 per cent over a range of pressure ratios from 2/I to 6/1.
The proposed vehicle engine, shown in a drawing, is basically the industrial engine uprated to a maximum operating temperature of 950deg C, with the former two-stage turbine replaced by a single stage followed by an axial power turbine with variable nozzles.
Unlike the earlier engines with a recuperative heat exchanger, the 500 bhp unit was planned to have a pair of glass ceramic regenerator discs. A single reverse-flow combustion chamber was used in the design.